GREENCAL
/ Innovation & Technology, Sustainability
EBNER.blog | Karl Wohlfart & Sascha Eppensteiner, EBNER
GREENCAL
Innovative continuous annealing lines for battery production.
The market for battery technology is expanding rapidly, playing a pivotal role in modern energy supply. Key drivers of this growth include the surging demand for battery electric vehicles (BEVs), portable electronic devices, and stationary energy storage systems for renewable energy. Lithium-ion batteries (LIBs) have emerged as the dominant technology, available in cylindrical, prismatic, or pouch cell formats.
Leading BEV manufacturers favor cylindrical LIB cells due to their high energy density, long lifespan, numerous charge-discharge cycles, stable performance and the ease with which temperature can be managed within the battery pack. Technological advancements and improved production methods are fueling market growth, even as breakthroughs in materials science and optimized high-volume manufacturing processes are both enhancing performance and reducing costs. The proliferation of battery gigafactories currently under construction or in the planning stage underscores this trend.
Asia dominates the cell manufacturing market, but plans exist that will expand Asia’s production capacity to approximately 2700 GWh/y by 2030. Europe and North America are also experiencing significant growth in this sector, with European manufacturers planning to expand their capacity to around 900 GWh/y and North American manufacturers planning to expand to 1550 GWh/y by 2030.
Manufacturing Battery Cell Housings
For the production of cell housings, low-carbon steels with a small amount of alloying elements and a very high degree of purity are used; these steels must also have particular deep-drawing properties.
After hot-rolled steel strip is pickled and cold rolled, it is cleaned and coated. The coating is generally of nickel, applied in an electrolytic process, though depending on the application additional elements may also be used. This coating provides special corrosion resistance.
Coating is followed by heat treatment, which provides the desired material properties. The goal is creation of a fine, isotropic grain structure that is free of oxides and exhibits excellent formability along the length and across the width of the strip; this prevents earing during deep drawing. Diffusion ensures that there is an excellent bond between the nickel coating and the steel substrate.
Depending on the thickness of the strip, the desired mechanical properties, the thickness of the diffusion layer and the final application, the strip may follow a number of process paths during production. The special heat treatment process that is employed can be carried out in a continuous process at a continuous annealing line or, with certain limitations, in one of EBNER’s proven HICON/H2® bell annealer facilities for steel coil.
The strip then moves to a finishing mill for fine adjustment of the properties and the surface finish, after which battery housings are manufactured in a deep drawing process. The housings can then be packed with anodes, cathodes and electrolytes.
The demands the future will bring, in particular those created by e-mobility, are challenging. Every company must design more sustainable processes while simultaneously remaining competitive. With this need in mind, EBNER has developed a new design for a horizontal continuous annealing line: the GREENCAL®. This type of facility focuses on energy efficiency, reducing emissions and maximizing throughput. At the same time, the line is capable of every continuous heat treatment technology employed to produce nickel-coated steel strip including normalizing, diffusion annealing and short-cycle annealing.
The combination of high convection and a highly pure process atmosphere ensures extremely precise temperature distribution across the width of the strip, paired with extremely high throughputs and reproducible material properties. The preferred method of heating is a fully electric system, creating no local carbon or NOx emissions.
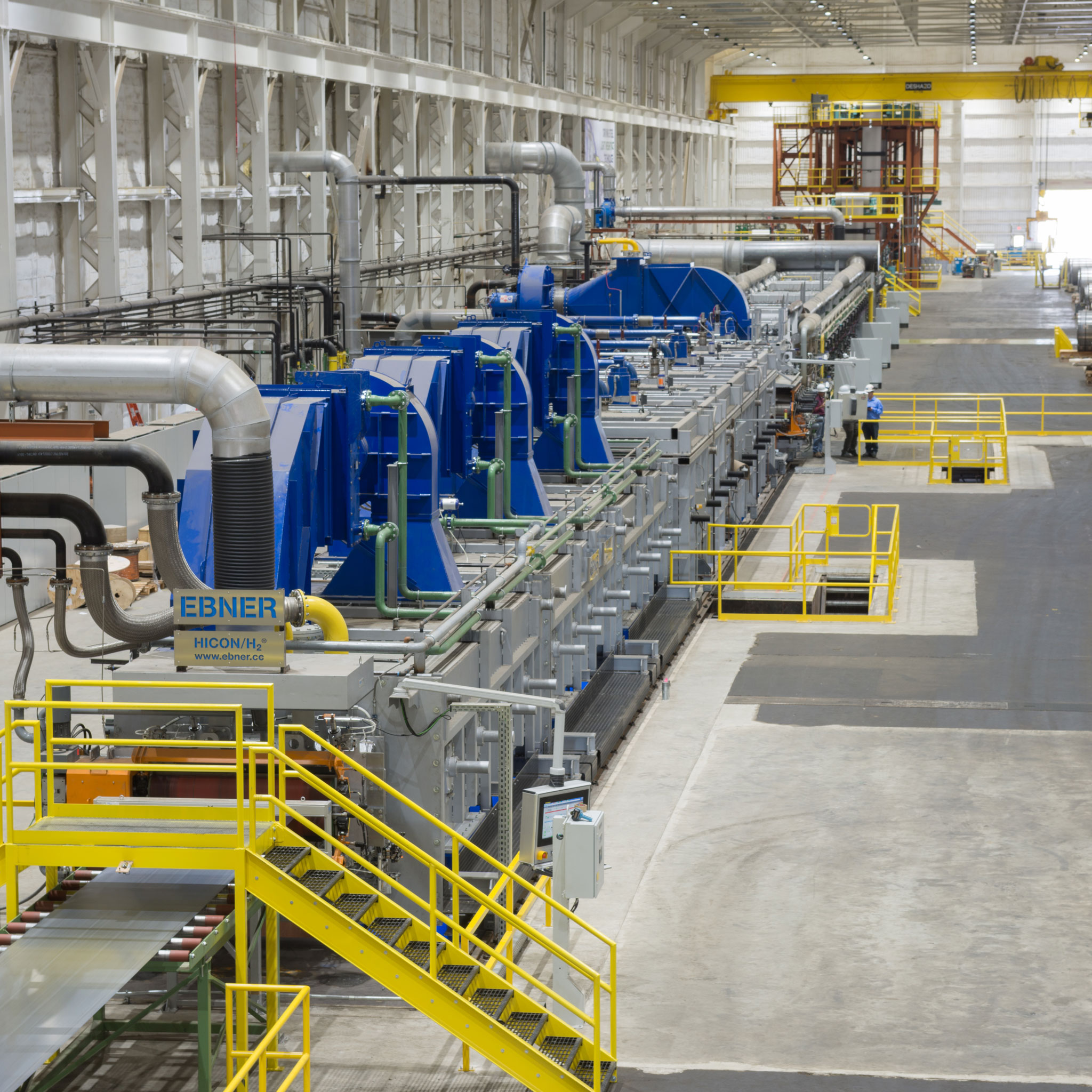
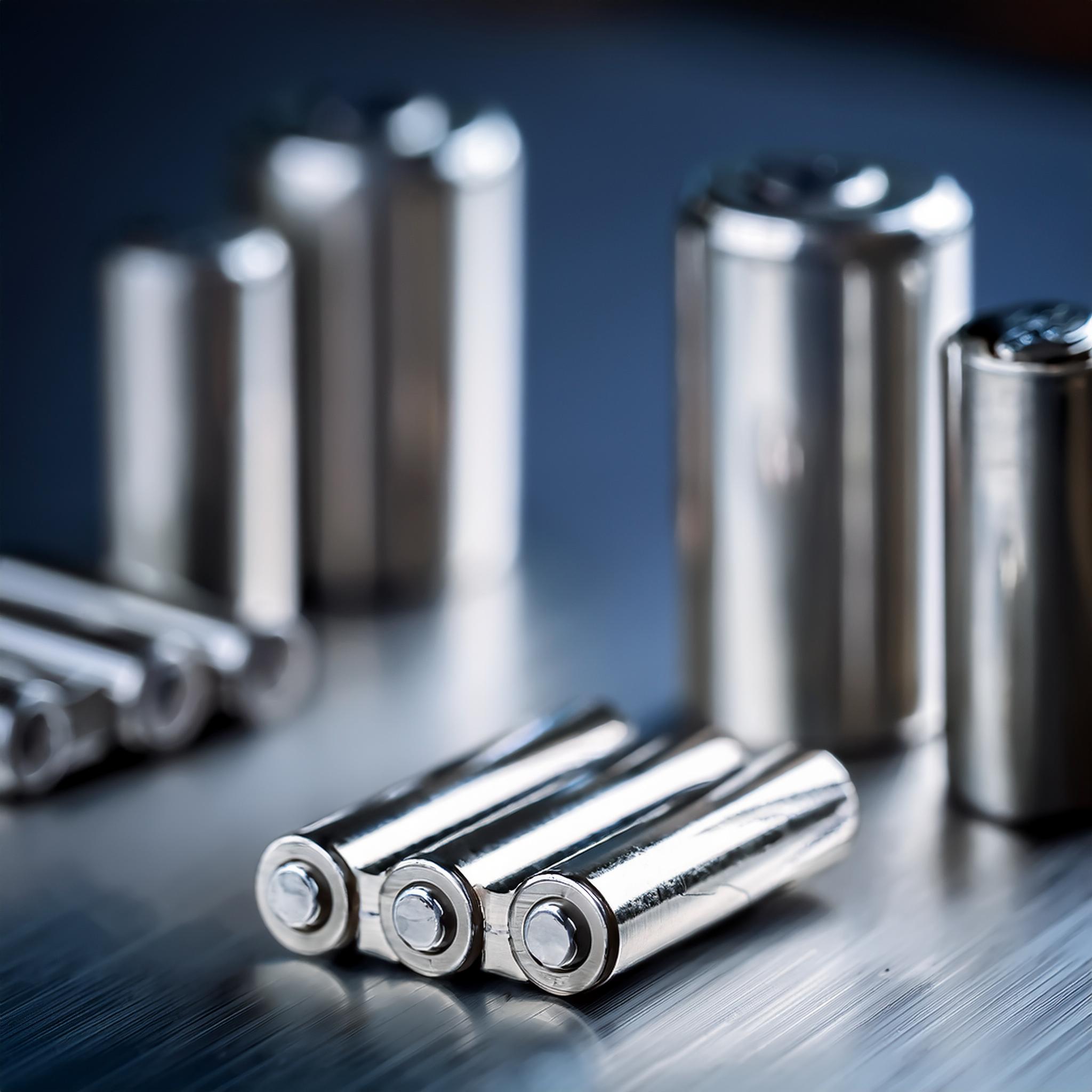
Compared to vertical multi-pass furnaces, a horizontal GREENCAL® is characterized by the following special features:
- High furnace temperatures, which achieve desired microstructures at high outputs (in contrast to the typical maximum temperature of 900 °C in vertical furnaces, temperatures up to 1020 °C are employed)
- Low strip tensions (~ 3 MPa compared to the 6 – 8 MPa of vertical furnaces)
- Low dewpoints due to the gas-tight furnace design (~ -40 °C compared to the ~ -20 to -30 °C in vertical furnaces)
- Thin strip only contacts small furnace rolls in a straight line, with no large contact surface; this reduces the risk of surface damage, roll pickups, heat buckles and strip breaks
- Heat treatment without deflections – multiple 180° deflections at high strip temperatures are eliminated, preventing strip damage due to flow lines and heat buckles
- Heating elements are protected from contact with the strip and damage in the event of a strip break
- Switching between different annealing cycles can be carried out without manual intervention
- High facility availability and low downtimes ensure maximum productivity
Advantages of the GREENCAL® Design
Flexible facility design with high throughput
- Different annealing technologies can be employed in a single line
- A variety of heating system types can be combined in one line
- Modular facility design allows capacity to be expanded at a later date
- Flexible heating and cooling rates, as dictated by the technological requirements
Sustainable heating methods
- Emission-free electric heating system with HICON® high-convection atmosphere circulation for high energy input over a short length of strip in the heating-up section
- Emission-free electric heating with radiant tubes, particularly suitable for soaking zones
- Emission-free induction heating with longitudinal and/or transverse field inductors (depending on the dimensions of the strip and target temperatures, limitations in the temperature uniformity and a higher specific energy consumption must be accounted for)
- Low emission gas-fired combustion system with highly efficient recuperative radiant tubes
The highest efficiency, i.e. the lowest specific energy consumption (kWh/t), is achieved using a high-convection electric heating system.
Flexible strip temperature control
- Extremely precise temperature control and temperature distribution
- Variable heating and cooling gradients
- Flexible soaking times
Gas-tight furnace design
- Special seal designs at the furnace inlet and outlet, as well as at leadthroughs for rollers
- Precise atmosphere control and furnace pressure control systems
- Extremely low dewpoints
Lowest energy and utility consumption
- Extremely efficient heating system design
- Special lightweight fiber module lining
- Process atmosphere recycling with recycling rates up to 80 %
- Thermal energy can be recovered during the process
Damage-free strip transport
- Driven seal rolls at the furnace inlet and outlet seals
- Special furnace roll designs
- Individual rolls powered by precise servo drives
- Prevention of deposits on rolls / long furnace roll service life
User-friendly facility designed for ease of maintenance
- Simple roll removal (without overhead crane)
- Strip break detection with protective devices for components inside the furnace
- New strip can be easily threaded
- Furnace facility can be quickly heated up and cooled when changing processing modes
Bringing it all together
EBNER’s development of a high-performance annealing line for battery steels, with its sharp focus on increasing energy efficiency, reducing emissions and providing high throughputs, is a major step forward in providing sustainable production methods to the metals industry and increasing e-mobility.
The first GREENCAL® facilities have already been successfully put into operation, with additional lines currently under construction.