Copper: A Material with Potential.
EBNER.blog | Anton Oppermann, EBNER | Ryan Gore, HAZELETT
Copper: A Material with Potential.
Flexible EBNER facilities for every type of semifinished product provide our customers with the highest efficiency and best possible quality.
Coper enabling technological progress
Copper has been in use for over 10,000 years, and entire periods of human history such as the chalcolithic or the bronze age have been named after it. Today, electrification and digitalization have led it to become even more important than ever.
Copper’s outstanding electrical and thermal conductivity, far superior to that of any other technologically relevant material, are the keys to its success. It also has excellent formability and corrosion resistance, and other properties such as hardness can be easily influenced with alloying elements.
The combination of these characteristics means that copper has a wide range of economical applications for every type of electrical facility, as well as in fields such as mechanical and plant engineering, power generation, telecommunications and mobility. Copper has allowed us to achieve our current level of technological progress, an age of electrification and digitalization.
Copper: Advancing Green Technologies
Copper is becoming increasingly important and the demand for it is rising due to increasing global energy consumption, as well as the need to meet climate goals and successfully transition to renewable energy. Copper is thus often considered a critical resource.
Every type of renewable energy, particularly wind power and solar energy, relies on copper. For example, electric vehicles require around four times as much copper as conventional vehicles. Every prediction thus shows that the demand for copper will rise sharply in the next few years. Copper can also be easily recycled: over half of Europe’s annual requirements are already being filled by recycled material.
Miniaturization: Driving the Growth of High-Strength Copper Alloys
Due to the trend toward increased miniaturization, high-performance copper alloys are increasingly being developed and used. These alloys are precipitation hardened and exhibit high strengths. In many sectors of the electronics industry, for example consumer electronics or electric vehicles, there is an increasing demand for high-strength copper alloys. A good example of this is the USB-C plug for smartphones, tablets and other devices, which will become standard in the EU in 2024. This type of plug contains high-strength copper alloy strip and foil (less than 0.15 mm thick), which creates the electrical connection between the cable and the plug socket.
Plug connections must be as small as possible while still providing a continuous electrical connection. Along with high strength, the material that is used must also be to retain its stress relaxation properties. Put simply, this means that the contacts must retain their strength under frequent use.
The contacts are usually manufactured by stamping them, though those with particularly delicate structures are manufactured using a photochemical etching process. A metallic coating is often applied to the strip and foil that is used, e.g. using a tinplating process.
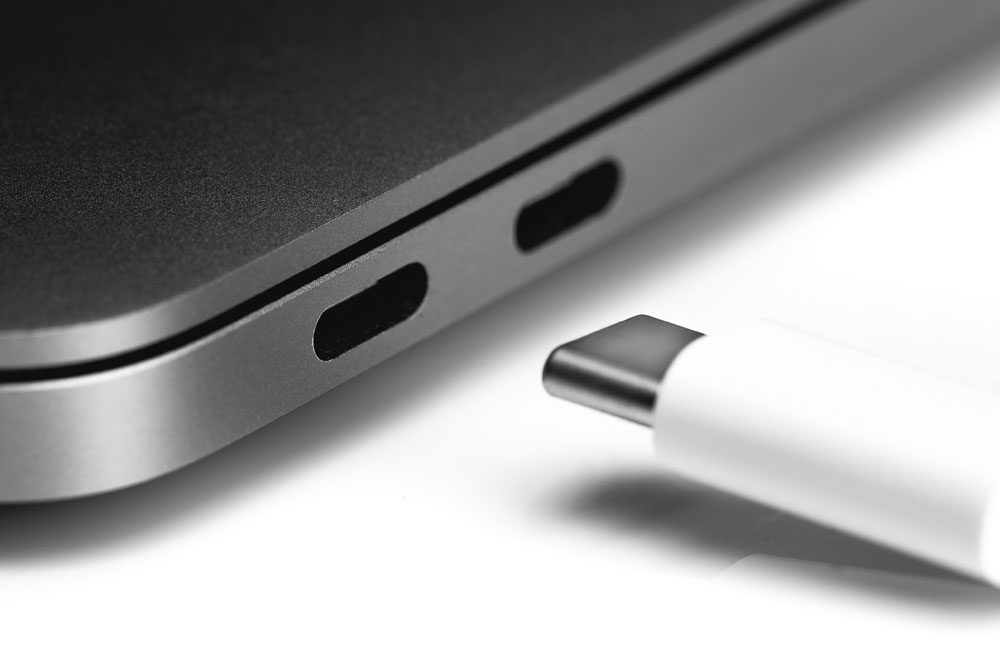
Bright Annealing Lines for Copper and Copper Alloys
The fact that the demand for copper is predicted to increase is also reflected in the increasing amount of interest in annealing capacity for high-performance alloys (also referred to as high-temperature alloys). These alloys are primarily processed in Asia, where a significant fraction of the electronics industry is based.
The proven design of an EBNER vertical bright annealing line allows copper and copper alloy strip to be heat treated in atmospheres containing a large proportion of hydrogen. This type of facility is particularly suited for high-performance copper alloys, which require extremely high processing temperatures. Following cold rolling, thin strip and foil up to 0.05 mm thick is heated up to target temperature in a jet tunnel and a radiant heating zone. It is then quenched in hydrogen atmosphere, a process that is extremely uniform. EBNER‘s integrated strip cleaning system optimally prepares the strip for heat treatment or a downstream process (e.g. passivation). Extremely high strengths can be achieved by heat treating the strip in an adjacent facility, for example by precipitation hardening it in a HICON® bell annealer.
Employment of a HICON/H2® muffle ensures that the temperature is extremely uniform and that the material is optimally protected from oxidation. An excellent strip geometry and uniform mechanical properties are achieved. The combination of muffle and verticallyoriented design allows the strip to be heated up and cooled without coming into contact with facility components. Paired with precise regulation of the strip tension, this ensures that the surface of the strip remains bright and free of damage even as optimal strip geometry is achieved. These features allow the manufacture of components with extremely small geometries for the electronics industry.
These facilities can be heated with state-of-the-art, low-emission natural gas burners, zero-carbon hydrogen burners or zero-emission electric heating systems.
HAZELETT
The EBNER Group offers solutions for processing every type of semi-finished copper product. A wide variety of heat treatment facilities can be supplied, from roller-hearth furnaces for rod and bar to bell annealers for strip and wire and vertical bright annealing lines. HAZELETT has been a member of the EBNER GROUP since 2021, meaning that the Group’s product line includes continuous casting equipment.
The development of HAZELETT technology for casting copper base materials began over 90 years ago, and it has become an extremely efficient, eco-friendly casting process. Constant improvements made to the technologies and designs, as well as the accumulation of know-how concerning the process, have been the keys to success. HAZELETT copper casting facilities deliver products that are of the highest possible quality, even as they ensure that production costs are held to a minimum.
Over half of the worldwide demand for copper is for cast and rolled copper wire rod, used as a starting product in the electrical and electronics industries.
The HAZELETT twin-belt copper bar casting machine is unique in the industry. The straight-through mold produces bar that does not need to be straightened when it exits the machine. The semi-horizontal orientation of the long, narrow mold and the ability to taper the mold to accommodate shrinkage of the bar as it cools ensure the highest quality bar for in-line rolling. Bar with diameters ranging from 8 to 22 mm can be produced.
With 38 HAZELETT copper bar casting machines currently operating in 16 countries, HAZELETT customers are producing a significant amount of the world’s copper wire.
The HAZELETT twin-belt copper bar casting machine is the only continuous copper casting machine in the world that can say this. For example, the casting machine installed in a European plant is producing every major type of copper base metal, and is supplying a significant amount of Europe’s copper sheet and foil.
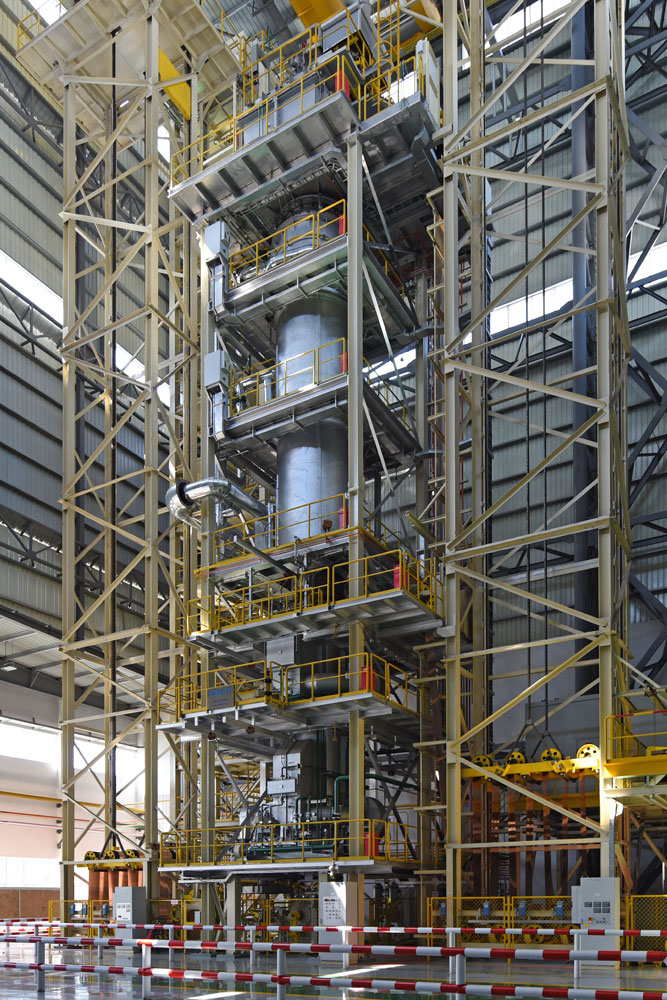