EBNER Efficiency Upgrades
/ Success Stories, Sustainability
EBNER.blog | Michael Schiesser, EBNER
EBNER Efficiency Upgrades.
In the aluminum industry, sustainability and energy savings start with EBNER case studies.
Recently, as part of a webinar titled “EBNER Efficiency Upgrades for the Aluminum Industry”, held on-line from March 20-21, 2024, EBNER’s Manoj Kumar (Senior Expert Product Development) and Helmut Schumergruber (Senior Expert Automation) – both aluminum experts in EBNER’s Research and Development Department – discussed current strategies and technologies that employ EBNER upgrades to provide significant energy savings. They placed particular emphasis on focused feasibility studies and retrofit solutions, which can be tailored to meet the specific needs and challenges created by individual customer requirements.
The close cooperation between our customers, our Customer Service Department and our Research and Development Department allows the development of solutions that are not only technically efficient, but also economically viable. Engaging in a dialogue with our customers is crucial for understanding their specific needs and developing precisely-tailored solutions.
The importance of energy efficiency in the aluminum industry
The aluminum industry is known for its energy-intensive production processes, which constitute a significant portion of operating costs. At the same time, the industry is under increasing pressure to reduce its environmental impact – pressure that may be exerted by regulatory requirements, rising energy costs or the increased expectations of customers and investors that products are sustainable. Optimizing energy consumption is thus becoming increasingly important.
The webinar: content and goals
“EBNER Efficiency Upgrades for the Aluminum Industry” sought to provide participants with practical insights into retrofit options that provide energy savings. Various examples of aluminum heat treatment facilities were presented, including pusher furnaces, floater (air cushion) furnaces, batch-type furnaces and roller-hearth furnaces. The key message was that significant savings can be realized through targeted, customer-specific solutions.
From theory to successful practice
- Customer-specific energy studies
One of the central topics raised by the case studies was that of focused energy studies, which are tailored to the individual requirements and situations of our customers. Our experts repeatedly emphasized that heat treatment facilities employed by the aluminum industry present different challenges and opportunities, which is why generalized solutions are often inadequate. A thorough analysis of existing systems and processes is the first step in identifying specific areas in which potential savings can be found. - Technological innovations
A variety of technologies that enable energy efficiency to be optimized were presented within the framework of the feasibility studies. Among other solutions, they included advanced carbon-neutral heating systems, waste heat recovery and optimized, energy-efficient cooling processes. Implementing such technologies can significantly reduce energy consumption without impacting production capacity. - Process optimization
Alongside technological solutions, the optimization of existing processes can play a central role in improving efficiency. Significant savings can be achieved by fine-tuning production parameters and introducing energy-efficient practices. Examples include optimizing the process chain to minimize energy losses and using digital tools to monitor and control energy consumption in real time. - Real-life success stories
Another important component of the webinar was the presentation of case studies illustrating the successful implementation of energy-saving measures in the aluminum industry. These examples demonstrated the ways in which EBNER customers achieved significant savings using customized approaches. For instance, one case study showed how an EBNER customer reduced energy consumption by 18 % by installing a mathematical calculation program and optimizing their production processes.
The path into a sustainable future
New technological developments and our approaches to optimizing processes highlight the fact that the aluminum industry is on the right path for improving its energy efficiency and sustainability. The approaches that were presented demonstrated that significant savings can be achieved, for example by conducting customized studies and employing innovative technologies. These do not only contribute to reducing operating costs, but also significantly reduce the environmental impacts created by our customers. Over the long term, aluminum producers that proactively focus on energy savings and sustainability will be more competitive and better prepared to meet future market demands and future regulatory requirements.
In conclusion, it can be seen that feasibility studies are an effective tool that the aluminum industry can use to modernize heat treatment facilities and sustainably reduce energy consumption. The results of our case studies demonstrate that energy savings of up to 20 % are both realistic and achievable. Companies that draw upon this potential will not only be able to reduce operating costs, but will also make a valuable contribution to decarbonizing the aluminum industry.
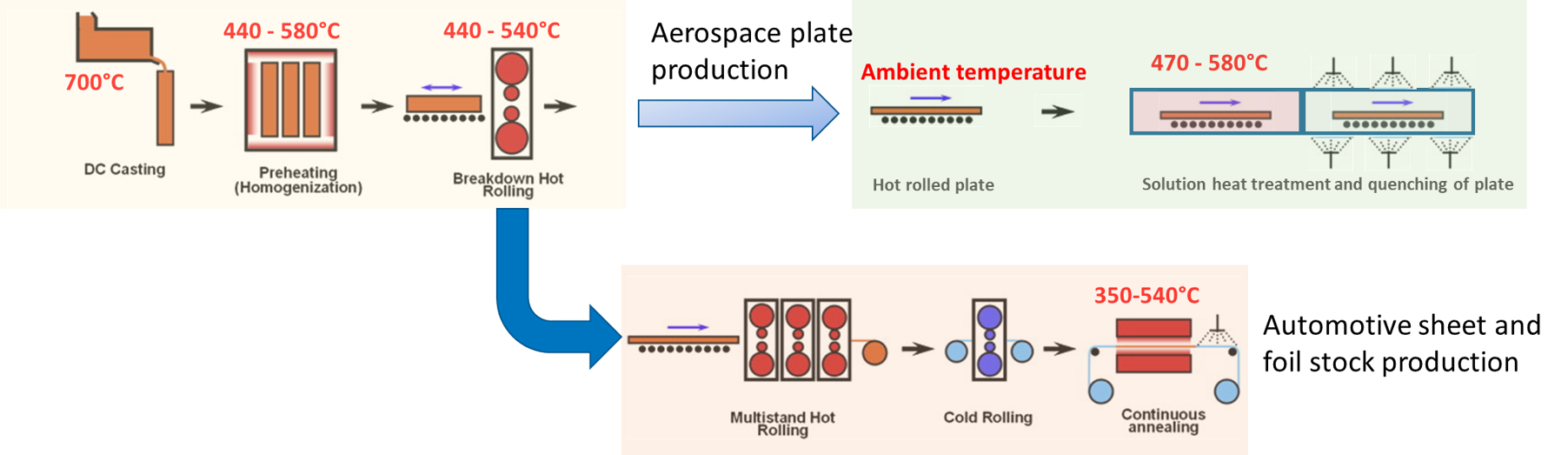