Heat Treatment Technology for Wire Rod and Drawn Wire.
EBNER.blog | Peter Seemann, Sascha Eppensteiner, EBNER
Heat Treatment Technology for Wire Rod and Drawn Wire
Hot-rolled and Stelmore-cooled wire rod are the starting materials for a number of processes and high-quality products.
The first time a coil of wire rod is heat treated it usually undergoes a spheroidization anneal, where the as-cast hot-rolled microstructure is optimized for additional cold forming. The excellent temperature uniformity that is achieved in HICON/H2® furnaces is essential for successfully annealing wire coils heat treated above the Ac1 temperature, particularly with highly-alloyed grades.
Thanks to the high heat transfer coefficients, the necessary transformation energy is transferred all the way through to the center of a compact wire coil. Both the exterior and interior windings of the coil thus show similar temperature profiles throughout the course of the anneal, leading to extremely uniform mechanical properties – particularly when high alloy grades are annealed above the Ac1 temperature.
Cold-drawn wire
With HICON/H2® technology, cold-drawn wire can easily be recrystallized in pure hydrogen. Depending on the grade of steel, operating temperatures may vary between 660 °C and 860 °C.
Hydrogen’s ability to transfer heat, along with its cleaning properties, promotes the evaporation of lubricants. Automatic atmosphere control programs flush the evaporated drawing compounds out of the workload space during the heating-up phase. Both at the end of the heating-up phase and at the end of cooling, the temperature scatter throughout the charge stack remains minimal. The graph shown below compares heat treatment of a 44 t stack of wire in nitrogen atmosphere with heat treatment in hydrogen atmosphere. When nitrogen is used as the process atmosphere, a throughput of only 1.8 t/h can be achieved. A hydrogen process atmosphere provides 2.6 t/h. Along with the fact that heat treatment in a hydrogen atmosphere takes less time, there is also a significant difference in the surface finish of the two compact coils: the coil annealed in hydrogen has a significantly better finish.
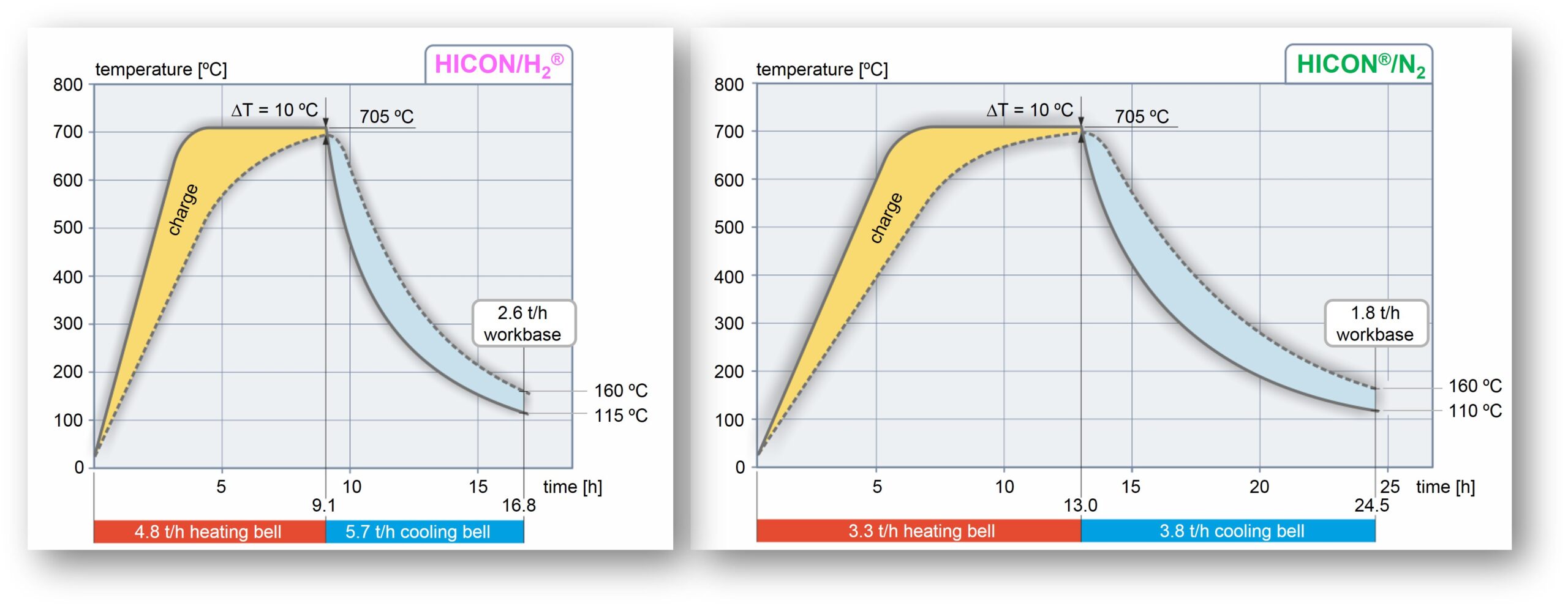
Lightweight construction and atmosphre flow
Workbases designed to heat treat steel wire (see image below) are distinguished not only by their lightweight construction, which they combine with excellent load support, but also by optimized gas flow throughout the entire volume containing the charge – which they combine with extremely high speeds of gas flow. Concentric support rings and segmented plates are used to reduce the weight of the diffuser/load plate assembly. The light weight of this assembly provides an improved and more even flow of gas across the entire surface bearing the charge.
Special fan impellers, developed by EBNER, have intakes with an increased cross-sections. This allows extremely high speeds and recirculation of extremely high volumes of gas: up to 50 m3/s. The combination of lightweight construction, optimized gas flow and high gas speeds enables the shortest possible annealing times.
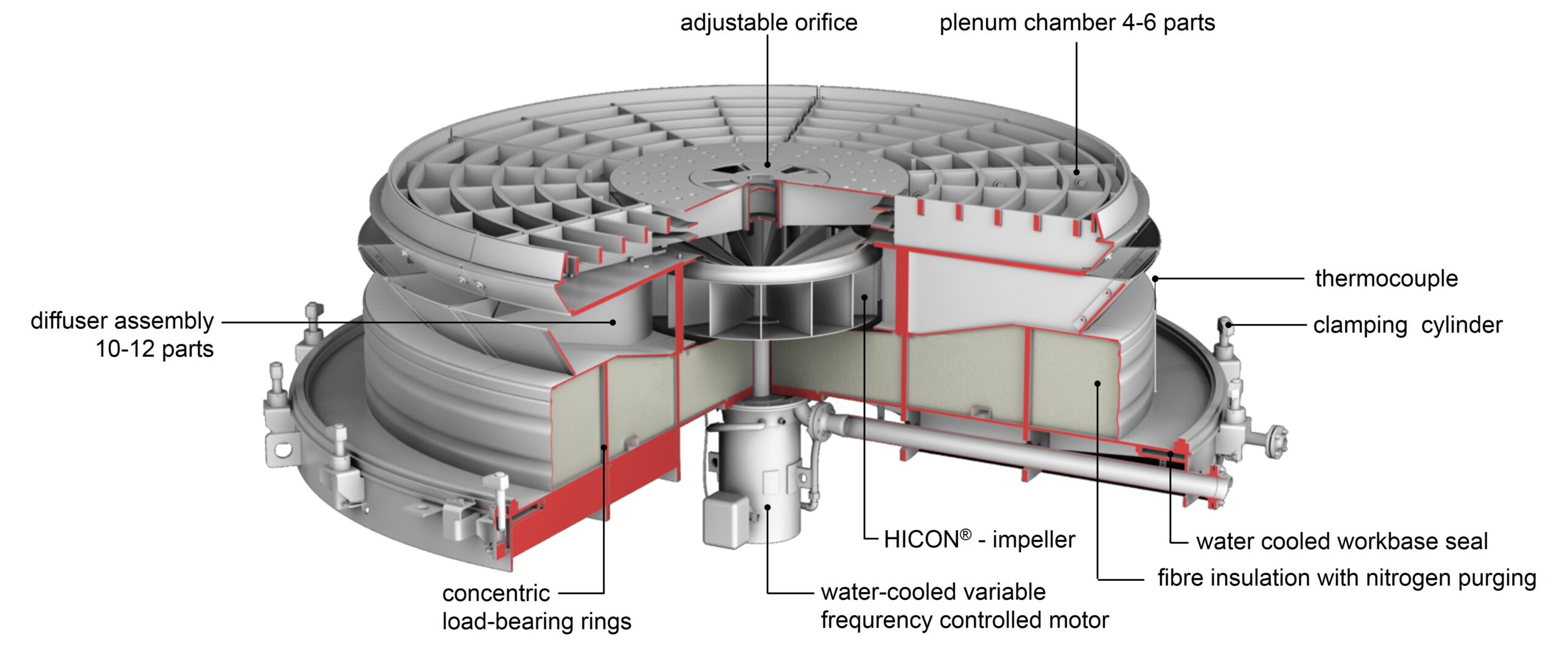
ATMOSPHEREperfect
The ATMOSPHEREperfect software module is an automatically-controlled purging program. It is easily activated by checking a box in the visualization system (see image below). An automatically-calculated purging segment is located in segment 1 of the atmosphere track, so that the atmosphere can be replaced with 100 % H2 as quickly as possible. Automatic H2 control is found in segment 2. The preset flowrate of 15 m³/h is the minimum purge flowrate. This is maintained until the minimum purging time has expired, unless control by the ATMOSPHEREperfect module is required. The purge flowrate is automatically regulated in response to evaporating drawing compounds and lubricants. Evaporation is detected by noting an increase in the power draw of the workbase fan while the speed has remained constant. That is, the module calculates the optimal current draw with a 100 % H2 atmosphere at a given temperature.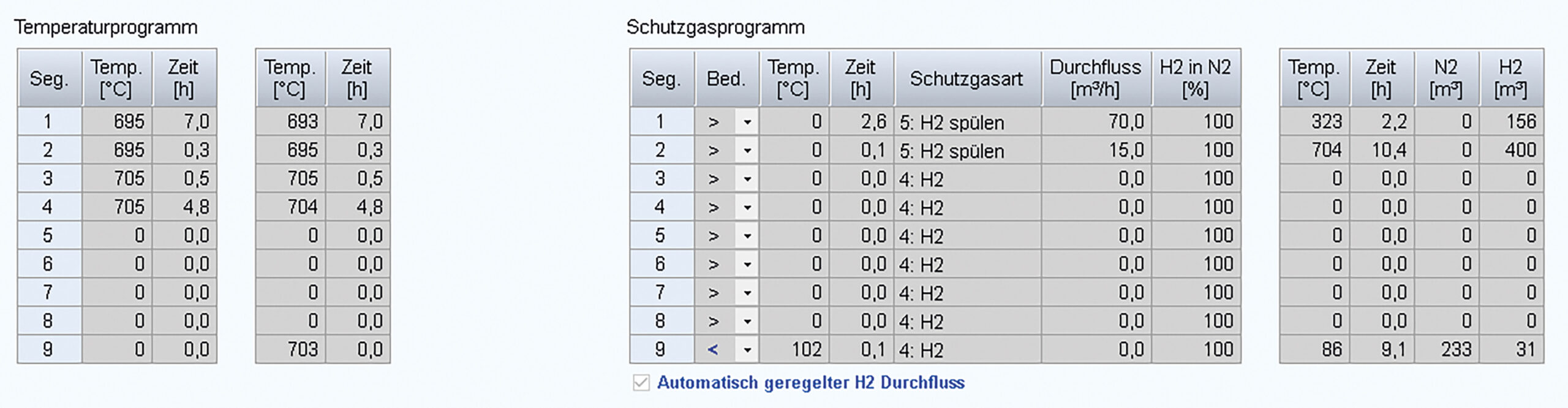
Encapsulation of the process chamber
The inner cover provides all-metal encapsulation of the process chamber and allows special atmospheres to be used in the workload space, without the admixture of exhaust gases or ambient air. The inner cover is exposed to temperatures over 1000 °C, as well as a high number of temperature cycles and thermal shocks. To prevent distortion, EBNER inner covers are always corrugated. It is also crucial to select the right material, as the combination of oxidizing exhaust gas on the outside of the cover and the reducing atmosphere on the inside can thin the material. A baffle system is located inside the inner cover to direct the flow of gas inside the workload space. This prevents the gas flow from short-circuiting or moving in irregular patterns, optimizing heat transfer.
ECOBURN Flex: Special Burners for operation with natural gas and hydrogen
To reduce the emission of pollutants such as NOx and CO2, EBNER is constantly advancing its proprietary burner technology. Our goal is to provide extremely low NOx emission values (< 100 mg/m³ @ 3% O2, figure 4), even as H2 combustion offers a carbon-neutral (at least on a local level) method of heating. ECOBURN FLEX burners can operate with either type of fuel gas (natural gas or hydrogen), and automatically switch to flameless operation as soon as a certain heating bell temperature is exceeded. During flameless operation, using natural gas as a fuel at max. heating power results in NOx values below 50 mg/m3. When using H2, they are below 70 mg/m3.
When ECOBURN FLEX burners are compared with the models of burner currently standard in the industry, NOx values can be reduced by about 30 % when in flame mode. The first production anneals using H2 as a fuel gas have already been successfully completed.
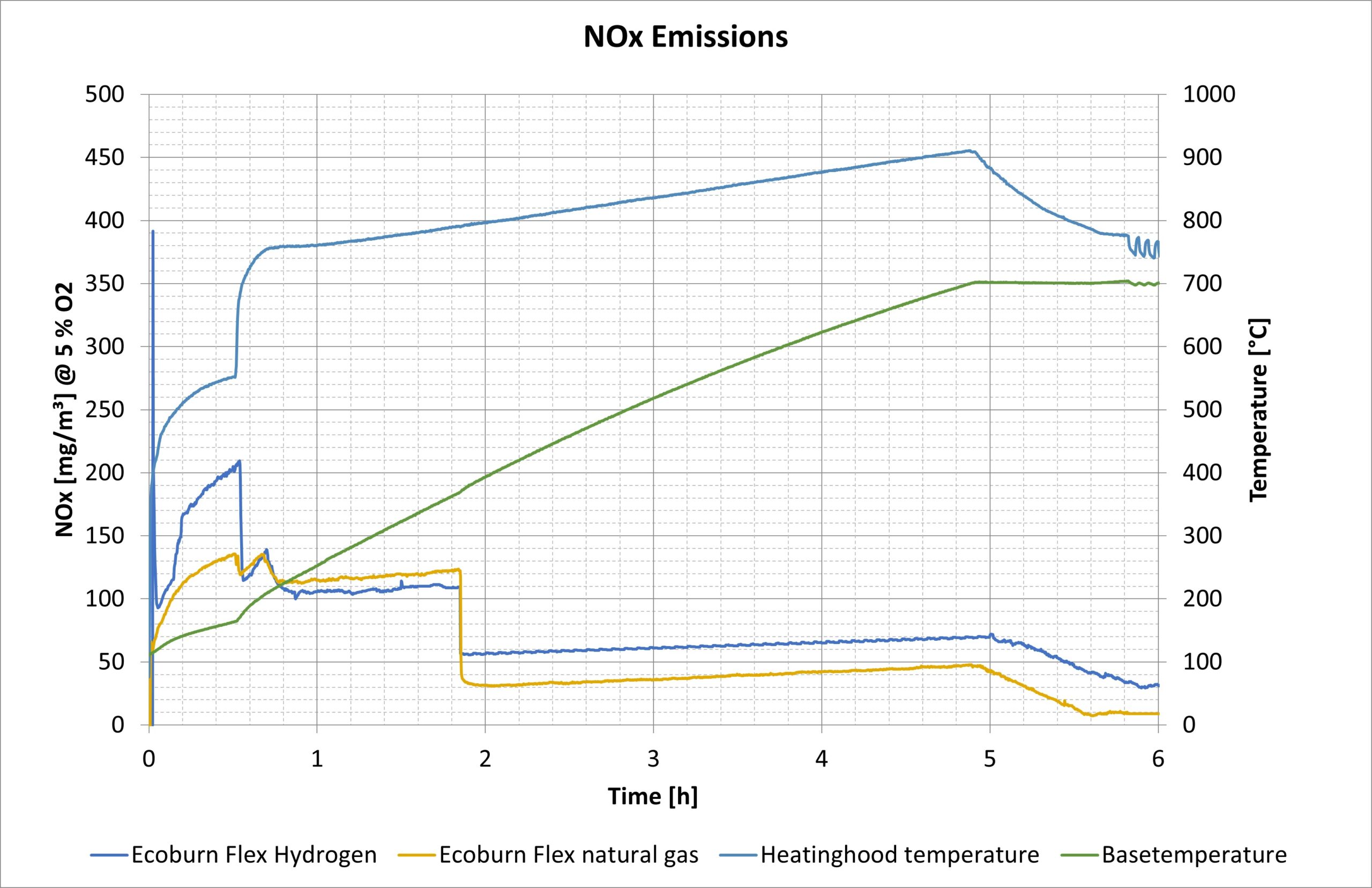
Putting it all together
EBNER bell annealers are distinguished by cutting-edge technology that is constantly being improved. Ground-breaking innovations have already been made to reduce atmosphere consumption (ATMOSPHEREperfect) and to improve burner technology (ECOBURN FLEX). Our furnaces feature the lowest energy consumption, the lowest emissions, the highest throughput and are extremely flexible. When annealed in an EBNER bell annealer, steel wire is of a quality that ensures the reliability of downstream processes: it has a homogenous microstructure, uniform mechanical properties, no additional decarburization, no additional grain boundary oxidation and an ultra-clean surface finish thanks to optimized atmosphere flow and sophisticated process control. Over 4.800 HICON bell annealers – of which around 500 are for wire – are in service throughout the world.