Get the Lead Out.
EBNER.blog | Herbert Gabriel, EBNER
Get the Lead out.
Blue Blade Steel´s quantum leap.
“Get the lead out!” – This idiom is believed to have originated during World War II and was used to signal soldiers to drop their equipment and ammunition, enabling them to be able to move quicker in certain situations.
In modern times, “get the lead out” has taken on a broader meaning beyond its military origins. It now refers more generally to any situation in which there is a need to act quickly or decisively. This is exactly what Blue Blade did when it was faced with making decisions to improve its market position.
The traditional method of hardening high carbon steel strip in continuous lines is to quench it from austenitizing temperature in a bath containing a liquid mix of lead and bismuth. The two metals form a eutectic system with a melting point below that of either pure metal and, more importantly, below the martensitic start temperature. Due to high rate of heat transfer in the molten-metal bath, achieving fully martensitic structures is relatively easy. There is, however, a strong desire to literally get the lead out of the process.
Once Blue Blade recognized the limitations of its existing technology in terms of throughput, flatness and surface quality, it began to search for a new approach. After extensive research Blue Blade found a technology that had proven itself in critical applications throughout the world and that it could introduce to the US market – a technology that would make it the first and only option for American-made H&T strip steel. The heart of this new technology, known as EBNER H2Q, is the use of hydrogen gas jets as a quench media instead of the traditional molten metal.
In 2020, a major upgrade to Blue Blade’s existing EBNER hardening and tempering line with H2Q technology was implemented. This upgrade enabled lead-free quenching at a high throughput and with superior surface quality, while still meeting the mechanical property requirements of martensitic steel at gauges up to 2 mm (0.100”). Not a small feat, considering that quenching from austenitizing temperature (around 1800 °F) to below the martensitic start temperature (about 420 °F) must take place within roughly 1 second. EBNER’s H2Q technology also offered the advantage of fast change-over times, as the system has almost no thermal latency in comparison to a molten-metal quench.
The upgrade project was commissioned in 2020, just as COVID was entering our vocabulary. Despite the difficulties this caused when ramping up production, the advantages of hydrogen quickly come into focus. Fast forward a few months, however, and a building fire destroyed most of the heat treatment line – once again, it was time to get the lead out.
EBNER’s team in Ohio sprang into action to rebuild the line to a like-new condition. Blue Blade was able to resume production in record time, all made possible by hard work and the close cooperation between Blue Blade and EBNER.
During this second rebuild, the existing leveling and tempering sections were replaced with current EBNER technology – elevating Blue Blade’s line to the most advanced heavy gauge hardening and tempering line in the Americas. What gains made it worthwhile to get the lead out? Blue Blade Steel has been able to enter new markets including those for automotive, aerospace, and medical applications.
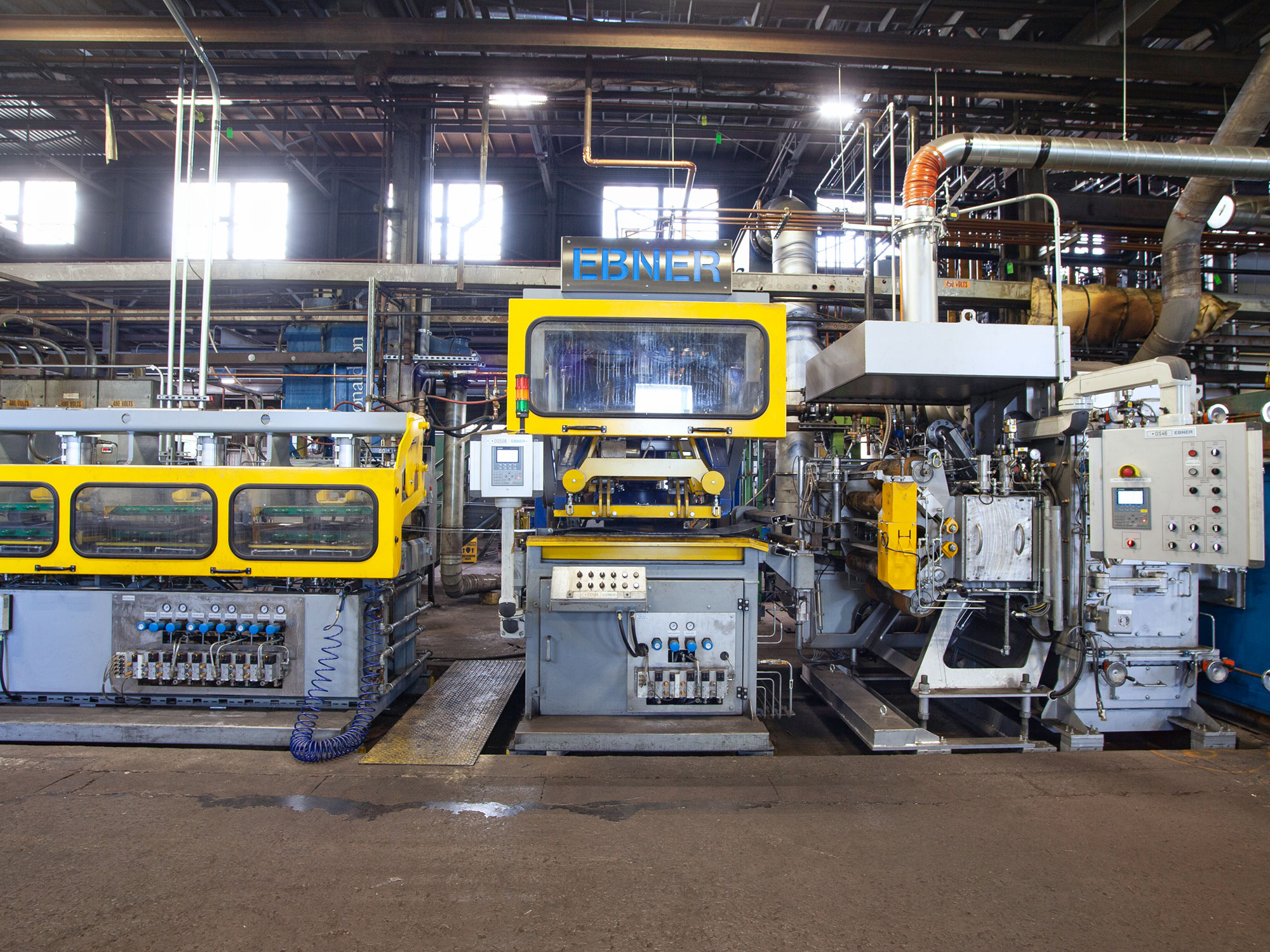