An innovative partnership: New standards for forging stock
/ Innovation & Technology, Success Stories
EBNER.blog | Oliver Jansen, Gautschi | Rainer Edtmeier, HPI
An innovative partnership: New standards for forging stock
Gautschi Engineering GmbH and HPI High Performance Industrietechnik GmbH supply a complete forging stock production line to Bharat Forge Aluminium USA.
Bharat Forge Aluminium USA is a subsidiary of India’s Bharat Forge Limited, a global leader in the metalworking and forging industry. The company specializes in manufacturing high-quality aluminum forgings that are used primarily in the automotive and aerospace industries.
Gautschi and HPI, both members of the EBNER GROUP, have recently collaborated in supplying a state-of-the-art casthouse for Bharat Forge Aluminium USA. This line will produce horizontally-cast aluminum rod, which will serve as the starting material for forged products. Bharat Forge’s primary goal is to automate production to the greatest extent possible, enabling it to offer extremely competitive per-unit prices to the automotive industry. At the same time, the high degree of automation will maximize workplace safety for Bharat Forge’s employees.
FROM SCRAP TO BILLETS TO DIRECT-FORGED PRODUCTS
Production begins with one of the two tiltable Gautschi single-chamber furnaces, which work in tandem as melting/casting furnaces. Charging is carried out by an HPI charging machine, which ensures efficient charging by minimizing the opening time of the furnace door and protecting the furnace lining from damage. Dross is cleaned from the surface of the bath by a rail-mounted HPI skimming machine.
The furnaces are equipped with Gautschi’s innovative VAREGAENVICOM regenerative burners, providing an output of 5200 kW. These burners have a number of advantages including long burner cycles, which provide a high effective melting rate paired with low NOx emissions. No external recirculation is required, which both has an additional positive effect on NOx emissions and means that maintenance requirements are low. Furthermore, the design of the refractory materials in a Gautschi regenerative burner means that the surface temperature of the burner is lower than that found in competitors’ products – minimizing heat losses in the area around a burner.
With a nominal capacity of 35 metric tons of liquid metal and a melting rate of 7 metric tons per hour, the Gautschi furnaces are perfectly matched with the casting equipment supplied by HPI. The installation of a pair of furnaces ensures that production is never interrupted, even if one of the furnaces is emptied. Thanks to the continuous supply of liquid metal to the caster, production runs of up to 36 hours are possible. Depending on the diameter of the product, outputs as high as 5000 kg/h may be achieved when casting 6xxx aluminum alloys.
The casting machine is equipped with the new HPI ForgeMaster© mold technology, providing the smallest possible edge zone (columnar edge) and a homogeneous microstructure. This is particularly important for forging stock, as the optimal conditions for solidification enable the billets to be directly forged – without an additional homogenization step. The excellent surface quality significantly reduces the amount of chips produced during the peeling process, which can reduce material losses by up to half.
All additional processing steps are carried out in a continuous in-line sequence: after casting, the cast rod is ultrasonically tested, peeled, inspected for surface defects, sawn into short lengths, chamfered and automatically packed into boxes. The billets are then transported directly to the adjoining forging plant, where they can be processed into high-quality parts for the automotive industry.
This joint project with Bharat Forge and the close cooperation between Gautschi and HPI will significantly change how forging stock is produced. Through its use of state-of-the-art technology and the highest standards for safety and environmental friendliness, this cooperation has set new standards for the industry. Together, the three companies are shaping the future into one that is efficient, innovative and sustainable.
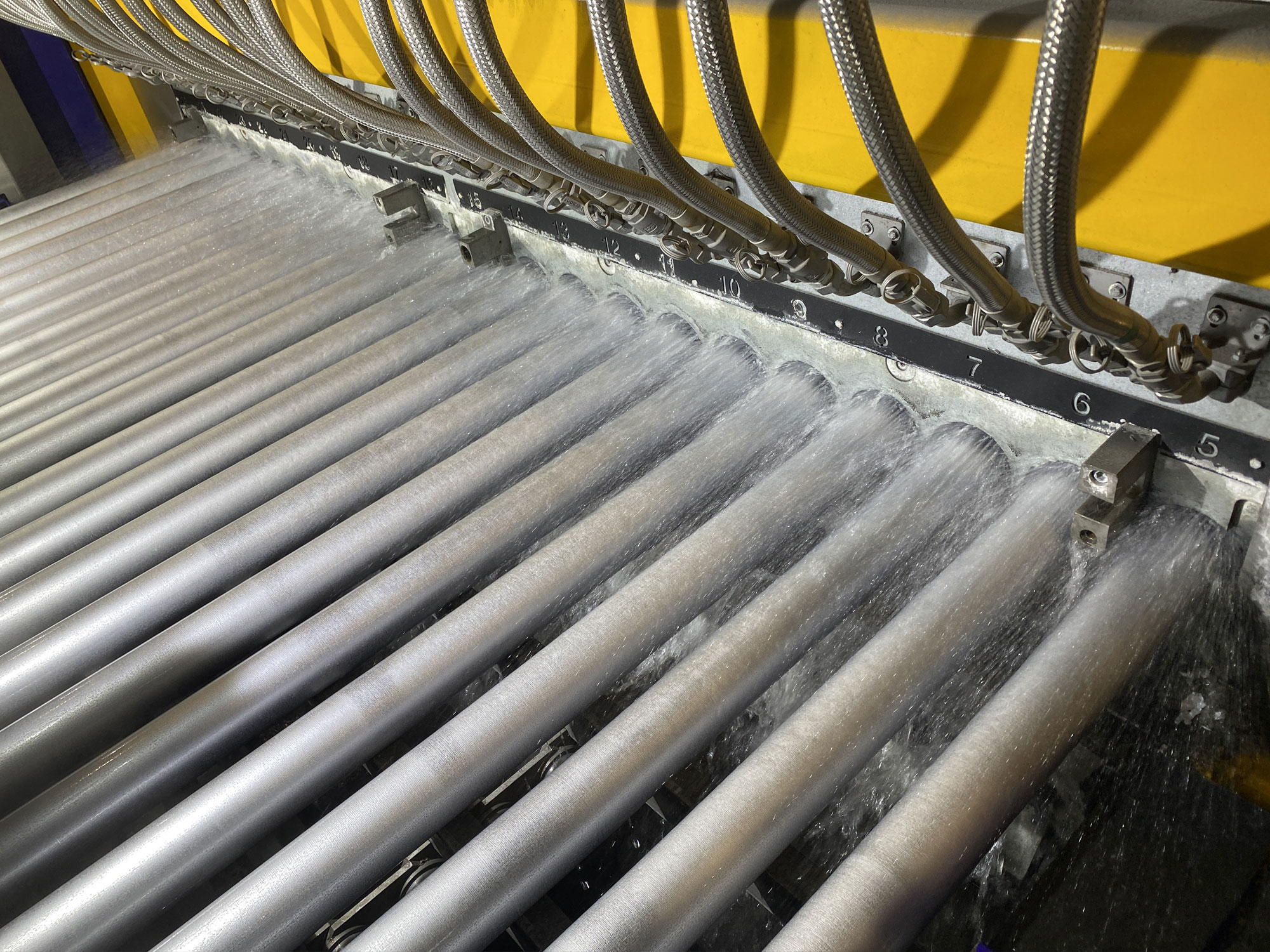
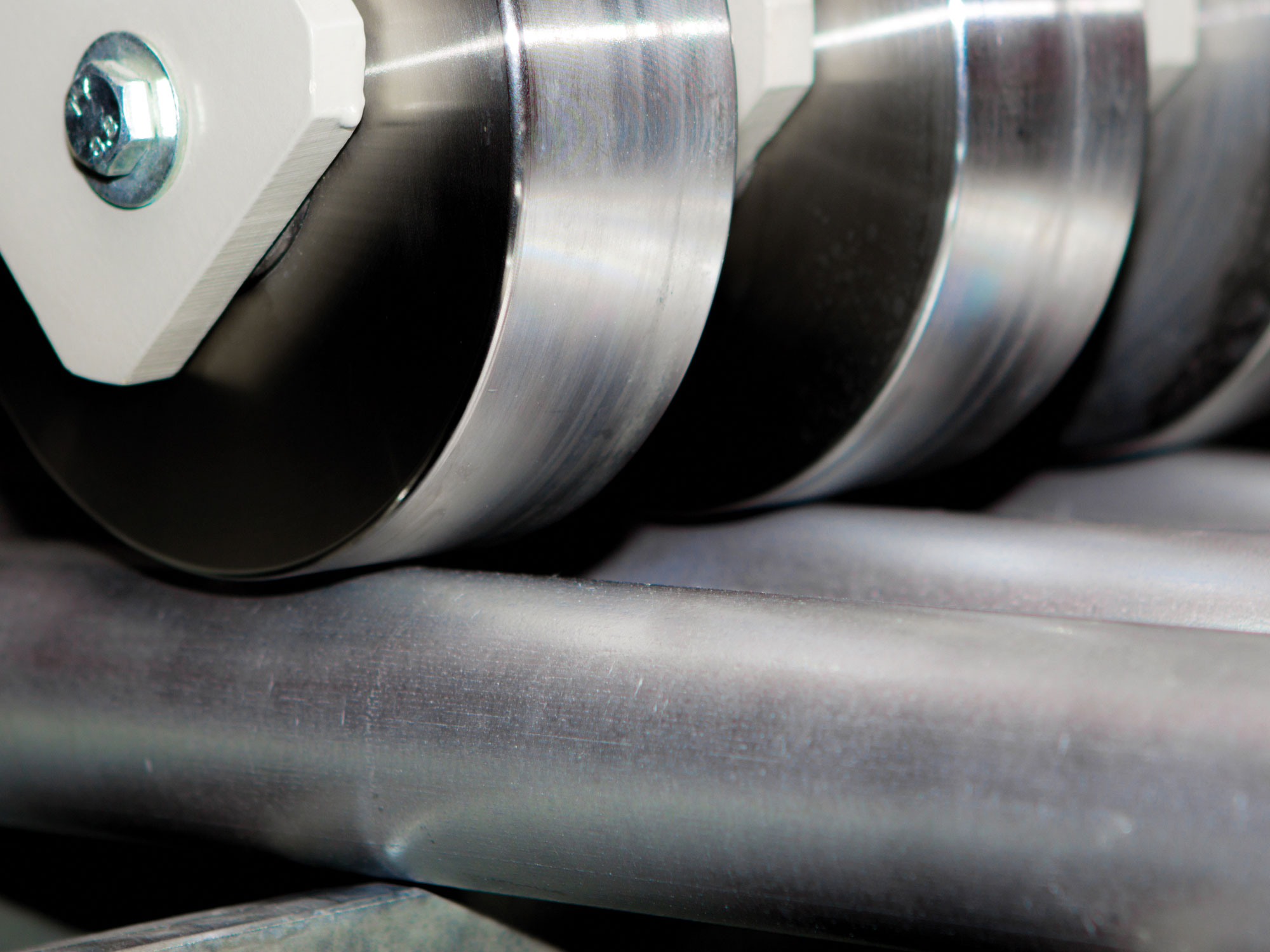