PACC module
EBNER.blog | Gerhard Schöfl, EBNER, Austria
The PACC module from EBNER.
EBNER develops flexible and robust in-line technology to partially harden and temper (tailored temper) press-hardened components: the EBNER PACC module (Precisely Accurate Contact Cool).
The following announcement was made to the automotive industry in 2017: “Lightweighting does not bring significant advantages to electric vehicles; the weight of the vehicle is virtually insignificant.” – Prof. Dr. Ferdinand Dudenhöffer, CAR Center Automotive Research, University of Duisburg-Essen.
Today, we see a trend in exactly the opposite direction: there has been a massive increase in the amount of light- weighting in modern car bodies, utilizing flexible hard/ soft zones in structural components.
If the generation of electricity is left out of the equation, electric motors are extremely efficient (efficiencies above 80 %). New developments also allow the recuperation of braking energy. This is what led to the thought that vehicle weights would only play a secondary role, as the energy required for acceleration would not be lost – at least in theory. Today, however, we have recognized that energy is actually lost twice: once during acceleration, and once during braking. This lowers the overall efficiency to around 60 %. An additional factor contributing to the rise of lightweighting is that components for electric vehicles,
such as axles and batteries, are expensive. The lighter the vehicle, the smaller the motor can bereducing cost. Furthermore, it should also be remembered that vehicle weights are restricted by European regulations for class B (standard passenger vehicle) driver’s licenses.
All this means that lightweighting is still important.
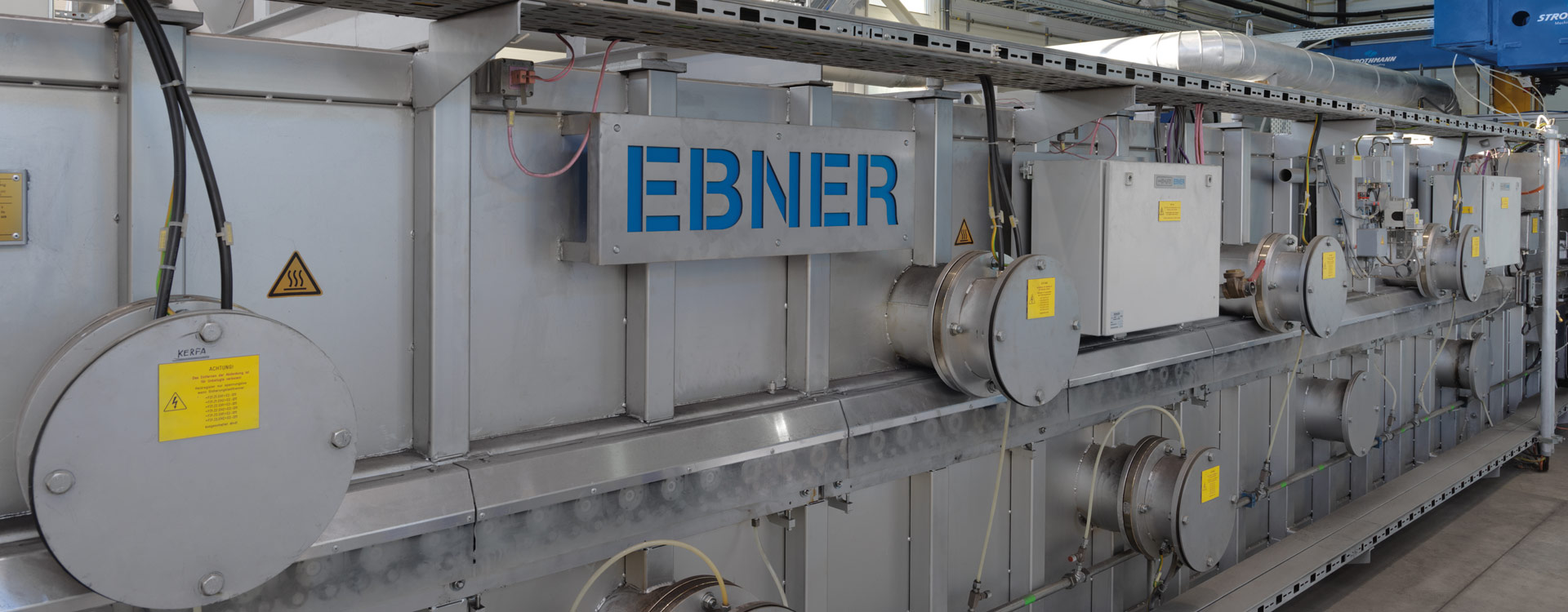
How do you lightweight steels?
The answer is press hardening. During press hardening, manganese-boron steel “blanks” – plates that have already been cut to size – are heated up to austenitizing temperature. They are then held at austenitizing temperature for about one minute to dissolve the carbides. The blanks are then transferred to a press equipped with a water-cooled die, and formed into a component.
The component is quenched to 170 °C at the same time, meaning that martensitic hardening also takes place. The result is a component with the highest possible strength, allowing the amount of required material to be reduced and with it the weight.
What do the new in-line PACC modules offer?
For some time, EBNER has been investigating new in-line technologies to partially harden and temper the hard/soft zones in structural components. This process is also known as tailored tempering. The high component strength and low component weight provided by this process, as well as the precisely-tuned deformation of the component in a crash, are major reasons why tailored tempering is desirable.
Very hard components are also difficult to weld – it is therefore important that components be fabricated with soft zones, easing assembly and installation. Currently, press hardening is generally carried out with hot forming equipment in a press. Disadvantages of the approach include the high costs of the press, the rapid wear of hot sections, component distortion and limited flexibility should changes be desired.
The new in-line PACC module for partial hardening and tempering was developed by EBNERs in-house R&D Department. This new technology makes it possible to
easily create flexible soft zones in press-hardened components. It involves partially cooling the blanks directly in the furnace, where as in usual processes the blanks are heated up to austenitizing temperature. Partial cooling of specific areas takes place in the last section of the furnace facility, with cooling pins (Contact Cool) applied to the workpiece to lower the temperature of the soft zones.
The blanks are then formed in the press in the usual way. The dies are (only) cooled, not heated. The geometry of the soft zones can be easily adapted, using a cartridge system. Additional advantages are a simple, robust system, no component distortion and flexible, adaptable transition zones. The service costs for stamping/pressing are also reduced significantly.
In cooperation with MAGNA, a prototype facility equipped with a new in-line PACC module has been installed at the MAGNA works in Weikersdorf, Austria. The line is currently producing components for the automotive industry under production conditions, to the complete satisfaction of all parties.
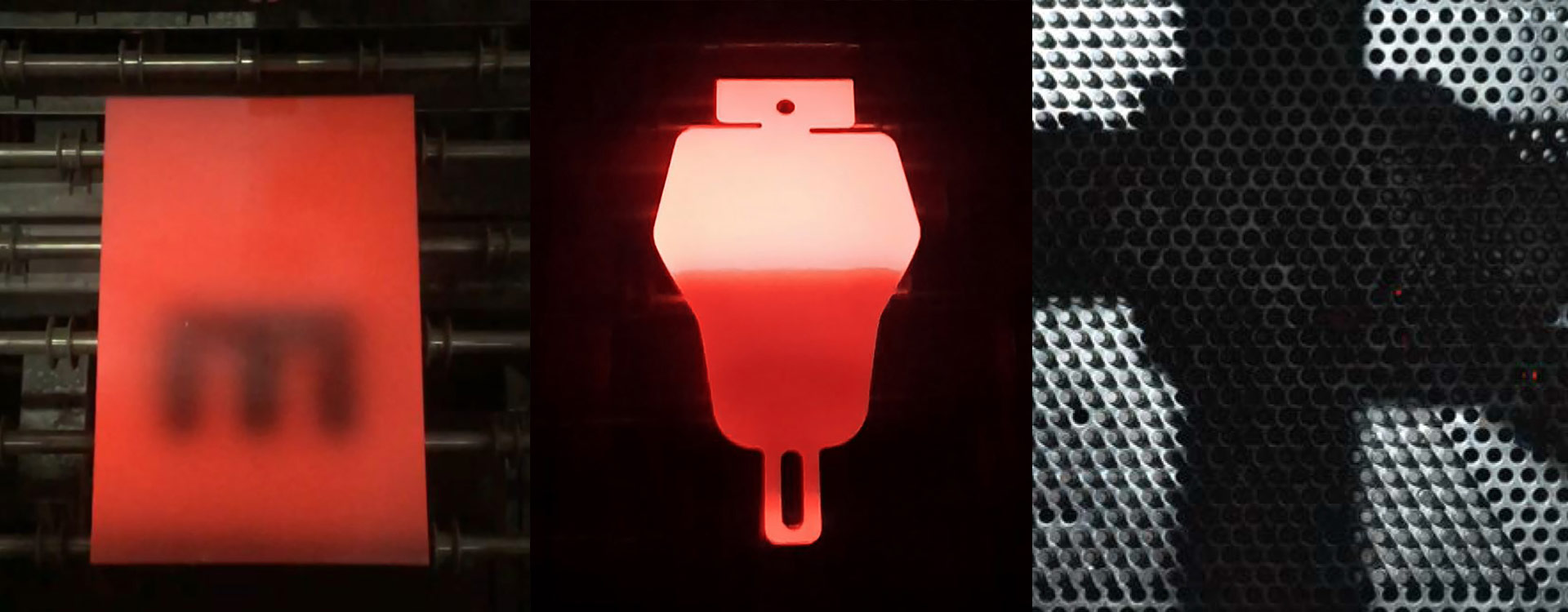