Strip cleaning facilities
/ Innovation & Technology, Success Stories
EBNER.blog | Hubert Bindreitner, EBNER Industrieofenbau, Austria
Strip cleaning facilities.
Integrated into annealing lines or as stand-alone equipment.
The incoming material for continuous strand annealing lines generally comes from a cold rolling mill, and the surface of the roll-hardened strip is generally covered with rolling lubricant, rolling lubricant emulsion and metal fines. This means that it is necessary to clean the strip before annealing.
Residual lubricants adhering to the surface of the strip negatively influence both the stability of the process and the quality of the strip. Furthermore, clean strip surfaces minimize contamination inside the furnace, and so increase the availability of a facility.
The development of EBNER strip cleaning systems
In the past, over 20 projects involving strip cleaning systems were implemented in partnership with Nisterhammer, a specialist in strip cleaning systems. During these projects, the complete automation system and all commissioning work were provided by EBNER.
When Nisterhammer shut down operations in 2014, EBNER was faced with the challenge of either finding an alternative partner or expanding its its existing knowhow and turning it into a new EBNER product.
The basic technology possessed by Nisterhammer was acquired, improved by a team of experts, and developed into a new line of products.
General principles and layout
A cleaning facility consists of 3 cleaning zones, with a dryer installed downstream of them. The individual zones are separated by pairs of squeeze rolls.
>> Cleaning zone 1: the high pressure zone
Hot demineralized water:, without any chemical cleaning agents added heats the strip and the rolling lubricant/ lubricant emulsion adhering to it. The lubricant and
emulsion are then washed off the strip. This is carried out at high pressure by special nozzles. A full-flow filtering process is then used to efficiently separate the mixture of lubricant and demineralized water in a coalesence separator.
Thus, clean water is again available for further use in the water circuit.
>> Cleaning zone 2: the brushing zone
In this zone, nozzles spray hot lye over the strip – or, in new design variants, no chemical cleaning agents are used. The film of lubricant still coating the strip is broken up by rotating brushes, which support the cleaning effect. This also washes off any remaining fines.
>> Cleaning zone 3: the rinsing
In the three-stage rinsing zone, the strip is rinsed with hot demineralized water to remove any alkaline residues.
The system is built as a series of cascades. Fresh demineralized water is only supplied to rinsing zone 3, and runs back to the upstream rinsing and/or cleaning zones. This ensures that the consumption of fresh water is kept low.
After the cleaning process, the strip runs through the HICON® dryer.
>> HICON® dryer
The high-convection dryer removes any residual moisture from the surface of the strip.
The following heating systems are available:
» Electric heating system
» Natural gas heating system
» Steam heating system
» Combined systems making use of waste heat from the annealing furnace
Integrating a strip cleaning facility into an annealing line
In 2019, two strip cleaning facilities were integrated into continuous bright annealing lines and successfully went into operation. The line at VDM Metals (Werdohl , Germany) processes thick special alloy (Ni-based, Fe-based, etc.) strip (see the report in HICON® Journal no. 02/2019, pp. 4 – 7). At Arinox S.p.A. (Sestri Levante, Italy), wide and thin precision steel strip is processed at high line speeds.
Strip cleaning facilities in stand-alone designs
Operating a strip cleaning facility as an offline unit can make good sense. Roll-hardened material that does not require a final heat treatment step can be cleaned without a complicated bypass of the furnace and the consequent loss of valuable annealing capacity.
Several annealing lines can be supplied with material from a central cleaning facility, meaning that the annealing lines do not require integrated cleaning sections. A stand-alone strip cleaning facility offers a high degree of flexibility, as the design of the facility does not need to take into account any limitations on line speed that may be required by the heat treatment process. Finally, as it is not absolutely necessary to operate the strip cleaning facility continuously, the strip handling systems can be relatively simple.
Advantages of the EBNER system.
Cleaning with pure demineralized water in the first cleaning zone
+ Low operating costs due to a 50 – 100 % reduction in the consumption of alkaline cleaning agents
+ Eco-friendly
Efficient separation of lubricant and water using full-flow filtering
+ Perfect cleaning results
+ Simple waste water treatment
+ Eco-friendly
Special roller bearings and guides
+ Elimination of strip off-tracking / wrinkle formation
Conductivity regulation in brushing and rinsing zones
+ Highly-stable process
+ Improved cleaning and rinsing results
Multiple uses of demineralized water (cascade principle)
+ Low demineralized water consumption (approx. 1 m³/h)
Use of waste heat from the furnace to heat the dryer and utility tanks
+ Low operating costs due to savings of up to 200 kWh/h
Fleece rollers used for final squeezing
+ Perfect drying results
SAVINGS IN UTILITY SUPPLY COSTS (LYE, ELECTRICITY, DEMINERALIZED WATER) OF 40 - 50 %, COMPARED TO STANDARD FACILITY DESIGNS
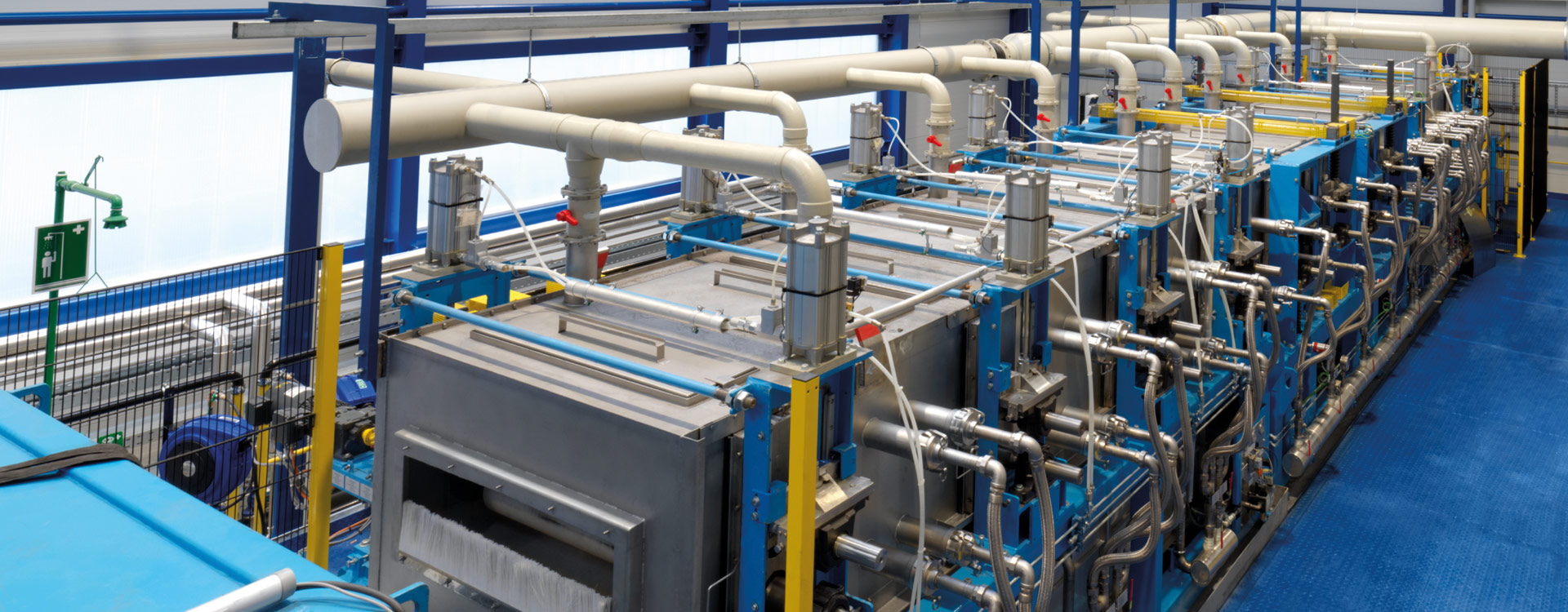