Gautschi Hybrid Vario Mold for ingots
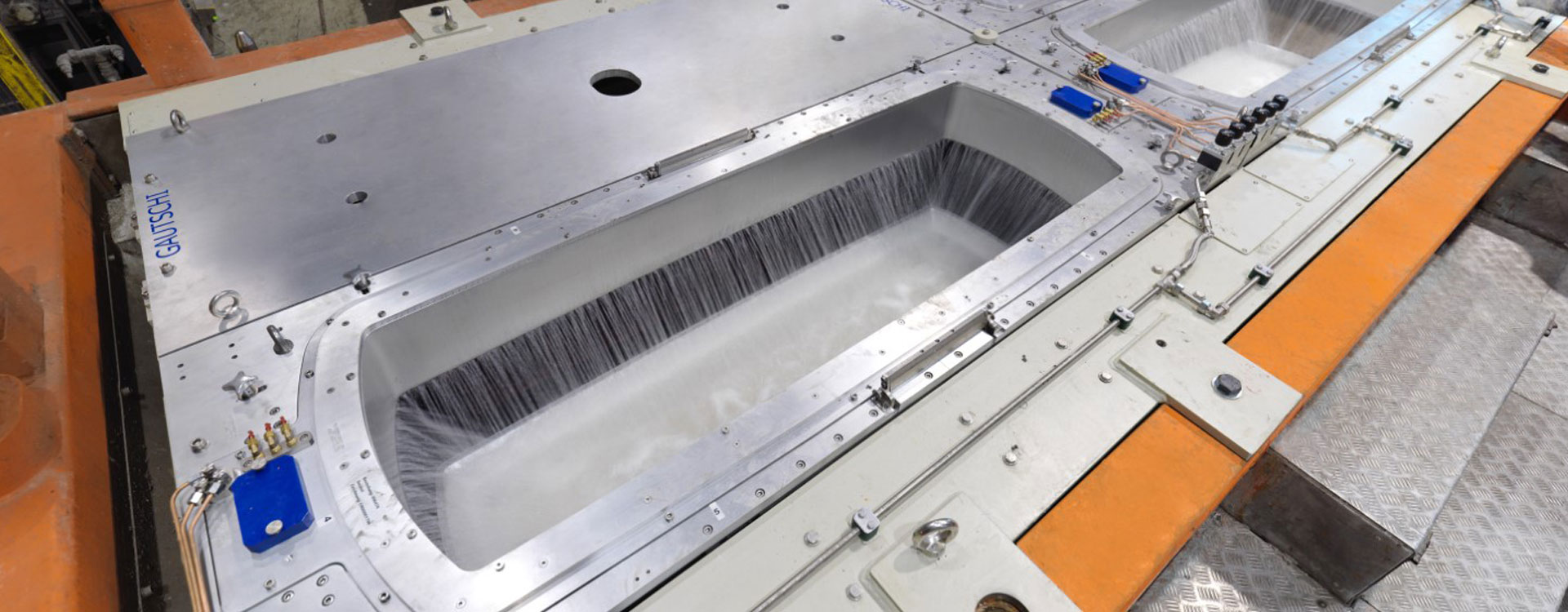
Gautschi Engineering | Stefan Pelech, Managing Director
The history of the Gautschi Hybrid Vario Mold (HVM) for ingots
Rolling ingots are the starting material used to manufacture aluminum sheet, and are produced in a continuous vertical casting process (VDC). The heart of any vertical continuous casting unit is the mold, which has a significant impact on the quality of an ingot and thus on the end product.
Gautschi Engineering GmbH’s Hybrid Vario Mold (HVM), designed for rolling ingots, stands out due to its precision design and high efficiency. These features directly lead to improved product quality and increased production capacity.
THE ROAD TO SUCCESS – MILESTONES IN DEVELOPMENT
2016 – THE DECISION TO DEVELOP AN INGOT MOLD
For decades, established manufacturers have been striving to continuously improve and simplify the processes used in mold-based production. These efforts inspired Gautschi Engineering GmbH to intensively investigate the topic and make it their area of special expertise.
Dedication and a visionary goal led Gautschi to develop an innovative ingot mold, which was introduced in October, 2016. This new technology allowed aluminum to be cast in a continuous and controlled process, and today this ingot mold still stands out due to its advanced cooling technology and the precise control it provides over the casting process.
2017 – A NEW TESTING GROUND AND VALUABLE INSIGHTS
In cooperation with Stockach Aluminium GmbH and AS Oxidwerke GmbH, both based in Germany near Lake Constance, Gautschi began to conduct its own series of tests and trials. Gautschi was given access to a large unused casting pit, which the company could then use to conduct testing. Gautschi began to conduct trials with customers from across the globe, allowing valuable data to be collected and know-how to be exchanged. This visionary and practical approach allowed Gautschi to respond to specific requirements of the international market.
2018 – THE FIRST STEP INTO A NEW ERA
The first casting unit with the new Hybrid Vario Mold (HVM), in a 535 × 1680 mm format, successfully went into operation at a well-known aluminum manufacturer’s works in 2018. This important step demonstrated how traditional production processes could be optimized through innovative technologies – a realization that formed the cornerstone of further development.
2020 – EXPANSION AND TECHNOLOGICAL BREAKTHROUGHS
2020 marked a turning point, with two critical developments:
- Product range expanded:
- Following successful commissioning of the first casting unit, the same customer installed a second unit at their works that supported ten different formats (ranging from 535 × 1140 to 535 × 1770 mm). For the highest possible quality and greatest possible reliability during every cast, alloys like 6016, 6061, 5754, 5052 and 3003 were used.
- Patents boost innovation:
- Alongside expansion of the product range, the design of the new Hybrid Vario Mold (HVM) was further refined and successfully patented. This technical highlight underlined Gautschi’s commitment to continuously raising the bar for casthouse technologies.
2020 – OPENING OF THE CASTHOUSE (R)EVOLUTION CENTER IN RANSHOFEN, AUSTRIA
Gautschi’s close collaboration with HPI High Performance Industrietechnik GmbH, based in Ranshofen, Austria, led to the idea of creating a shared testing center and moving Gautschi’s headquarters from Switzerland to Ranshofen. This test center would incorporate facilities for both horizontal and vertical casting, allowing the entire spectrum of technologies to be covered and an extended range of services to be offered. Following careful planning, construction of the testing center and commissioning of the pilot casters was completed in 2020.
The CASTHOUSE (R)EVOLUTION CENTER, or C-R-C, had become a multi-story testing center that, along with the office building, offered over 1000 m² / 10,700 square feet of space. Construction of this state-of-the-art R&D casthouse has made it possible to test and refine advanced designs under real production conditions, and insights drawn from practical experience are directly applied to optimize processes.
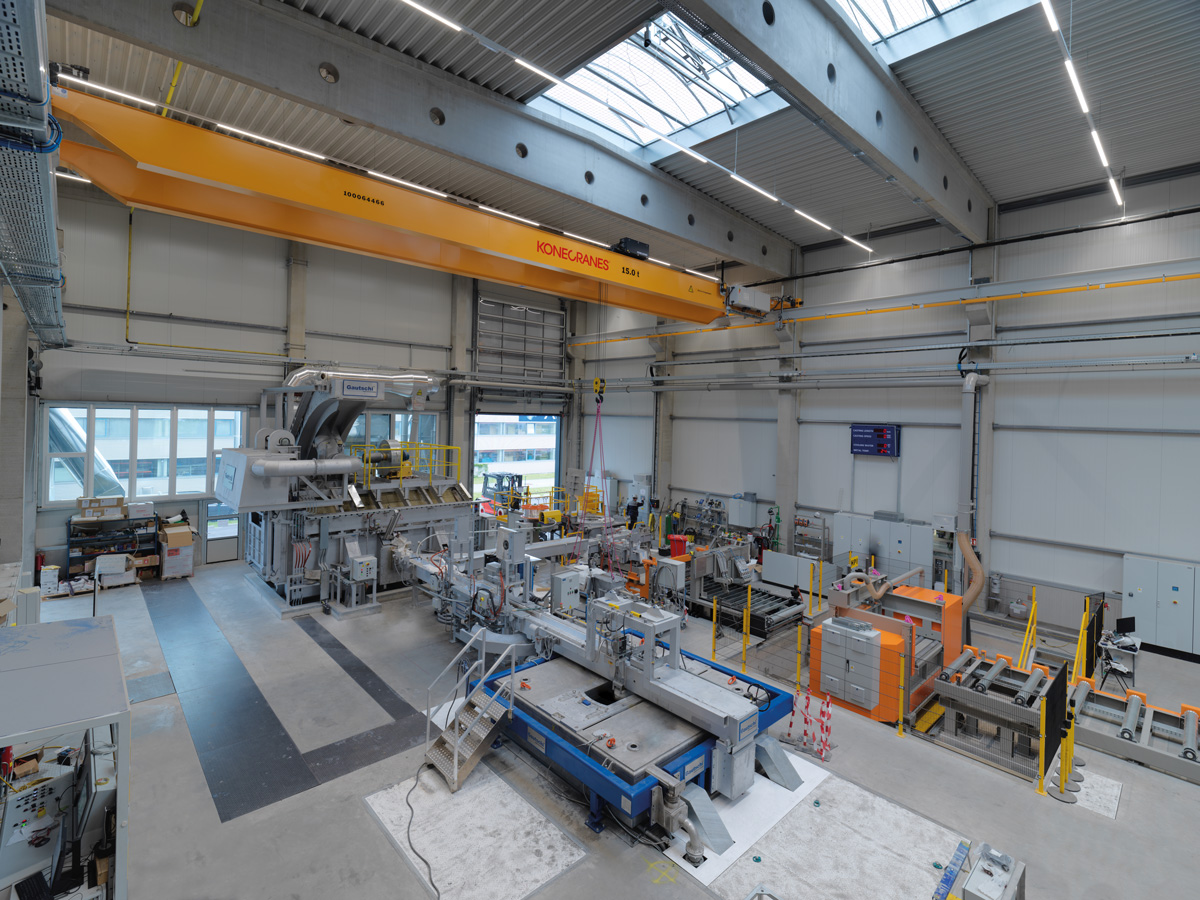
2024 – EXPANDING PRODUCTION CAPACITY
The success story of the Gautschi ingot mold was continued in 2024, as a third casting unit designed for HV molds went into operation. A custom design for one of our partners, this new unit is also able to handle additional casting formats such as 35 × 1920 and 535 × 2120 mm. Proven alloys such as 6016, 6061, 5754, 5052 and 3003 continue to be in use, a clear confirmation of the quality and efficiency of the system.
Selected parameters and technical advantages
- Butt curl: varies between 20 and 50 mm
- Butt swell: virtually absent
- Scrap: less than 1 %
- Safety: initial casting is fully automated
These features lead to savings in both materials and costs, as ingots require a reduced amount of machining before any downstream process. Furthermore, the safety of the operators in the production area is improved.
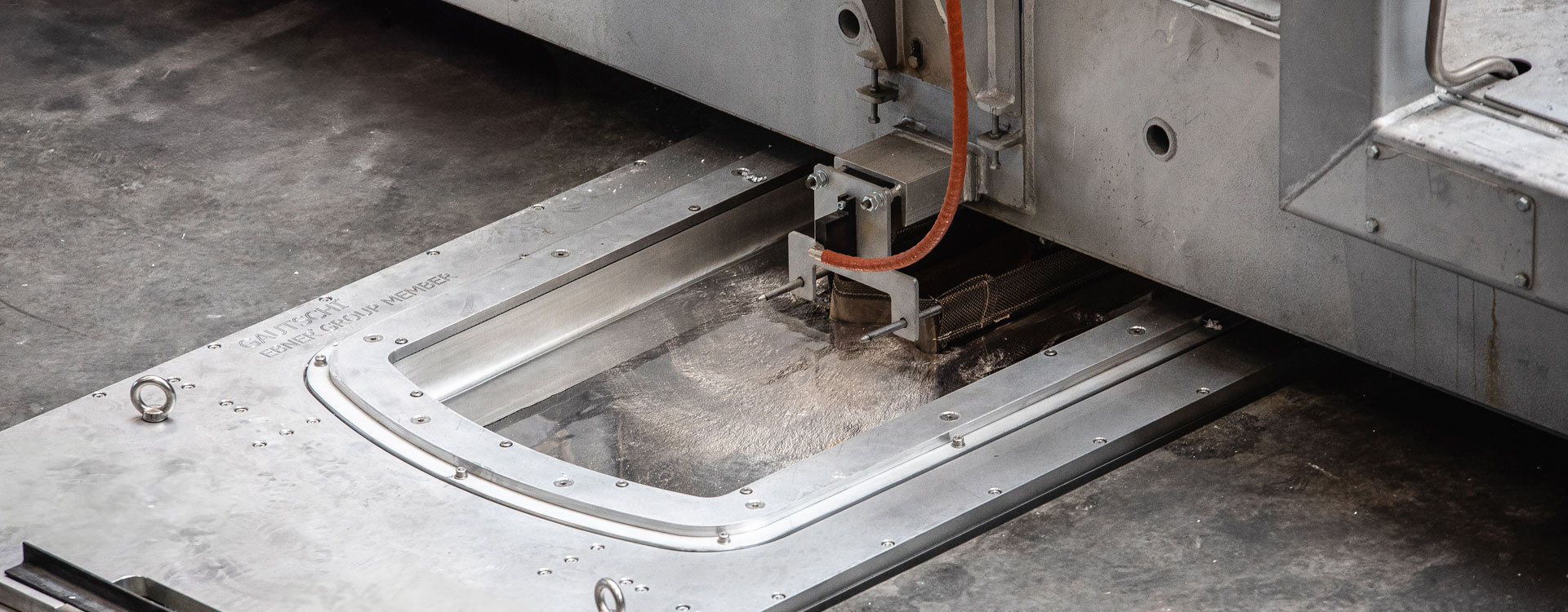
TECHNICAL EXCELLENCE MEETS THE MARKET
The continuous improvement of our ingot molds is founded on the successful give-and take between our technological know-how and intensive practical experience.
The tireless effort to apply state-of-the-art manufacturing technologies has made Gautschi a leader in the field.
Gautschi’s Hybrid Vario Mold (HVM) is the benchmark for:
- Highest degree of precision
Optimized casting processes and customized formats ensure extremely accurate results during production. - Flexibility and range
The wide variety of aluminum alloys that are supported and the mold’s ability to be adapted to different casting formats means that our mold offers tailor-made solutions to the most demanding production requirements. - Innovative research
By merging in-house expertise with current trends, Gautschi is constantly setting new standards in casthouse technology.
THE FUTURE OF MANUFACTURING – TAKE THE LEAD WITH GAUTSCHI
Gautschi unites decades of experience with pioneering technologies. The Gautschi ingot mold, as well as the Hybrid Vario Mold developed from it, are not just state-of-the-art solutions – they also provide a decisive competitive advantage.