A green milestone.
/ Success Stories, Sustainability
EBNER.blog | Michael Schiesser, EBNER
A Green Milestone.
A milestone along the path to a sustainable aluminum industry has been passed by implementing state-of-the-art EBNER technology.
The global aluminum industry is currently facing one of its greatest challenges: that of making its production processes more sustainable and climate friendly. One of the most important elements in this transformation process is decarbonization, with the use of renewable energies and a reduction in CO2 emissions being key elements in the decarbonizing process. Aluminum undergoes various processes during its manufacture, with heat treatment playing a crucial role. In this particular process, industrial heat treatment facilities heat aluminum ingots, plates and coils to change the mechanical properties of the metal.
Concrete examples of decarbonization are the EBNER E³ Upgrade & Rebuild product solutions for the aluminum industry.
As far back as 2019, a customer from the aluminum industry had tasked EBNER with conducting feasibility studies on methods of decarbonizing heat treatment facilities. Over the course of these studies, various heating systems were evaluated, time and cost projections (CapEx + OpEx) were created, and overall assessments were made. With this work as a foundation, EBNER received an order this year to decarbonize a group of existing gas-fired heat treatment facilities by installing its newly developed electric heating system.
The technical aspects of decarbonization using EBNER E³ products for existing heat treatment facilities
Converting a heat treatment facility from a combustion system using fossil fuels to an alternative heating method, for example an electric heating system, is technically demanding. It requires detailed planning and meticulous implementation to ensure that a customer’s high quality requirements can continue to be met in the future. Essential steps in the conversion include:
- Analysis of energy consumptionBefore a conversion can be made, the energy consumption of the existing gas-fired plant must be determined. This analysis forms the basis forthe design of the new carbon-neutral heating system, ensuring that it can provide the required flow of thermal energy.
- Selection of heating technologyCarbon-neutral heating systems can be implemented in various forms, for example those that use resistance heating elements/cartridge heaters, those that use coiled heating elements or those that use carbon-neutral gas burners. The choice of technology depends on the specific requirements for heat treatment, the physical properties that are desired and the space avail-able in the facility.
- Integration into the existing systemsOnce selected, the new EBNER electric heating technology is integrated into an existing EBNER heat treatment facility – where it can be efficiently operated by simply supplementing the automation and control systems. Such a system is compatible with both EBNER and non-EBNER heat treatment facilities, and is easily installed as part of an upgrade.
- Commissioning and test phasesA comprehensive testing phase follows successful installation. During testing, the performance and efficiency of the facility are analyzed under real production conditions. Among other things, the high quality standards prevalent in the aluminum industry require precise temperature control; this is optimized and its performance is demonstrated during the commissioning phase.
The conversion of heat treatment facilities by rebuilding gas-fired heating systems into electric ones is an important step in decarbonizing the aluminum industry. This transformation not only benefits the environment but also offers the potential for higher efficiency, increased throughput and improved product quality. The challenges associated with a conversion can be overcome through careful planning, investing in modern technologies, and increased use of renewable energies. Over the long term, the electrification of industrial processes will play a central role in shaping sustainable and climate-friendly aluminum production processes.
In view of the global efforts being made to reduce greenhouse gas emissions, the electrification of industrial processes is becoming increasingly important. State-of-the-art EBNER E³ heating technologies, operated with renewable energy, offer a promising alternative to conventional facilities heated by burning fossil fuels. Depending upon the configuration of an existing facility, our new E³ technologies can be easily installed during a rebuild. They demonstrate that older facilities can continue to heat treat aluminum for some time to come, even in a green future.
We would be happy to discuss the ways in which emissions can be reduced at your existing heat treatment facility – please feel free to contact us!
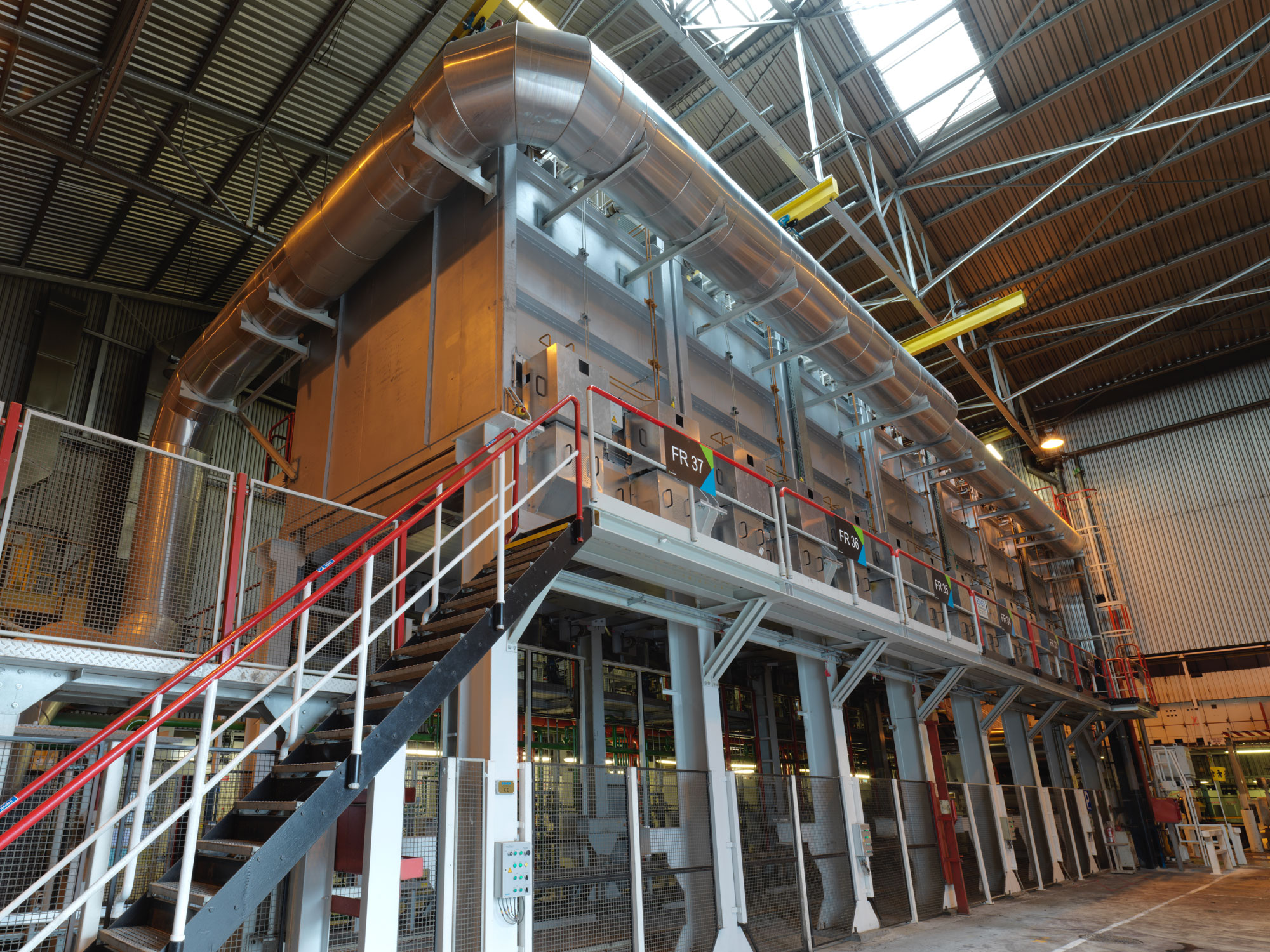