GAUTSCHI MASTERmax.
EBNER.blog | Stefan Pelech, Gautschi
Gautschi MASTER max.
ALUMINUM RECYCLING for dross and scrap with high organic content.
Remelting metallic aluminum requires 10 to 15 times less energy than producing aluminum metal from bauxite. This is reason enough to collect every bit of aluminum that is unused or cannot continue in use and add it to a melting process. Every kilogram of aluminum that is collected prevents the emission of around 15 kg of CO2.
Scrap
Depending its original application, aluminum scrap may come in a wide variety of shapes and bring with it a wide variety of contaminants. It must therefore be sorted and cleaned as thoroughly as possible before it can be placed in a melting furnace. If the scrap is in large pieces and free of organic contaminants, it can be melted in a single-chamber furnace such as the GAUTSCHI type SRF (Schmelzofen Rund Feststehend or “melting furnace, oval, fixed hearth”) or type SVF (Schmelzofen Viereckig Feststehend or “melting furnace, rectangular, fixed hearth”) furnaces. For scrap that is either in large (profiles, plates, cast parts) or small pieces (chips, shredded can scrap) and contains trace amounts of organic contaminants such as oil, paint or plastic, specially-adapted multi-chamber furnaces are often the best choice. An example of such a furnace would be the GAUTSCHI SMF (Schmelzofen Mehrkammer Feststehend, or “melting furnace, multi-chamber, fixed hearth”).
Dross
Aluminum oxidizes very rapidly, particularly when it is hot and in a liquid state. This causes a skin of alumina (aluminum oxide) to form on the surface of the molten metal in a melting furnace. This skin is called “dross”, and is either removed or skimmed off before processing is continued. Alumina is porous, and absorbs metallic aluminum like a sponge. For this reason, a large percentage (30 – 70 %) of the dross is comprised of metallic aluminum that should be recovered if possible.
Innovative aluminum recycling for a sustainable future
For dross and scrap with high levels of organic contaminants, materials that are particularly difficult to melt, rotary tilting furnaces (RTF, in German DKO or Dreh- Kipp-Öfen) are used. In these furnaces, the charged material is mixed with a salt flux in a manner similar to a cement mixer and heated. This allows the charge to be melted in a controlled manner, providing higher yields. The GAUTSCHI MASTERmax is the product that rounds out aluminum recycling needs. Developed by KMF, this rotary tilting furnace is extremely well-suited for melting can scrap, dross and chips. By continuously measuring the temperature of the stream of exhaust gas and allowing the melting process to be optimized through the injection of oxygen, this RTF achieves the highest possible efficiencies – maximum metal yields paired with minimal energy consumption. Instead of natural gas, the organic contaminants that enter the furnace with the scrap are used to supply energy used for the melt in the furnace.
Efficency and performance go hand-in-hand
This rotary furnace does not just impress with the small
amount of space it requires. Also impressive is its robust design, which enables it to operate day in and day out in the most demanding casthouse environments. Using the melting recipes stored in the MELTmax control system, operators can automate the entire process in a controlled manner. As dictated by the guidelines of Industry 4.0, the control system ensures that the composition of scrap is defined and that melting programs are individually tailored to suit that composition. This ensures that the balance between energy consumption and melting performance is maintained.
Adaptability for varying requirements
Experienced operators can manually fine-tune the performance, while newer ones are assured of reproducible yields and highly stable processes thanks to the high degree of automation and the melting recipes. The hybrid design of the MASTERmax system enables to the furnace to be operated with a wide variety of melting processes, including:
- A salt process with a fixed horizontal axis, during which enough salt flux can be added to liquefy the slag. This measure is necessary when the scrap has particularly thin walls.
- A low-salt process with a variable axis (tiltable), during which a “crumbly” dry slag forms. This dross can be tipped out of the furnace at the end of the cycle.
- A salt-free process, which is of particular use when recycling uncontaminated dross.
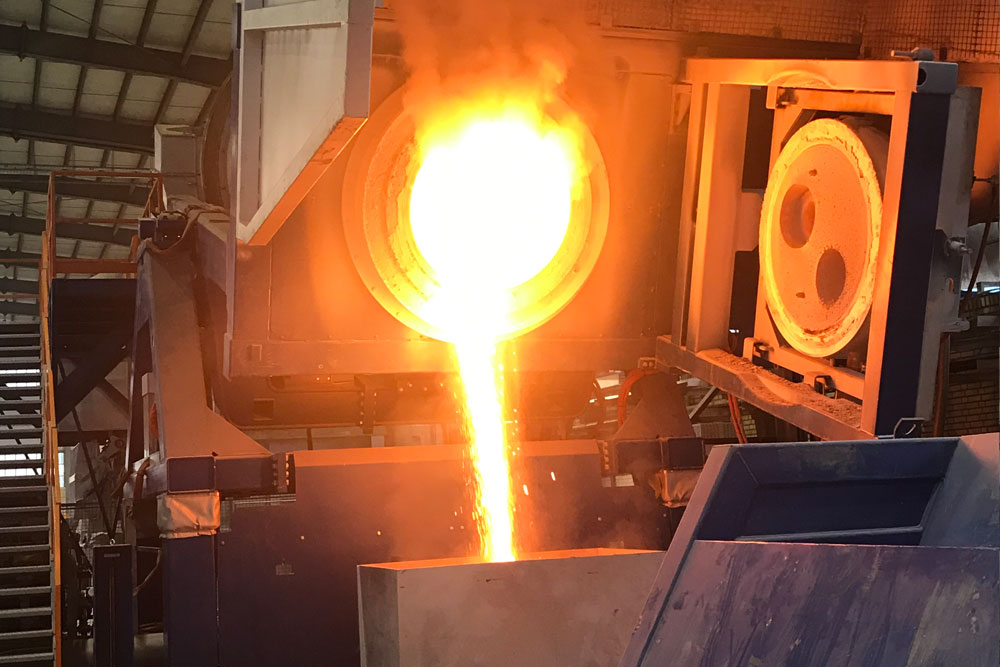
Intelligent automation and flexibility
The melting unit, with technical features designed to allow a maximum amount of automation, provides reproducible results paired with the highest possible yields and optimized thermal efficiency. Precise weighing of the furnace in real time, along with continuous measurement of the temperature of the molten metal, are unique features that provide a degree of automation that is significantly higher than that of competing products.
Another unique approach taken by the MASTERmax is the ability to draw out liquid metal in a controlled manner through a tap hole in the furnace door, while the furnace door remains closed. This minimizes oxidation and keeps the temperature of the aluminum constant during the entire tapping procedure. All process data can be integrated into the casthouse control center, or called up out of the control system individually using charge reports.
Sizes available in the MASTERmax series
Furnaces in the GAUTSCHI MASTERmax series are available in five sizes. They range from a compact, entry-level model like the 1TR2, with 2 MW burners and a 4-ton capacity, to the powerful “Jumbo RTF”, which is equipped with 5 MW burners and which can supply an impressive 50 ton of molten aluminum.
The advantage of MASTERmax: practical innovation
Due to the innovative double-pass system for exhaust gas, a thermal outburner is not standard required equipment. With the system, up to around 8 % of the aluminum scrap that is processed can be organic components (oil, paint, plastic). A thermal burnout system can, however, be added as an optional extra to better comply with local environmental regulations, even if scrap with even higher percentages of organic components is to be charged. The infinitely variable flame length of the burner optimizes energy consumption, and ensures a uniform temperature distribution, The adjustable tilt of the furnace drum, which can be varied between -8° and +25°, allows optimal use of the furnace geometry. The fully automatic, fully rotating (360°) charging cradle evenly fills the furnace along its longitudinal axis and ensures that the charging procedure is virtually airtight, even as it protects the refractory lining at the same time. Capacities of up to 7 tons per load allow optimal timing. The short charging times that result minimize the exposure of the melt to ambient air, and so reduce the amount of oxidation of the metallic aluminum. Tapping below the slag, with the rotating drum tilted, maintains the purity of the aluminum. An exhaust gas hood that tilts with the furnace prevents the escape of exhaust into the casthouse while the slag is being poured out.
Cooling the slag
Slag – the residue of the rotary furnace process – is comprised of alumina, a greater or lesser amount of salt flux (NaCl or KCl) that depends on the melting process that was employed, and other metal oxides. As the metallic aluminum and slag cannot be 100 % separated in the rotary furnace, around 10 % of the slag is typically composed of metallic aluminum after the furnace cycle.
After tilting, the slag has a temperature of 1000 °C or more. If the slag is allowed to remain in the slag container, the metallic aluminum will continue to oxidize. This can be recognized by the fact that the temperature of the slag will rise even further. Oxidation will continue until there is no metallic aluminum remaining, but can be stopped if the slag is cooled down to below 400 °C. The faster this can be carried out, the more metallic aluminum will remain in the slag. This aluminum can subsequently be recovered using an eddy current separator.
The COOLmax slag cooler developed by KMF requires only a few minutes to cool the slack down to the required temperature of 400 °C. At the same time, the slag is ground into grains of a size that allows aluminum “nuggets” to be separated out of it later using eddy currents.
Carbon considered
Throughout the world, aluminum casthouses create an estimated 4 million tons of dross. If we assume a metal content of ~ 50 %, the recycling of dross would reclaim about 1.7 million metric tons of aluminum. The rapid cooling of slag would allow an additional 300,000 metric tons of aluminum to be reclaimed.
Two million metric tons of secondary aluminum instead of the same amount of primary aluminum means a savings of almost ~ 30 million metric tons of CO2 per year. 4.5 million metric tons would be provided by the adequate cooling of slag alone!
Click here to learn more about Gautschi.