C-R-C – Casthouse Revolution Center
EBNER.blog | Robert Schmidt, Gautschi, Rainer Edtmeier, HPI, Austria
C-R-C Casthouse (R)Evolution Center.
HPI and Gautschi “mold” a new future for casting technology in Ranshofen, Austria
For almost 100 years, Gautschi Engineering GmbH has been a driving force in raising casthouse equipment technologies to new levels. HPI – High Performance Industrietechnik GmbH specializes in the horizontal continuous casting of light metals, and in recent years the company has demonstrated its pioneering role through continuous development.
With the establishment of a state-of-the-art technology center in Ranshofen, Austria, the two companies have taken another step forward in extending their technological lead.
The Casthouse (R)Evolution Center (C-R-C) in Ranshofen, Austria is a full-scale industrial foundry, offering a horizontal casting facility operated by HPI and a vertical casting facility operated by Gautschi. Both facilities are available from October 2020 for customer demonstrations, alloy trials, operator training, and small, quick and/or special production runs. The facilities will also be used to further develop the state-of-the-art molds and casting systems of both companies, including all related aspects such as safety, quality, metal yield, and productivity.
A variety of equipment is available from HPI, including a 1.5 t electric melting furnace, a rod feeder device for grain refinement and of course the heart of the facility: a horizontal continuous casting machine (HSG) with flying saw. The entire production process, from melting the base material to production of first-class semi-finished aluminum products in both round and rectangular formats, is offered.
In addition to all this, the technology center is equipped with a 7.5 t melting furnace from Gautschi. When required, this furnace can supply the HPI casting line with liquid metal for an extended period of time. The Gautschi vertical casting machine is capable of casting slabs and billets in any alloy and up to 6.5 m in length. Material is fed in from the Gautschi melting furnace mentioned above. An inline degasser and a ceramic filter guarantee top quality.
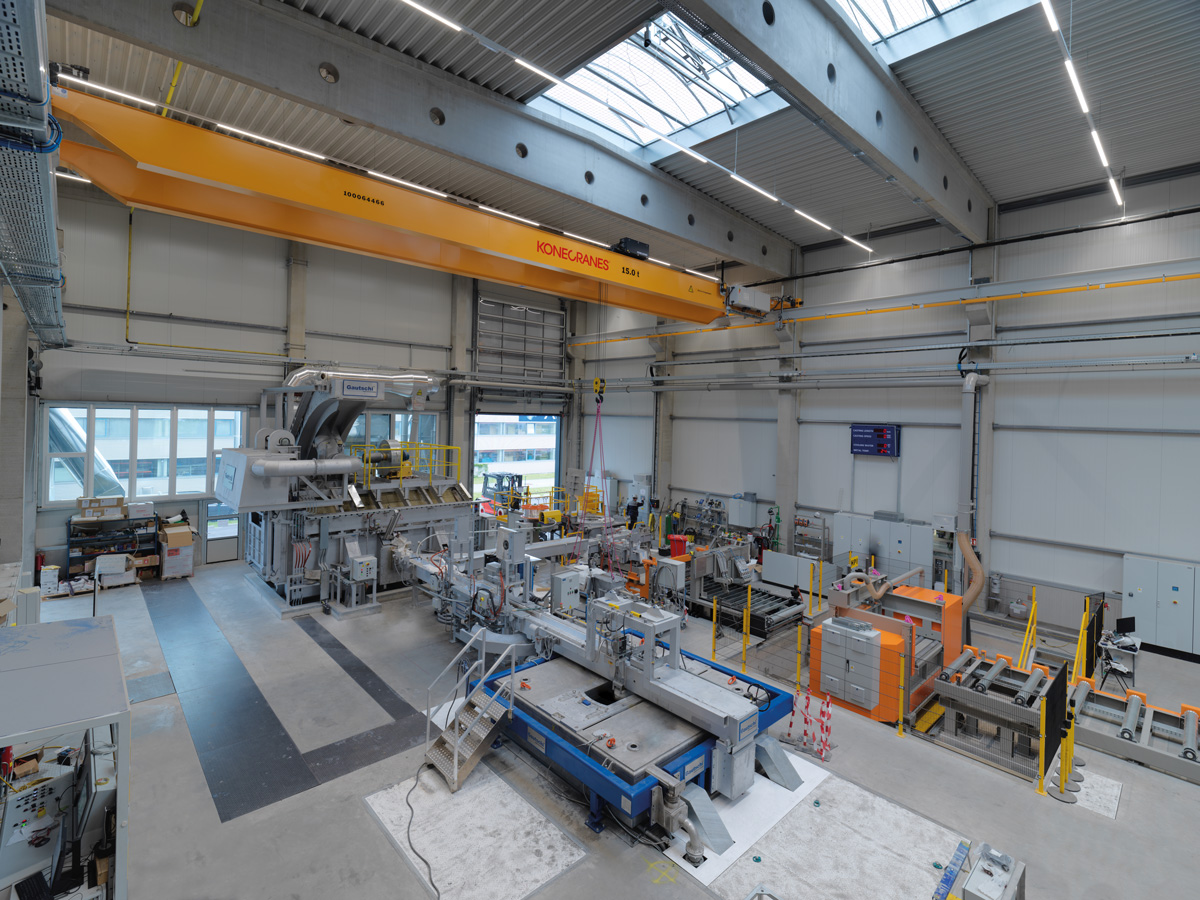
Gautschi has been a supplier of casting machines for both billets and slabs for many years, and offers several types of molds on the market. These include the well- known Gautschi billet mold, which has demonstrated its advanced quality and performance at many locations over the last 20 years, and the recently-developed and newly-introduced Gautschi slab mold. The new Gautschi slab mold was developed by an international team comprised of casting experts and experienced Gautschi design engineers. Making use of their extensive experience in casting difficult and highly-demanding alloys, including slabs used in aircraft and automotive body applications, the experts focused on providing real 100 % hands-free casting, significantly less scalping scrap and significantly less butt curl for all alloys, even as they ensured that the strictest safety standards were maintained in the manufacturing process. In light of their experience, the team of experts expects that the new Gautschi slab mold will have a definite impact on, as well as meet, the highest demands currently placed by the market – as well as those expected in the future.
The Gautschi billet mold is based on the Air Glide technology developed by VAW. An excellent surface, a low segregation zone, high pit recovery and easy maintenance have made this mold a huge success. The full range of alloys has been cast successfully with Gautschi billet molds, including the most demanding aircraft alloys. This billet mold has been improved over the last few years, and will be further improved at the CRC by making use of the pilot caster.
The complete process is connected to a data logging and analysis system, enabling continuous data recording and process evaluation throughout the entire plant. By recording and analyzing the properties of the semi-finished product, such as the microstructure, surface quality, tensile strength and hardness, parameter effects can be derived and precise prediction models generated. These models allow a direct derivation of the effects of process conditions on the quality and properties of the end product. The prerequisites for qualitative and quantitative optimization of the customer’s production are thus given. The affiliated laboratory enables detailed evaluation and analysis of the metallurgical properties of a product. In addition to a spectrometer for measuring the chemical composition, the lab also includes a thermal analysis facility to determine the solidification behavior of the alloy and a device to record the hydrogen content in the melt. Small crucible and heat treatment furnaces round out the available equipment in order to, for example, reproduce small melts (a few kilograms), homogenization tests and aging tests.
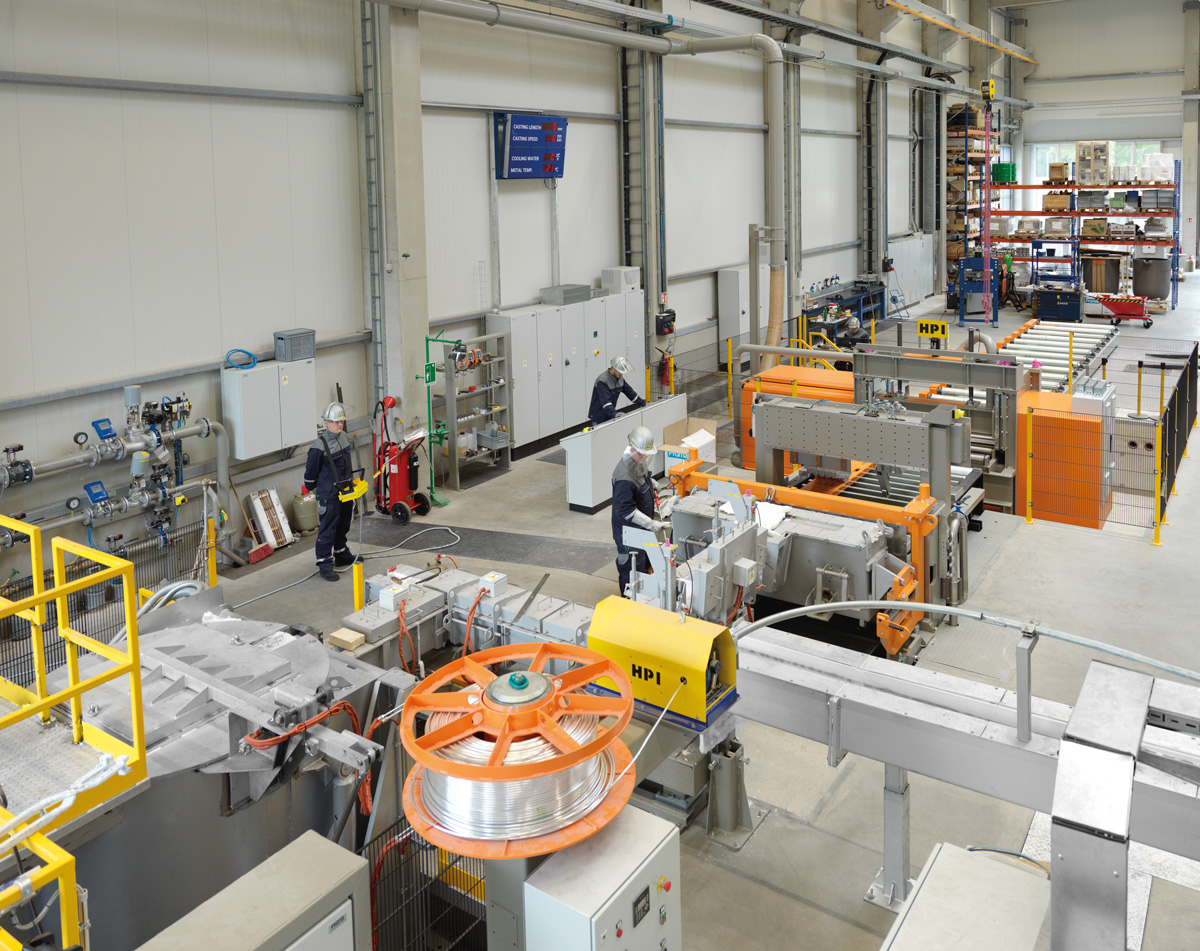
The unique features of the technology center promote and support creative processes in the field of mechanical engineering. In cooperation with foundry specialists, new geometries and casting systems can be built in the affiliated mold workshop and tested directly at the lines. The knowledge gained flows directly back into the design.
Thanks to the new technology center, customers are always at the cutting edge of technology – benefiting from the bundled know-how in Ranshofen, the center of the aluminum industry in Austria.