CASTHOUSE (R)EVOLUTION CENTER
EBNER.blog | Stefan Pelech, Casthouse (R)Evolution Center
CASTHOUSE (R)EVOLUTION CENTER
We are your casthouse for special alloys and individual demands.
The Casthouse (R)Evolution Center (C-R-C) in Ranshofen, Austria is a full-scale industrial foundry, incorporating a horizontal casting facility operated by HPI and a vertical casting facility operated by Gautschi.
Both facilities are available for customer demonstrations, alloy trials, operator training, and small, quick and/or special production runs. The facilities are also used to further develop our state-of-the-art molds and casting systems.
HPI equipment installed at the C-R-C includes a 1.7 t electric melting furnace, a rod feeder device for grain refinement and of course the heart of an HPI casthouse: a horizontal continuous casting machine (HSG) with a flying saw. This equipment offers an entire production process, from melting the base material to production of first-class semi-finished aluminum products in both round and rectangular formats.
In addition to the HPI equipment, the technology center is equipped with a 7.5 t melting furnace from Gautschi. When required, this furnace can supply the HPI casting line with liquid metal for an extended period of time. There is also a Gautschi vertical casting machine, which is capable of casting slabs and billets in any alloy and up to 6.8 m in length. This machine is supplied with material by the Gautschi melting furnace, and an inline degasser and a ceramic filter guarantee top quality.
Gautschi has been a supplier of casting machines for both billets and slabs for many years, and has several types of molds on the market. These include the well-known Gautschi billet mold, which has demonstrated its advanced quality and high performance at many locations over the last 20 years, and the recently-developed and newly-introduced Gautschi slab mold.
The proven Gautschi billet mold, based on the AirGlide® technology developed by VAW, has been a huge success thanks to its excellent surface, low segregation zone, high pit recovery and easy maintenance. Gautschi billet molds have been used to successfully cast a full range of alloys, including the most demanding aircraft alloys. It has been continuously improved over the last few years, and at the C-R-C the pilot caster is being used to optimize it even further.
The new Gautschi slab mold was developed by an international team comprised of casting experts and experienced Gautschi design engineers. Making use of their extensive experience in casting difficult and highly-demanding alloys, including slabs used in aircraft and automotive body applications, the experts focused on providing real 100 % hands-free casting, significantly less scalping scrap and significantly less butt curl for all alloys – even as they ensured that the strictest safety standards were maintained in the manufacturing process. In light of their experience, the team of experts expects that the new Gautschi slab mold will have a definite impact on, as well as meet, both the high demands currently placed by the market and those expected in the future.
Gautschi is not alone in offering state-of-the-art molds, as HPI has also developed a revolutionary mold technology in recent years. This technology allows forging bars or casting ingots to be produced with perfectly smooth surfaces and minimally thin edge zones, adding to the obvious advantages of the horizontal continuous casting systems offered by HPI. Uninterrupted casting over a period of several days already ensures incomparably consistent product quality, and the new HPI molds are being optimized for additional applications and alloys at the C-R-C.
Additional services are offered by the C-R-C’s affiliated laboratory, which can provide a detailed evaluation and analysis of the metallurgical properties of a product. In addition to a spectrometer for measuring the chemical composition, the lab also includes a thermal analysis facility to determine the solidification behavior of the alloy and a device to record the hydrogen content in the melt. The equipment available in the lab is rounded out by small crucible and heat treatment furnaces, which are used for a variety of tasks such as the reproduction of small melts (a few kilograms), homogenization tests and aging tests.
The unique features of the C-R-C technology center promote and support creative processes in the field of mechanical engineering. In cooperation with foundry specialists, new geometries and casting systems can be built in the affiliated mold workshop and tested directly in the lines. The knowledge gained flows directly back into the design.
CONTRACT CASTINGS at the C-R-C
Knowledge gathered at the C-R-C finds direct application in production runs for customers. Due to the optimal sizes of the available facilities, cost-effective and high-quality casts of special alloys can be carried out in a wide range of batch sizes, producing either slabs or billets.
The capability of carrying out contract casts was an important factor that contributed significantly to our desire to found the C-R-C technology center. Concentrating many possibilities under one roof, the C-R-C is unique in the field of toll casting. There is an enormous potential for providing customers with high-quality production material on short notice, and orders can even specify whether material is cast horizontally or vertically.
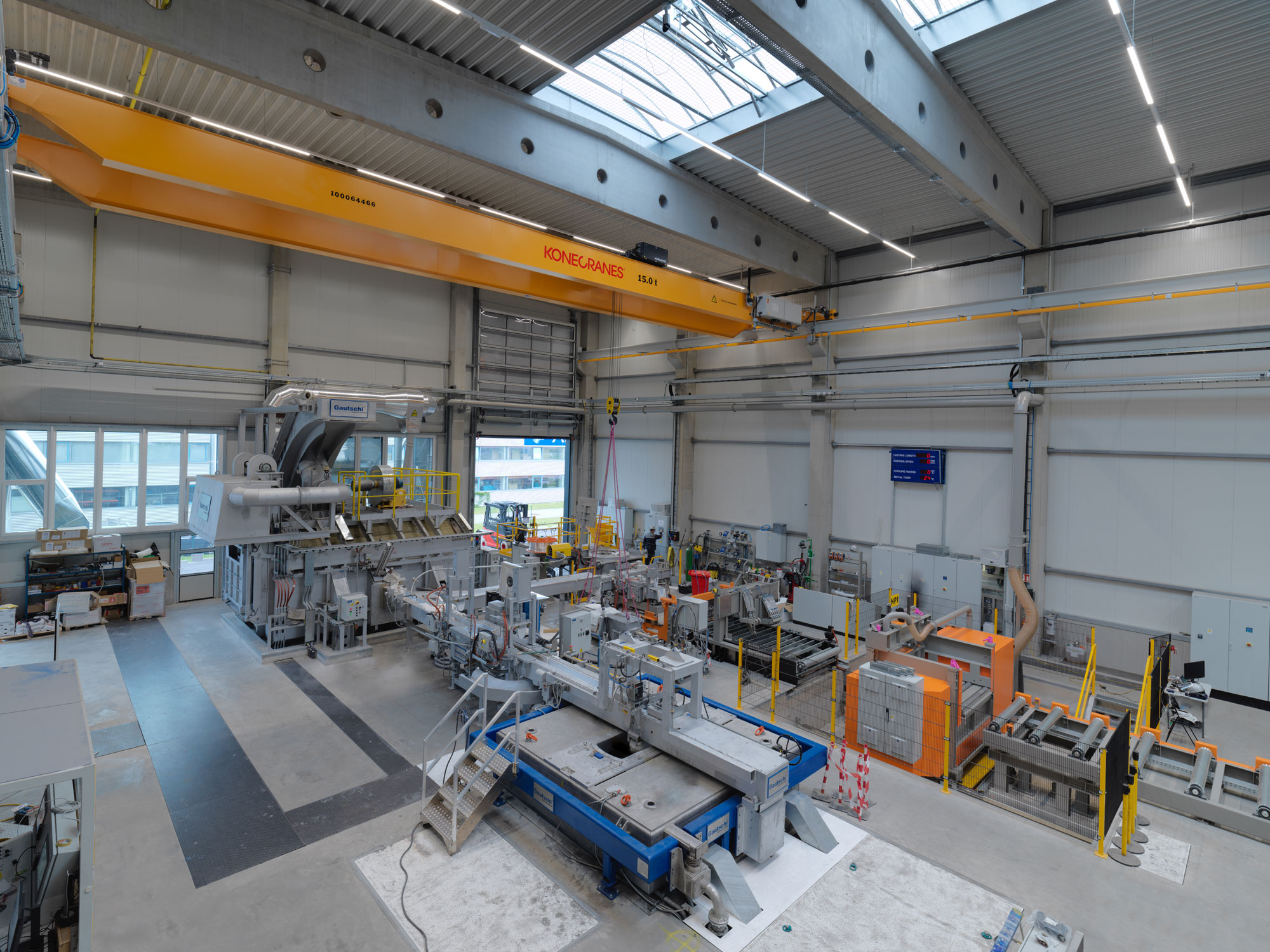