Flexible and innovative
EBNER.blog | Günter Mascher, EBNER Austria
Flexible and innovative.
Pre-aging furnaces for installation downstream of floater furnace facilities for aluminum strip.
The manufacture of automotive sheet out of hardenable 6xxx series aluminum requires a particularly complex sequence of heat treatments. To fulfi ll this requirement, EBNER has developed a special type of furnace.
It has been shown that employing an additional heat treatment step (EBNER pre-heater) immediately after quenching from solution annealing temperature (EBNER floater furnace) can lead to the formation of significantly larger and more stable zones, or nuclei, in the microstructure. The condition that is achieved is designated T4*.
This provides an optimal start to the hardening process, and can be quickly ended during reheating in a later process step.
In practice, this approach is employed in automotive applications where formed sheet parts undergo cathodic dip coating, followed by curing. As relatively short times and low temperatures are used during curing, the material quickly hardens to the desired fi nal hardness (T6). This effect is also referred to as the paint bake response. This eliminates the need for a separate and additional heat treatment step, as would otherwise be necessary.
As EBNER has been successfully manufacturing floater furnaces for solution annealing for decades, the need for improved temperature uniformity at the pre-heater when strip speeds were changed was recognized.
As the pre-aging furnace is linked “in line” with the strip handling gear of the fl oater furnace facility, different strip speeds necessarily result. Matching the pre-heat furnace to the mechanical equipment of the strip handling system is unavoidable.
The pre-heat furnace design that had been previously bought-in rapidly reached its technical limits, so EBNER – as the most innovative and competitive full solution provider in thermal processing – revised and improved the furnace and added it to its product range.
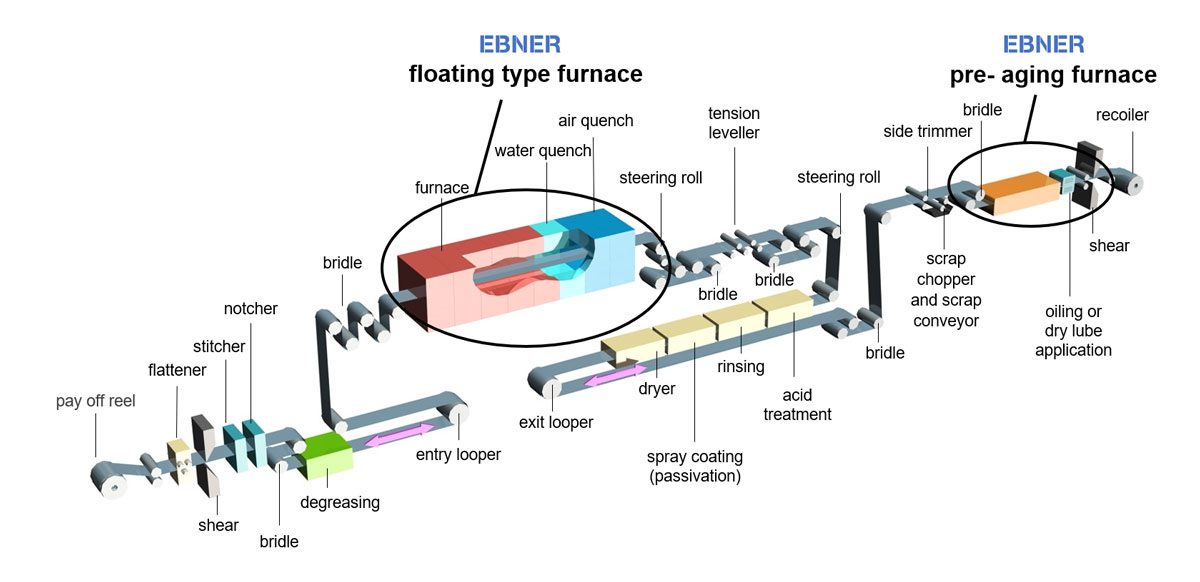
Schematic representation of a floater furnace facility
Simulations, practical tests in our in-house R&D department, the application of the accumulated knowhow gathered from our fl oater furnaces and calculation modules resulted in a furnace optimized to meet the requirements. Just as at a floater facility, the strip is transported contact-free through the furnace by the proven EBNER nozzle box system.
To provide precise and consistent material properties, it is necessary for the pre-aging furnace to be able to react quickly to changing facility parameters. The ability of an EBNER pre-aging furnace to react quickly and flexibly minimizes scrap length when changes are made in the line speed.
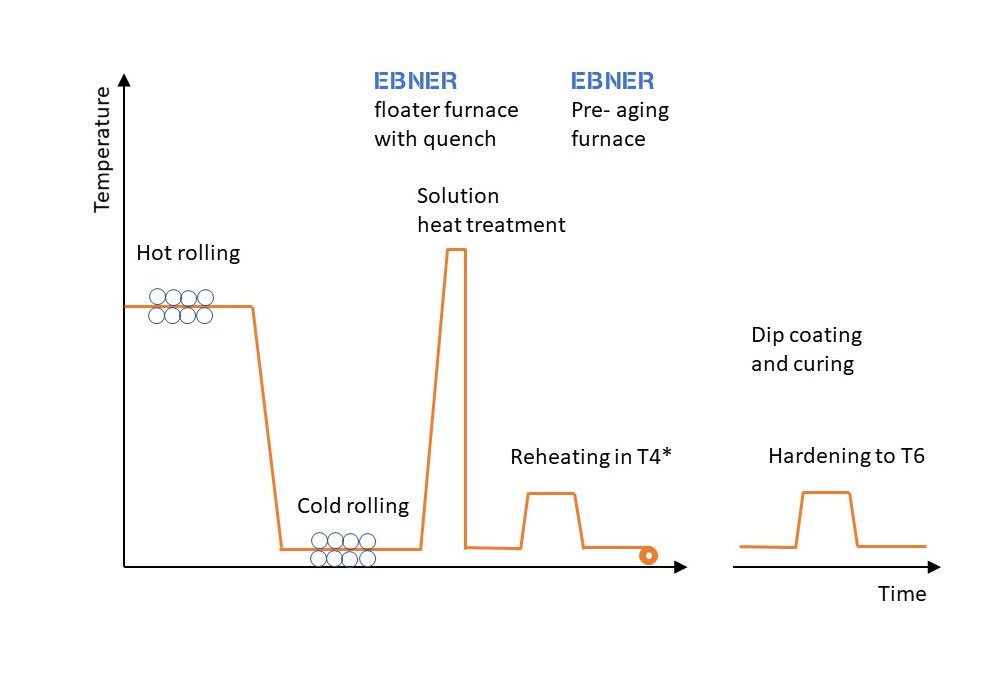
Schematic representation of process steps
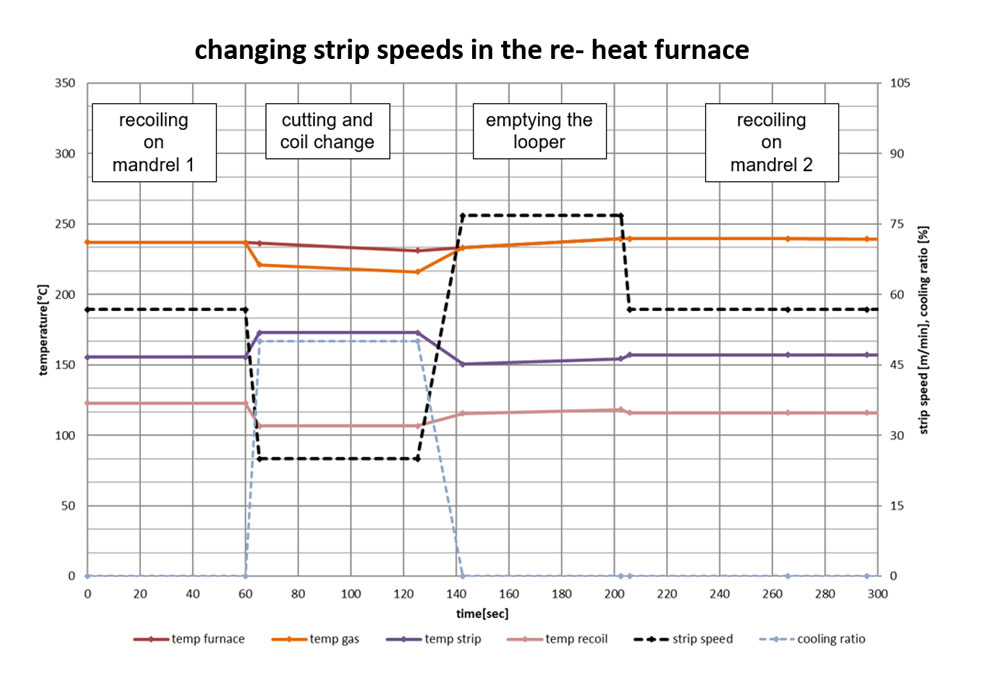
The chart shows the relationship between temperatures during changing line speeds
Due to its powerful heating system and cooler, an EBNER pre-aging furnace is ideally suited for rapid reactions to process changes. Our VISUALFURNACES process control system, acting in concert with the facility control system, calculates both the strip temperature required at the outlet of the pre-aging furnace and the required process parameters (such as recirculation, heating, and cooling performance of the furnace) for different strip speeds (e.g. catching-up, processing, cutting, etc.). Optical strip temperature measuring devices monitor the calculated setpoints and correct them as needed. Five such EBNER furnaces are already in operation, and orders have been placed for two more. These direct gas-fired furnaces are modular in design, divided into zones along their length. They may thus be easily expanded to suit any desired maximum facility throughput. Two widths of furnace are available for installation in existing facilities.
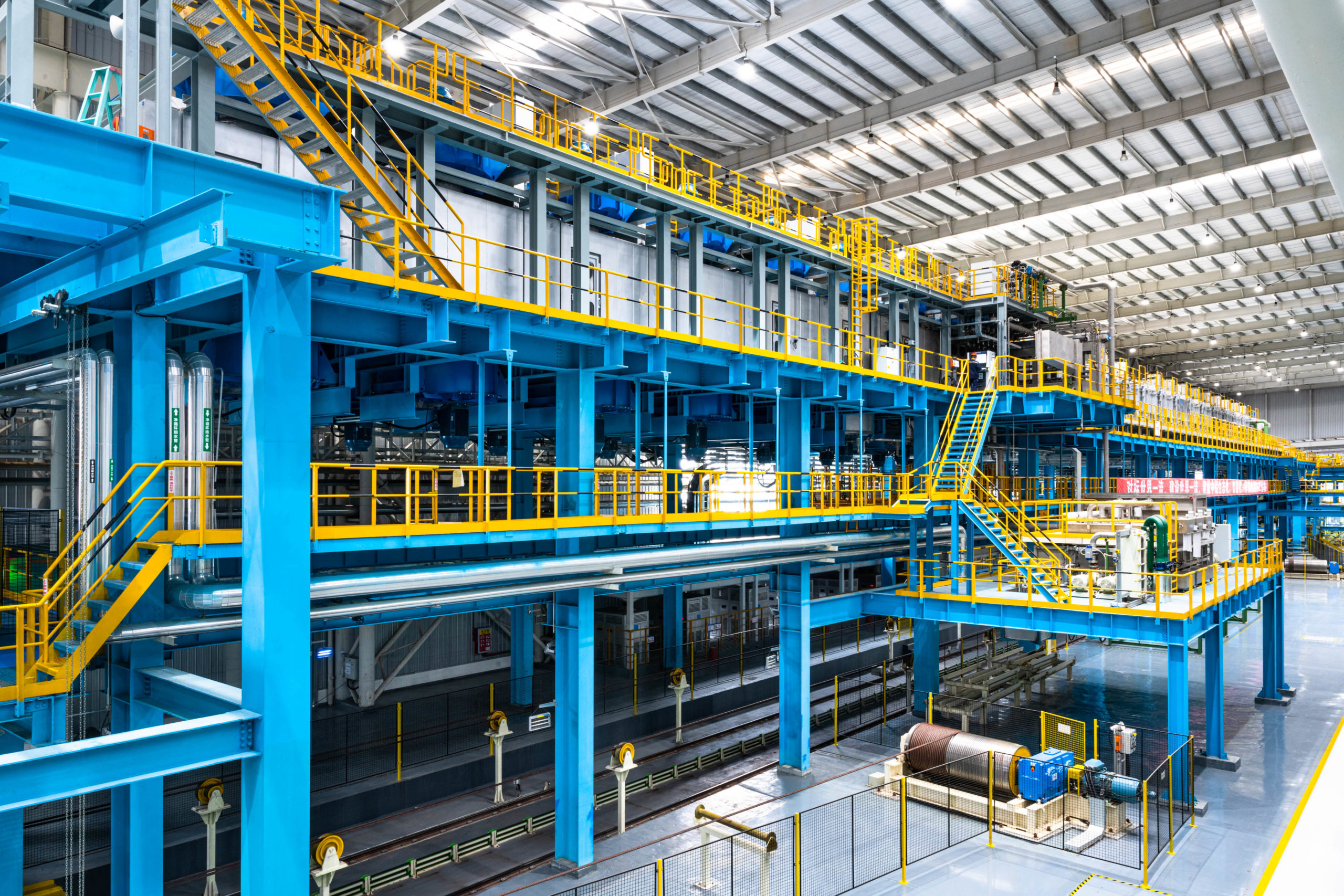
EBNER floater furnace facility in China
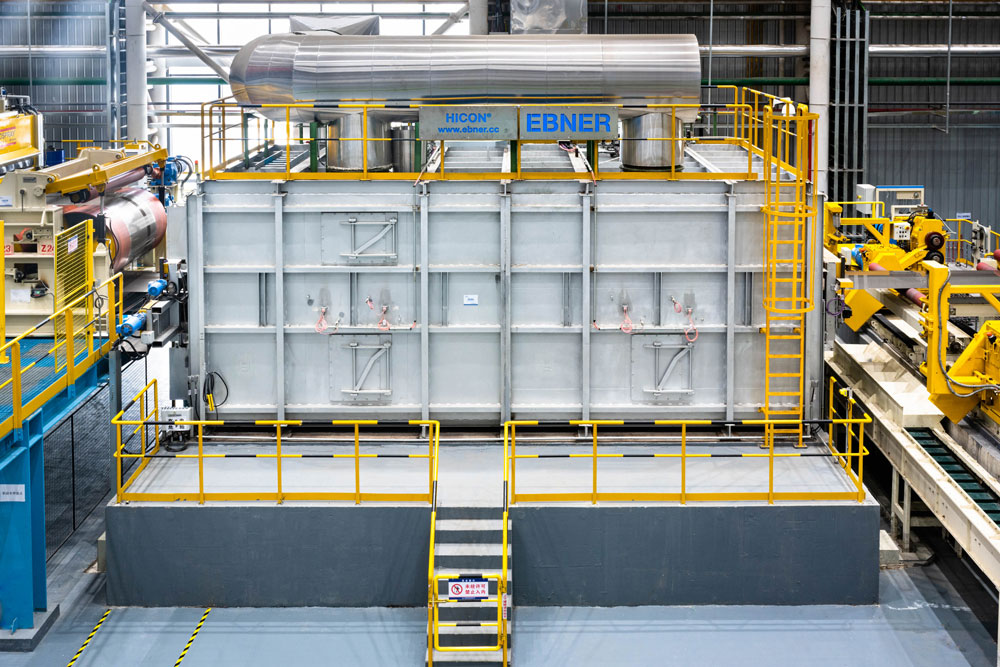
EBNER pre-heater at a floater furnace facility in China