GAUTSCHI MASTERmax.
EBNER.blog | Stefan Pelech, Gautschi
Gautschi MASTER max.
ALUMINIUM RECYCLING für Krätze und Schrott mit hohem organischem Anteil.
Beim Wiedereinschmelzen von metallischem Aluminium benötigt man 10- bis 15-mal weniger Energie als bei der Herstellung von Aluminiummetall aus Bauxit. Grund genug, jedes Stück Aluminium, das nicht oder nicht mehr verwendet werden kann, zu sammeln und dem Schmelzprozess zuzuführen. Mit jedem Kilogramm gesammeltem Aluminium werden somit etwa 15 kg CO₂-Ausstoß vermieden.
Schrott
Je nach Anwendung fällt Aluminiumschrott in unterschiedlichsten Formen und mit unterschiedlichen Verunreinigungen an. Bevor er also dem Schmelzofen zugeführt werden kann, muss er sortiert und so weit wie möglich gereinigt werden. Ist der Schrott großstückig
und frei von organischen Verunreinigungen, wird er in Einkammeröfen geschmolzen, zum Beispiel im GAUTSCHI SRF (Schmelzofen Rund Feststehend) oder SVF (Schmelzofen Viereckig Feststehend) Ofentypus.
Ist der Schrott großstückig zum Beispiel Profile, Platten, Gussteile oder kleinstückig, wie Späne oder geschredderte Dosen beinhaltet aber geringfügige organische Verunreinigungen wie, Öl, Lack oder Plastik, sind speziell angepasste Mehrkammeröfen oft die beste Wahl,
zum Beispiel der GAUTSCHI SMF (Schmelzofen Mehrkammer Feststehend).
Krätze
Aluminium, insbesondere wenn es heiß und flüssig ist, oxidiert sehr schnell. In einem Schmelzofen bildet sich daher eine Haut von Aluminiumoxid an der Oberfläche des Schmelzbades. Diese Haut nennt man „Krätze“ und wird vor der Weiterverarbeitung abgezogen, oder abgeschöpft. Das Aluminiumoxid ist porös und saugt metallisches Aluminium wie ein Schwamm an. Daher besteht Krätze zu einem großen Teil (30-70%) aus metallischem Aluminium, welches wiedergewonnen werden sollte.
Innovatives Aluminium-Recycling für eine nachhaltige Zukunft
Für Krätze und Schrotte mit hohen organischen Verunreinigungen, die besonders schwierig zu schmelzen sind, werden Dreh-Kipp-Öfen (DKO) verwendet, in denen ähnlich wie in einem Betonmischer die Einsatzmaterialien mit Schmelzsalz vermischt und aufgeheizt werden, um sie kontrolliert und mit hoher Ausbeute aufschmelzen zu können.
Der GAUTSCHI MASTERmax ist das Produkt, das Aluminium-Recycling komplettiert. Entwickelt von KMF, ist dieser kippbare Drehtrommelofen bestens geeignet zum Schmelzen von beispielsweise Dosenschrott, Krätzen und Spänen. Durch permanente Temperaturmessungen des Abgasstroms und die Möglichkeit, den Schmelzprozess mit Sauerstoffeindüsung zu optimieren, erreicht der DKO höchste Wirkungsgrade – maximale Metallausbeute bei minimalem Energieverbrauch. Denn die organischen Verunreinigungen, die mit dem Schrott in den Ofen gelangen, werden statt Erdgas als Energielieferant zum Schmelzen im Ofen genutzt.
Effizienz und Leistung im Einklang
Der Drehtrommelofen beeindruckt nicht nur durch seinen geringen Platzbedarf, sondern auch durch seine robuste Bauweise, die den täglichen Einsatz im anspruchsvollen Casthouse-Betrieb ermöglicht. Über die in der MELTmax-Steuerung hinterlegten Schmelzrezepturen kann der Bediener den gesamten tap-totap-Prozess kontrolliert automatisiert durchführen. Im Sinne von Industrie 4.0 sichert die Steuerung definierte Schrottzusammensetzungen und darauf individuell abgestimmte Schmelzprogramme, die die Balance zwischen Energieverbrauch und Schmelzleistung gewährleisten.
Anpassungsfähigkeit für vielfältige Anforderungen
Erfahrene Bediener können die Leistung manuell feinabstimmen, während Anfänger dank des hohen Automatisierungsgrads und der Schmelzrezepturen reproduzierbare Ausbringungsleistungen und Prozesssicherheit erreichen. Die Hybridkonstruktion des MASTERmax ermöglicht den Betrieb des Ofens mit unterschiedlichen Schmelzprozessen:
- Der Salzprozess mit horizontal fixierter Achse, im Zuge dessen so viel Schmelzsalz zugeführt werden kann, dass die Schlacke flüssig wird, was für besonders dünnwandigen Schrott notwendig ist.
- Der salzarme Prozess mit variabler Achse (kippbar), bei dem trockene, „bröselige“ Schlacke entsteht, die am Ende des Zyklus aus dem Ofen gekippt werden kann.
- Der salzfreie Prozess, der vor allem beim reinem Krätzerecycling angewendet werden kann.
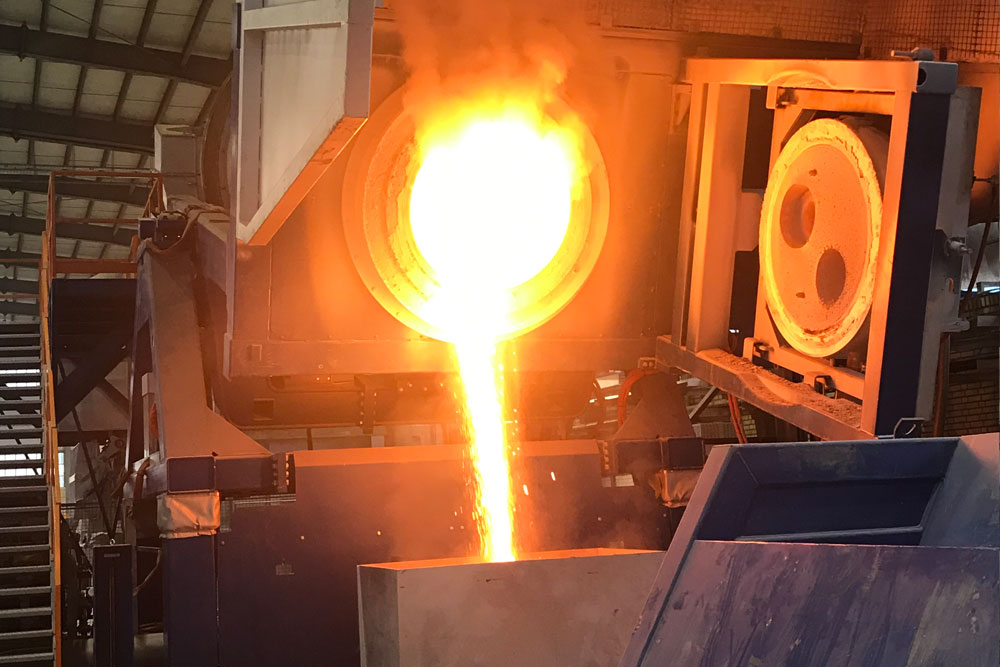
Intelligente Automatisierung und Flexibilität
Das technisch auf maximale Automatisierung ausgelegte Schmelzaggregat ermöglicht reproduzierbare
Schmelzergebnisse bei höchster Ausbringungseffizienz und optimiertem thermischen Wirkungsgrad. Eine präzise Ofenverwiegung in Echtzeit sowie permanente Temperaturmessung des Schmelzbads sind wichtige Alleinstellungsmerkmale, mit der der Automatisierungsgrad deutlich höher ist als bei Produkten des Mitbewerbs.
Eine einzigartige Eigenschaft des MASTERmax ist sein Ansatz, das flüssige Metall bei geschlossener Ofentür über ein Abstichloch am Ofenboden kontrolliert abzuziehen, um Oxidation zu minimieren und die Aluminiumtemperatur während des gesamten Abstichvorgangs konstant zu halten. Sämtliche Prozessdaten können in den Casthouse-Leitstand integriert oder mittels Chargenprotokollen einzeln aus der Steuerung abgerufen werden.
Größenvielfalt der MASTERmax Serie
Die Öfen der GAUTSCHI MASTERmax Serie gibt es in 5 Baugrößen: vom kompakten Einstiegsmodell wie dem 1TR2 mit 2 MW Brenner und 4 Tonnen Kapazität bis hin zum leistungsstarken „Jumbo DKO“ mit 5 MW Brenner, der eindrucksvolle 50 Tonnen flüssiges Aluminium bereitstellt.
Die Vorteile des MASTERmax: Praktische Innovation
Durch das innovative double-pass Abgassystem ist keine thermische Nachverbrennung standardmäßig erforderlich. Der verarbeitete Aluminiumschrott kann damit etwa 8% organische Bestandteile (Öl, Lack, Plastik) enthalten. Optional kann jedoch eine thermische Nachverbrennungsanlage hinzugefügt werden, um lokalen Umweltanforderungen besser zu entsprechen, auch wenn sogar Schrotte mit noch höheren organischen Anteilen chargiert werden sollen. Die stufenlos verstellbare Flammenlänge des Brenners optimiert den
Energieverbrauch und gewährleistet eine gleichmäßige Temperaturverteilung. Der verstellbare Neigungswinkel der Ofentrommel von -8° bis +25° ermöglichen eine optimale Nutzung der Ofengeometrie. Die vollautomatische 360° drehbare Chargiermulde füllt den Ofen gleichmäßig entlang der Ofenlängsachse, ermöglicht einen nahezu luftdichten Chargiervorgang, während gleichzeitig die Feuerfestauskleidung geschont wird. Kapazitäten von bis zu 7 Tonnen pro Ladung ermöglichen eine optimale Taktung. Die daraus resultierenden kurzen Chargierzeiten minimieren die Exposition der Schmelze gegenüber der Umgebungsluft und reduzieren die Oxidation des metallischen Aluminiums. Der Abstich unter der Schlacke bei geneigtem Drehtrommelofen erhält die Reinheit des Aluminiums. Eine mitkippende Abgashaube verhindert Rauchaustritt in die Hallenumgebung während dem Auskippen der Schlacke.
Schlacke kühlen
Schlacke – der Reststoff des Drehofenprozesses – besteht in jedem Fall aus Aluminiumoxid, je nach Schmelzprozess aus mehr oder weniger Schmelzsalz (NaCl und KCl) und aus diversen Metalloxiden. Da die Auftrennung zwischen metallischem Aluminium und Schlacke im Drehofen nicht zu 100% erfolgen kann, ist gleich nach dem Ofenzyklus noch typischerweise etwa 10% metallisches Aluminium in der Schlacke vorhanden.
Nach dem Abkippen hat Schlacke eine Temperatur von etwa 1000°C oder mehr. Lässt man sie im Schlackenbehälter stehen, wird das metallische Aluminium weiter oxidieren, was an einem weiteren Anstieg der Schlackentemperatur erkennbar ist. Das geschieht so lange, bis kein metallisches Aluminium mehr übrig ist. Diese Oxidation lässt sich stoppen, wenn man die Schlacke unter 400°C zwangskühlt. Je schneller man das schafft, desto mehr metallisches Aluminium verbleibt in der Schlacke und kann in der Folge durch Wirbelstromabscheider wiedergewonnen werden. Der von KMF entwickelte COOLmax Schlackenkühler, kühlt die Schlacke innerhalb weniger Minuten unter die erforderlichen 400°C. Gleichzeitig wird die Schlacke zu einer Korngröße gemahlen, die die spätere Abscheidung der Aluminium- “Nuggets“ mit Wirbelstrom ermöglicht.
CO₂-Betrachtung
In den Aluminiumgießereien weltweit fallen jährlich geschätzt 4 Mio Tonnen Krätze an. Rechnen wir mit einem Metallgehalt von ~50%, wird durch Krätzerecycling etwa 1,7Mio t Aluminium wiedergewonnen, wobei durch schnelles Abkühlen der Schlacke weitere 300 000 t Aluminium wiedergewonnen werden könnten. 2 Mio t Sekundäraluminium statt derselben Menge Primäraluminium bedeutet eine Einsparung von ~30Mio t CO2 pro Jahr. 4,5 Mio t davon allein durch ausreichende Schlackenkühlung.
Klicken Sie hier, um mehr über Gautschi zu erfahren.