Sustainable heat treatment
/ Innovation & Technology, Sustainability
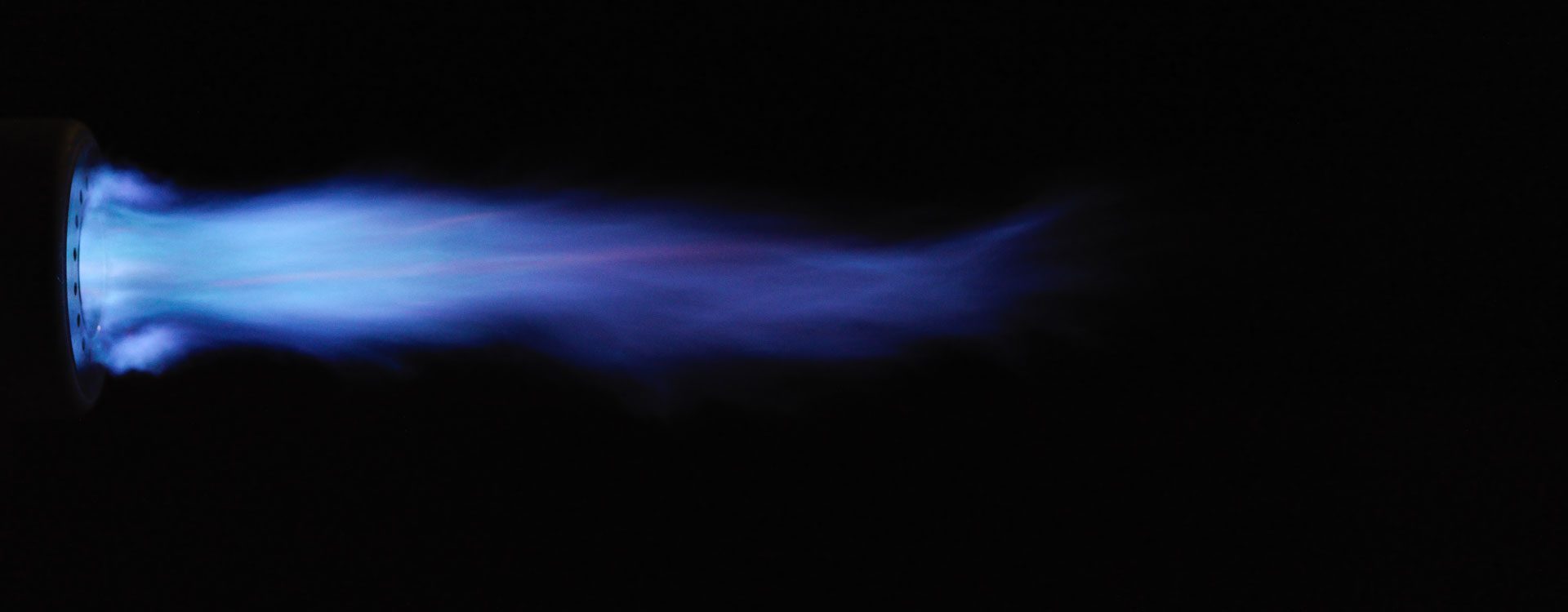
EBNER Industrieofenbau | Peter Seemann, VP Research & Development | Michael Koller, Senior Manager
Sustainable heat treatment
The future of EBNER burner technology.
Burner technologies play a central role in industrial heat treatment – whether in terms of efficiency, emissions or an ability to be adapted to alternative fuels. For decades, EBNER has been developing innovative burner solutions for heat treatment furnaces, constantly raising the bar for the rest of the industry. In a recent interview, EBNER’s Peter Seemann (Vice President Research & Development Ferrous) and Michael Koller (Senior Manager R&D Ferrous) spoke about current developments, current challenges and the future of burner technology.
BURNER TECHNOLOGY AT EBNER
What role does EBNER play in the development of innovative burner solutions for industrial furnaces?
Seemann: EBNER develops its own burner solutions for the majority of its facilities. In-house development allows us to optimally respond when integrating burners into different types of furnaces. The EBNER product range offers a wide variety of burner technologies – from classic gas burners to flameless burners and hydrogen-powered solutions.
Given that variety, what has been your core approach to development?
Koller: Our feeling of responsibility towards the environment and future generations inspired us early on to begin development of low-emission, sustainable combustion technologies. This produced various innovations, including our own flameless burners, which not only meet increasingly strict NOx emission regulations, but also follow our vision of “Driving Green Technologies”. At the same time, there was a need to address future market requirements for carbon-neutral heat treatment solutions. This led to the development of our hydrogen burners. As long as “green” hydrogen is available in sufficient quantities, these burners allow a heating system to be fully carbon-neutral – an important step towards a climate-friendly industry.
How do the various EBNER burners differ in terms of technology, efficiency, emissions and area of application?
Koller: EBNER employs heating systems that heat both indirectly (using radiant tubes) and directly. The efficiency of these systems, as well as their emissions, depend on a number of factors. These include the processing temperature, burner output and the temperature to which the combustion air is preheated. The main factors determining their areas of application are first, direct versus indirect heating and second, the type of heat treatment facility – that is, whether it is for steel or aluminum.
Over the last few years, which technological trends have influenced development? Is there a general direction in which all burner designs are headed?
Seeman: A constant effort is being made to increase combustion efficiency, while reducing pollutant emissions at the same time. In addition to that, over the last few years there has been intensive research into the combustion of fuel gases with widely different compositions – mixtures of hydrogen and natural gas, synthetic gases or ammonia. The goal of development is to allow zero carbon or low carbon combustion.
What makes EBNER burners stand out?
Koller: EBNER only develops all-metal burners, which are designed to operate in furnace temperatures up to 1250 °C. In-house design and manufacturing contribute significantly to the exceptionally long service life of our burners.
Are EBNER burners only used for heat treatment, or are they also used in other applications?
Koller: At this time, our burners are only used in facilities we manufacture. Their future use in non-EBNER facilities, as well as in other industries (for example, in equipment used to manufacture cement, bricks, elastomers, glass or carbon) is a major focus of our ongoing research and development work.
CHANCES AND CHALLENGES
Which challenges currently shape the development of burner technologies?
Seemann: One of the greatest challenges is the conflict between the goals of increasing efficiency and reducing NOx emissions. A solution may be found in intelligent control technology, which allows burners to be controlled very precisely. Additional challenges are posed by the growth of hydrogen as a fuel gas, which remains uncertain.
EBNER has over 43 years of experience in burner development. How has the technology changed over the last few years?
Koller: At new facilities we see an increasing number of measures to reduce NOx emissions, including external exhaust gas admixing and flameless burners. SCR systems for secondary NOx reduction are also installed in particularly strict regulatory environments. Furthermore, a focus is currently being placed on hydrogen-fueled and hybrid burners.
SUSTAINABILITY AND INNOVATION IN BURNER TECHNOLOGY
How does EBNER burner technology contribute to reducing emissions and energy consumption?
Seemann: The use of large recuperators can lead to additional energy savings. Flameless technology already allows extremely low levels of emissions to be achieved.
How does EBNER make sure its burner technologies remain competitive over the long term?
Seemann: Burners are continuously optimized, both in terms of energy efficiency and emissions behavior. Regular testing in our in-house testing facilities allows us to rapidly put new developments into practice. EBNER also cooperates with research institutes in both Austria and Germany.
How flexible are EBNER burners when being integrated into existing facilities or switching between different types of fuels?
Koller: During burner development, great care is taken to ensure that the burner can be integrated into existing facilities with minimal effort. That is the case, for example, with our hybrid natural gas/hydrogen burner.
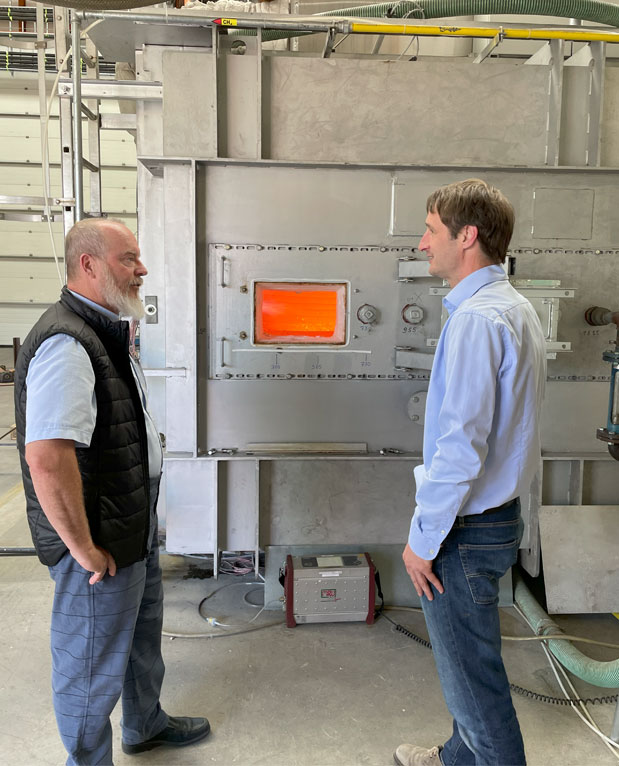
OUTLOOK
Does EBNER see a future for burner technologies that employ electric heating?
Seemann: Direct electric heating will play an increasingly important role, particularly in heat treatment. However, for high-temperature processes plasma burner technology will remain crucial, as it allows very precise temperature regulation. EBNER has already developed innovative solutions such as our plate heating system, GREENBAFx® bell annealers and electric radiant tubes.
GREENBAFx® furnaces were introduced in 2024, and it was said that they marked a new generation of bell annealers. Why?
Seemann: Many companies are placing their trust in hybrid heating solutions, and in GREENBAFx® EBNER has combined electric and gas heating systems in a single facility. This allows fossil fuel and electrical power sources to be used flexibly, reducing both emissions and operating costs.
What technological innovations will shape the future of burner technology?
Koller: Of particular importance for the future of burner technologies is the development of solutions for decarbonization, along with carbon-neutral methods of heating. In this regard we can look back on the years of development work carried out in our in-house TECHCENTER, during which we successfully introduced our hydrogen- fired ECOBURN H2 FLEX burners to the market and made significant progress in the development of plasma burner technology.