Hardening and tempering technology for aluminum plates
EBNER.blog | Andreas Steinmassl, EBNER
EBNER hardening and tempering technology for aluminum plates.
Efficiency, temperature uniformity, quench technology and high quenching rates: these are the key characteristics EBNER roller-hearth furnace facilities are provided with to fulfill the strict requirements of the aerospace industry.
For years, the requirements placed on aluminum plates used to manufacture aircraft components with the durability to be exposed to high stresses have been the driving force behind the rising quality and process reliability of aluminum production. Prominent examples of this are the provisions of the AMS 2750 standard for heat treatment, which form a challenging package of requirements that must be fulfilled by the suppliers of furnace technology. EBNER stands out as a technology leader in this field, as difficult approaches to requirements represent ideal challenges for us to face.
The first EBNER roller-hearth furnace to solution heat treat aluminum plate went into operation over 30 years ago. Even back then, the quality requirements placed by the aerospace industry were taken into account and fulfilled. Nevertheless, since that time, the technology has been strongly advanced through close cooperation between the EBNER R&D team and the EBNER Engineering Department. A significant role was also played by the close tailoring of development to our customers’ needs. Continuously rising requirements provided the input we needed to focus ourselves on the necessary core technologies.
Factors determining the quality of a finished plate include temperature uniformity and rapid, even quenching in a water quench. We placed our primary focus on these two parameters and developed a clear competitive advantage.
To achieve temperature accuracies better than ± 2 °C during soaking, each furnace zone was divided into eight temperature control zones that could be regulated individually. In addition to the granular subdivision of heating zone temperature regulation, EBNER developed a precise process cooling system that compensated for excess energy in the process and prevented even minimal spikes in temperature. This system works hand in hand with the principles of the proven EBNER HICON high-convection system. Large, high-pressure impellers are powered by frequency-controlled motors with an energy efficiency class of IE4. This system ensures that the furnace atmosphere has an extremely high circulation rate, and the resulting high speeds at the air emission nozzles provide superior heat transfer coefficients.
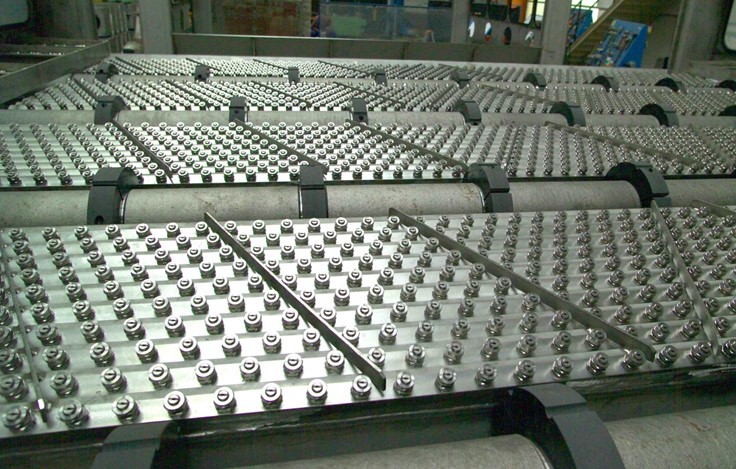
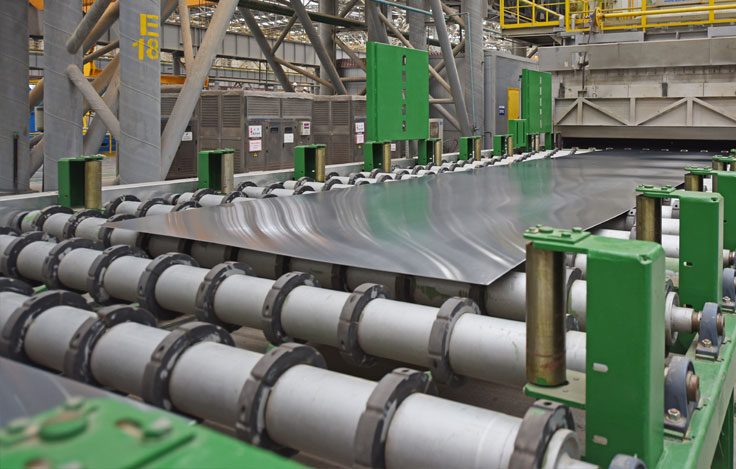
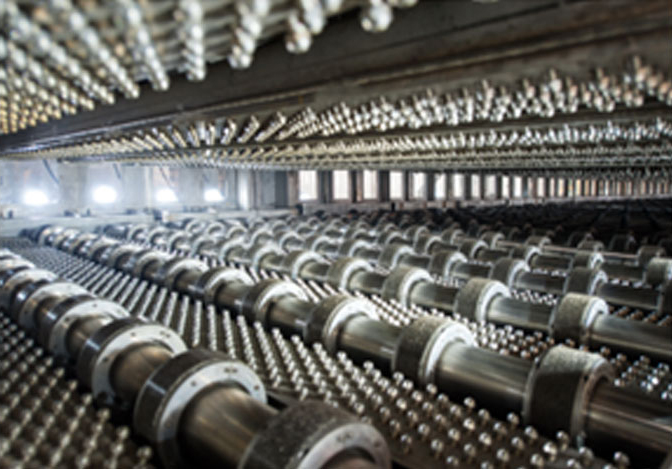
EBNER hardening and tempering technology for aluminum plates
As soon as the soaking time has expired and the solution temperature has been reached, the quenching process starts. An EBNER quench is comprised of three main zones: the high-pressure quench, which provides the critical cooling of the plate down to below abt. 200 °C, the low-pressure quench, in which cooling is completed and any reheating of the plate due to residual energy in its interior is prevented, and finally the dryer, where any remaining water is removed from the plate.
Decisive in determining the metallurgical characteristics of the plate is the first quenching step, which at EBNER roller-hearth furnaces is carried out in the high-pressure quench. The height of an EBNER high-pressure quench is adjustable, meaning that the process is extremely flexible and can be adapted to widely different plate thicknesses. The plates are quenched symmetrically from
above and below, with identical distances between the surfaces of the plate and the nozzles. This symmetry ensures extremely uniform quenching throughout the entire thickness of the plate. The special arrangement of the high-pressure nozzles also helps ensure the uniformity of quenching across the plate, as the nozzle array of the high-pressure quench ensures that the cooling rate remains linear across the width of the plate. Yet another significant advantage is that, due to the high pressures that are used, the film of water that forms on the plate is constantly penetrated. In contrast to conventional quenching systems, fresh cold water is repeatedly applied to the surfaces of the plate and a Leidenfrost (vapor film) effect is prevented. All of these quench features ensure homogeneous metallurgical characteristics, which are reflected in the results of conductivity tests.
To increase the energy efficiency of the system, EBNER roller-hearth furnaces can also be equipped with charging roller tables that enable hot plates (plates that retain residual heat from the rolling process) to be charged. As may be expected, higher temperatures at the furnace entry result in shorter heating-up times and so reduce energy consumption.
To sum it all up, one can say that EBNER roller-hearth furnaces are currently the technical and technological benchmarks for the industry. Additional developments and concepts are already in the design phase, and our R&D and engineering teams are working hard to refine them and make these new systems ready for the market.