New Management at Gautschi
EBNER.blog | Stefan Pelech, Gautschi
New Management at Gatuschi
In February of this year, Stefan Pelech took over operational management of Gautschi Engineering GmbH. Together with Udo Weilerscheidt, who is responsible for the financial side of the business, he is leading the company into the future.
Stefan Pelech has over 20 years of experience in the manufacture of industrial facilities for the aluminum casting industry. For the last two years he has been responsible for developing and coordinating the EBNER GROUP’s product lines for aluminum melting and casting, with a primary focus on sustainability and recycling.
During this time, Gautschi developed a design for a multi-chamber melting furnace – complete with the components and upstream facilities required to prepare, sort and preheat scrap. Right after taking on his new management role, Stefan Pelech took the time to answer our questions.
Do you have any current goals? What would you like to achieve with Gautschi in 2024?
We would like to further strengthen our global position and continue to be a reliable partner for our customers. Positively processing every one of our customer’s orders and ensuring their full satisfaction is, of course, a prerequisite.Can we expect any changes in Gautschi’s product line?
Yes, several. For example, there is the Varega Envicom burner. This burner was developed to reduce pollutant emissions, which are regulated more and more tightly. It is a regenerative burner that is distinguished by its high efficiency, paired with extremely low CO2 emissions and an equally low level of NOx emissions. We expect that this new type of burner will be advantageous when installed in new facilities, as we will be able to set new standards for emission levels. It will also be advantageous when installed as part of a modernization package – we expect that over the next few years our customers will invest in improvements to the efficiency and eco-friendliness of their facilities.Isn’t TPS (Thermal Processing Solutions GmbH) also working on new burner technology?
Yes. TPS is a start-up that split off from Gautschi and is also based in Ranshofen. Werner Wiggen and his team at TPS are developing a method for carbon-free heating, which will be particularly suitable for aluminum melting furnaces. This method is known as a plasma jet. The patented technology is distinguished by the fact that, when inert gases such as nitrogen are used, the temperature of the plasma jet is lowered from several thousand degrees to a level comparable to that of natural gas burners. Both the amount of dross that forms and the hydrogen content of the molten metal are reduced. This is revolutionary, as all the effort that is currently required to keep the melt clean can be significantly reduced. For the multi-chamber furnaces that we are currently developing, plasma technology will be a game changer.What are multi-chamber furnaces and what are they used for?
Multi-chamber furnaces are currently used in the secondary aluminum industry to remelt aluminum scrap that has been contaminated with organic materials. This can be painted sheet and profiles, window frames with synthetic seals or foam insulation, or simply the oily chips left over after aluminum parts are machined. When the aluminum scrap averages up to around 5 % combustible components, it can be preheated in a multi-chamber furnace. The pyrolysis gases that are generated during the process can then be used as an energy source instead of natural gas. The preheated scrap, free of organic components, is then melted using an immersion melting process. This method uses the least amount of natural gas, and also provides the greatest metal yield.Is there a process for scrap that is highly contaminated?
For scrap containing up to 10 % organic contaminants, we offer the MASTERmax rotary tilting furnace. In this type of furnace, both the scrap and dross melt under a protective layer of salt flux. Over a year ago, we entered into a sales partnership with KMF to provide this technology.What happens with clean scrap?
If you need to melt clean scrap, a Gautschi round top melting furnace is the furnace of choice. Those provide unbelievably high melting rates – two years ago, I could hardly believe it myself. But it really is true that the round shape and the high output of the Varega burners allow heat to be transferred at an extremely high rate, making use of both thermal radiation and convection. In the biggest round top furnace built to date, 165 metric tons of aluminum can be melted in about 5 hours!Apart from your products for the aluminum melting sector, does Gautschi work with other metals?
We focus exclusively on aluminum. However, we do not confine ourselves to melting: we also manufacture vertical casting lines and heat treatment facilities.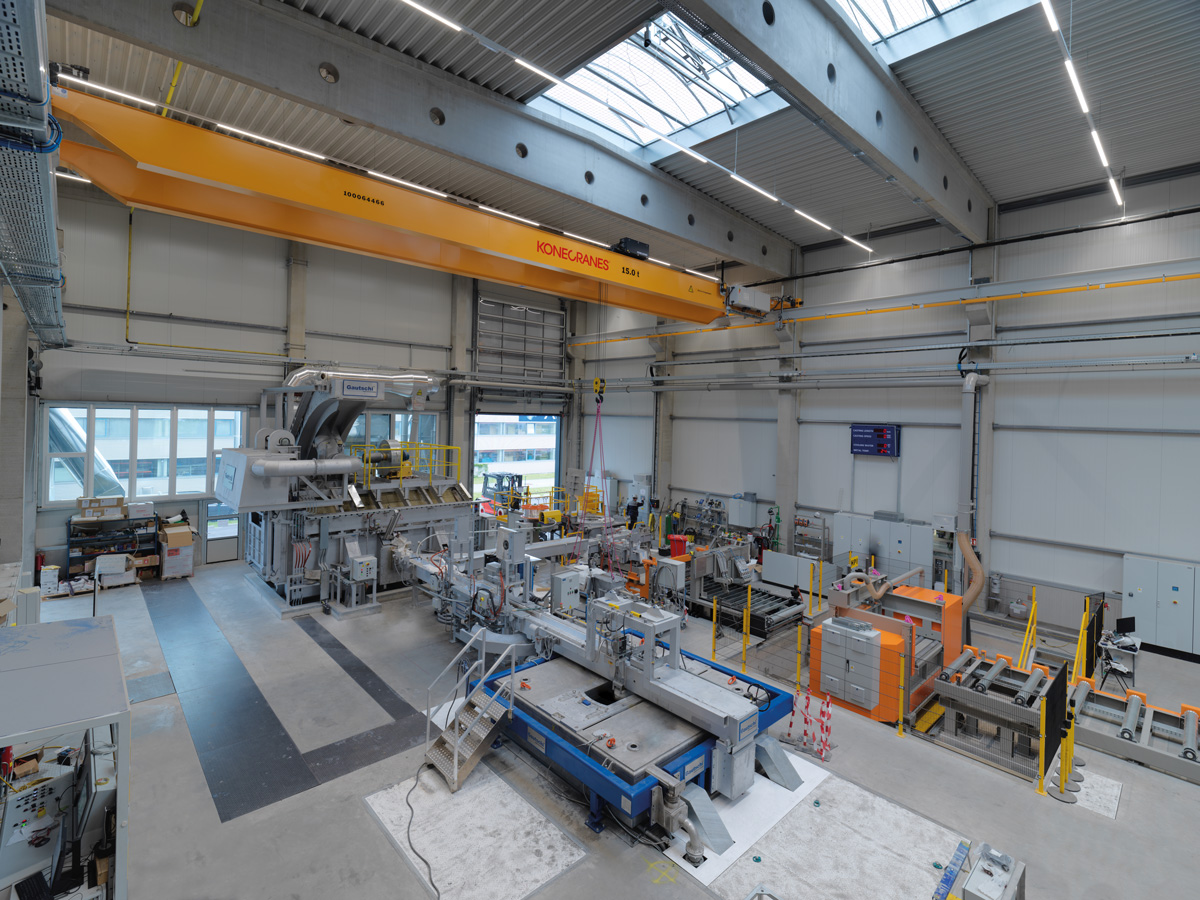
Do those have any special features?
In casting, our primary goal is to provide a “100 % hands-free” process. This enormously increases both the safety of workers in the casthouse and the security of the facility. During “hands-free” casting, no members of the casting crew are needed near the facility – from the start of the process, when the casting furnace begins to fill the launder with liquid metal, all the way up to the end when the launder is completely empty and the continuously-cast product has both solidified and cooled. Employees supervise the fully automated components remotely, from a safe control station.
We are also continuously developing mold technologies. It should be possible to cast notoriously difficult hard alloys just as easily and at the same high quality as simple “garden-variety” alloys. That should also hold true whether you are casting ingots with the Gautschi ingot mold or casting billets with the Gautschi Air Glide mold.
How and where does Gautschi develop molds?
We develop molds at our Casthouse (R)Evolution Center, known as the C-R-C. We share this casthouse with HPI, and it is equipped with both horizontal (HDC) and vertical (VDC) casters. HPI uses the HDC to develop its mold technology, while Gautschi uses the VDC for its casting trials.
You also mentioned heat treatment facilities, which are one of EBNER‘s core competencies. What does Gautschi do in this field?
In this area, we have very different product lines.
First, we offer batch-type homogenizing furnaces. These are used in casthouses to metallurgically prepare semi-finished cast products for further processing (pressing or rolling). Our furnaces stand out from the competition due to their extremely short heating-up times, the extremely uniform temperature distribution within the furnace and their coolers, with which cooling rates can be flexibly adjusted to suit the alloy being processed. Second, several years ago we developed the Compact Coil Furnace (CCF) – the most efficient and most flexible facility for heat treating sheet coils. Individual coils are heat treated in inert gas, with a minimal amount of atmosphere and energy required.
Third, we offer pusher-type and soaking pit furnaces. These are also extremely efficient and have excellent temperature regulation, and are used to bring ingots up to temperature before they are hot rolled. This is the only area in which our product range overlaps with EBNER’s.
That brings us to our last question. Gautschi is a 100 percent subsidiary of the EBNER GROUP, which means that EBNER Industrieofenbau in Leonding (Austria) is a sister company. There are a number of others, such as GNA in Canada, HPI, which is also based in Ranshofen, HAZELETT, and so on. All of these companies are active in the aluminum industry. How do they interact with one another?
The product lines of all of the sister companies you named complement one another. There is very little overlap, meaning that we do not compete with one another in the marketplace. This is a huge advantage for us, because we have access to projects and markets that we might not be able to bid for if we were operating alone. For example, we can work together with HAZELETT on a strip casting line where we supply the melting furnaces, or with HPI on a batch homogenizing facility where HPI supplies the handling and sawing equipment. For overall automation of the facilities, we can use the VISUALFURNACES 8 software suite developed by EBNER Industrieofenbau.
We can also rely on the support of EBNER Industrieofenbau when we would like to simulate atmosphere flow or during product development projects. In China, for example, the market is supported by Gautschi China. When they need to, they can fall back on the manufacturing capacity at EBNER’s workshop in Taicaing. There are many more such examples, and one of our goals is to find and exploit more of these synergies.
Thank you for taking the time to talk to us and your interesting answers, and we wish you the best of luck in the future!
Thank you too!