Digital transformation.
/ Digitalization, Innovation & Technology
EBNER.blog | Peter Gosch, EBNER, Austria
Digital transformation.
At EBNER, digitalization is more than just a buzzword.
At EBNER, the digitalization of business processes already began several years ago. This has allowed us to supply even more efficient and powerful facilities to our customers.
EBNER is aware of both its ecological and economic responsibilities, and has set itself a clear goal: to ensure that EBNER heat treatment facilities have the lowest possible environmental impact and consume the lowest possible amount of resources during operation.
All of our digitalization efforts are aimed at helping us meet our strategic goal of ecological and economic responsibility. Digital transformation is playing an important role in this effort, and will have a significant impact on the future of the company.
Our new digital backbone will be formed by the new VISUALFURNACES 8 process control system (PCS), which is currently under development. All digital services will be supplied with process data by VISUALFURNACES 8, which when combined with mathematical and physical models (Model Predictive Control and Properties Predictive Control) will enable us to ensure optimal production management and increased yields in the future.
Our effort to optimize production management not only ensures the success of the EBNER effort to optimize TCO (Total Cost of Ownership), but also has a significant effect on optimizing the utilization of required resources. This reduces both energy consumption and emissions.
One of the digital services that will be offered by EBNER in the future will be the use of a digital twin during commissioning. This will allow commissioning times to be optimized, and process sequences can be simulated. In the future, digital twins will also be used to train the operating personnel of our customers. They will make it possible to carry out realistic training before actual commissioning.
In the field of customer services, our goal is to provide all of our customers in the next few years with a predictive maintenance portfolio and an SLA (Service Level Agreement) tailored to it over the next few years.
In the near future, communication will take place through our new EBNER customer portal: our customers will be able to access all facility information, relevant process data, service tickets, training opportunities, information about new developments and current sales campaigns centrally, through the EBNER Customer Portal.
Here too, the goal is to allow our customers to access all relevant information as easily as possible, making communication and service workflows as efficient as they can be and saving as many resources as possible.
During our digital transformation, we strive to employ latest technologies. They allow us to optimally employ the expertise and experience of our employees throughout the world: as personal as needed, as digital as possible. This conserves the resources of both our customers and the environment.
We would like to refer our readers to the last issue of the HICON Journal, issue 02/2020. In that issue we introduced our digitalization strategy, our E3 (EBNER Energy Efficiency) modules in particular. We also provided an overview of both EBNER facilities 4.0 and CATCH, the digital “dating” platform for plant engineering.
At EBNER, digitalization and ecology go hand in hand. Digital transformation is not a buzzword for us: it is both a reality we experience in our daily lives and a clear strategic goal.
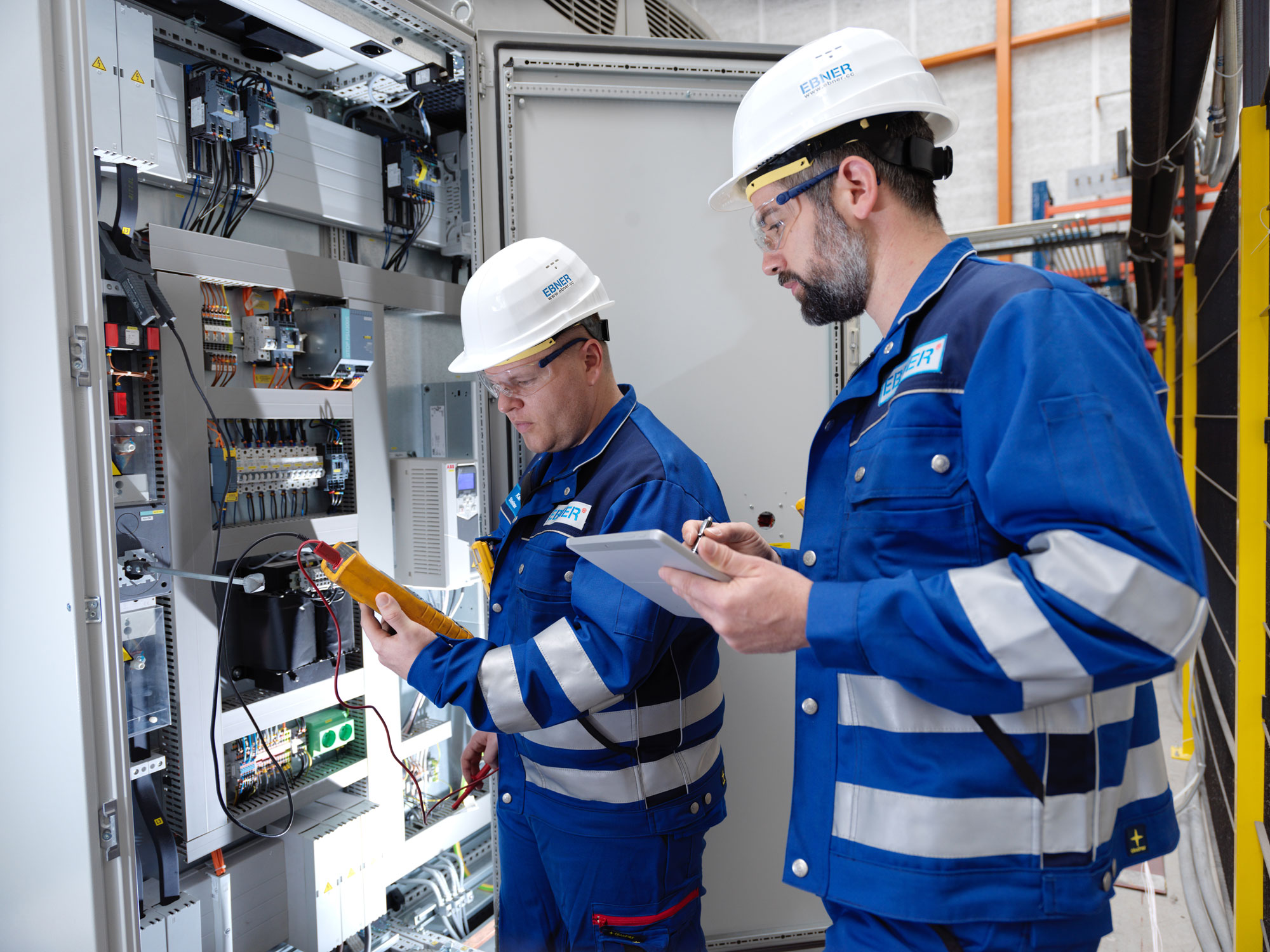