Zero-emission steel strip manufacturing
/ Success Stories, Sustainability
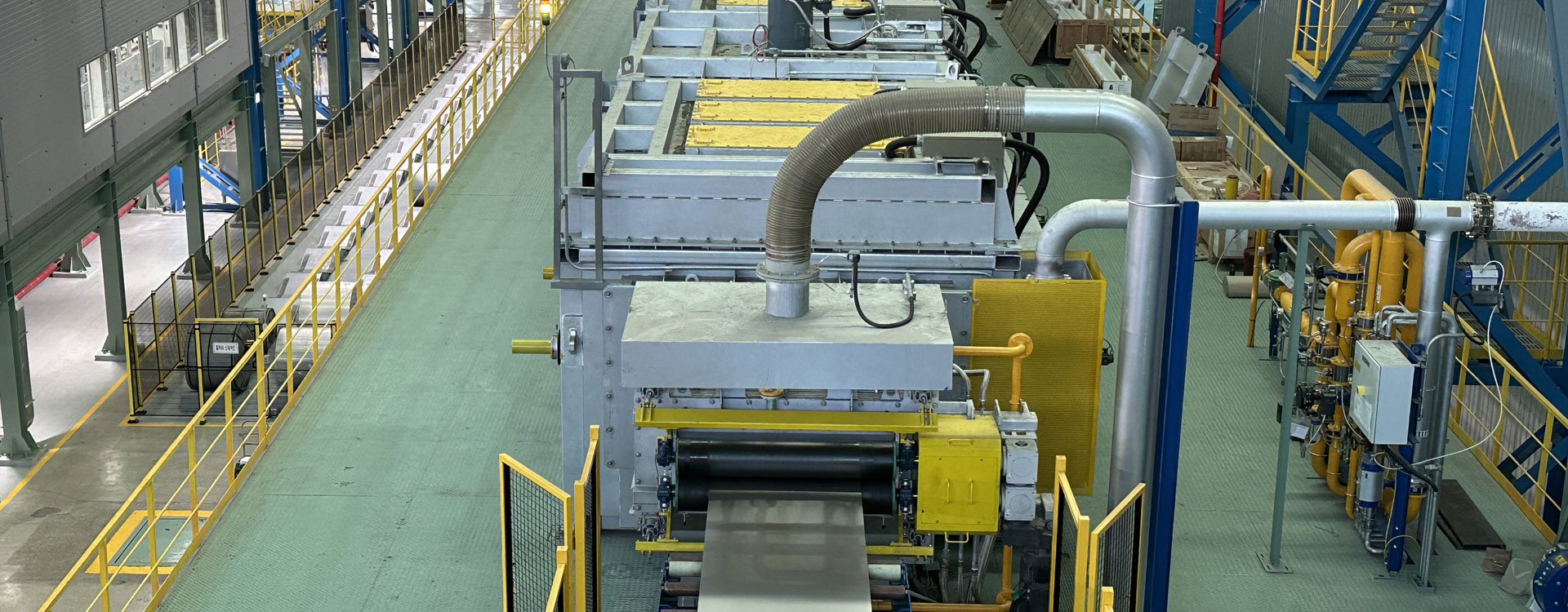
EBNER Industrieofenbau | Karl Wohlfahrt, Senior Sales Manager | Sascha Eppensteiner, VP Product Management
Zero-emission steel strip manufacturing
The Korean steel industry places its trust in green technologies from EBNER.
In a world where electrical energy and energy storage are constantly increasing in importance, battery manufacturing has become a critical industry.
Among the most powerful drivers of growth is the rising demand for battery-powered electric vehicles (BEVs), portable electronic devices and stationary storage systems for renewable energies. The lithium-ion battery (LIB) has emerged as the dominant technology used in these applications, and LIBs are now available in cylindrical, prismatic and pouch cell formats. Leading BEV manufacturers prefer cylindrical LIB cells due to their high energy density, long service life, high number of charging/discharging cycles, stable performance and the ease of heat management within a battery pack.
NEW FACILITIES SUCCESSFULLY COMMISSIONED
Asian manufacturers currently dominate the global market for battery cells, and further growth can be expected. This situation is underscored by the fact that, over the last two years, two GREENCAL® continuous annealing lines have been successfully started up – one at each of two leading South Korean manufacturers of cold rolled products. Both high-performance horizontal lines are designed to heat treat nickel-plated steel strip, which is then used to manufacture battery cell casings. The manufacturing process for cell casings requires extremely pure lowcarbon steel with a low proportion of alloying elements and excellent deep drawing characteristics. This unique combination of properties is created in a special heat treatment process. The goal of the process is to produce a fine, oxide-free and isotropic grain structure that provides excellent longitudinal and lateral formability and inhibits earing during deep drawing. A diffusion process is then used to create the bond between the nickel plating and the steel substrate. Depending on the thickness of the strip, the desired mechanical properties, the thickness of the diffusion zone and the application of the end product, a variety of routes may then be used to manufacture the strip.
TCC Steel, headquartered in Pohang, South Korea, has already seen success in this market sector and their investment in a high-capacity facility has made them even more competitive.
Dongkuk Industries, also with a manufacturing plant in Pohang, has been strategically diversifying its product portfolio to enable it to enter the most promising markets. By investing in a high-capacity continuous annealing facility for deep-drawn battery steels, as well as in additional equipment, Dongkuk has opened up new markets for itself.
ADVANCED FACILITY TECHNOLOGY
The demands of the future – particularly those posed by e-mobility – are challenging all of us to design processes that are more sustainable, even as they remain competitive. It was with these challenges in mind that EBNER developed the designs for both GREENCAL® continuous annealing lines, designs in which energy efficiency, the elimination of emissions and the maximization of productivity played a central role. At the same time, the facilities had to fulfill the highest demands for quality. A single one of these processing lines is capable of employing every processing technology used in the manufacture of nickel-plated steel strip, from normalizing and diffusion annealing to short anneals.
The combination of extremely pure process atmosphere, high convection and radiant heating leads to extremely precise temperature distribution across the width of the strip, even as it provides reproducible material properties.
The entire facility is exclusively heated with electricity, ensuring that there are no local carbon or NOx emissions. This makes the use of this technology of particular interest to OEMs of batteries or electric vehicles.
TECHNICAL DATA OF GREENCAL® LINES OF THIS TYPE:
Strip width: up to 1.220 mm
Strip thickness: 0,1 – 1,0 mm
Strip speeds: up to 100 m/min
Throughputs: up to 120.000 t/a
Annealing temperatures: up to 1.020 °C
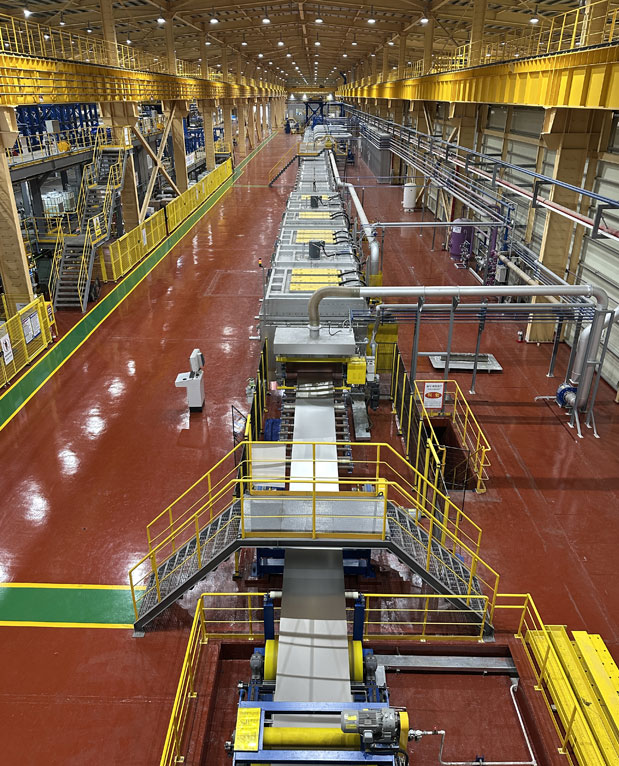