GREENBAFx
/ Innovation & Technology, Sustainability
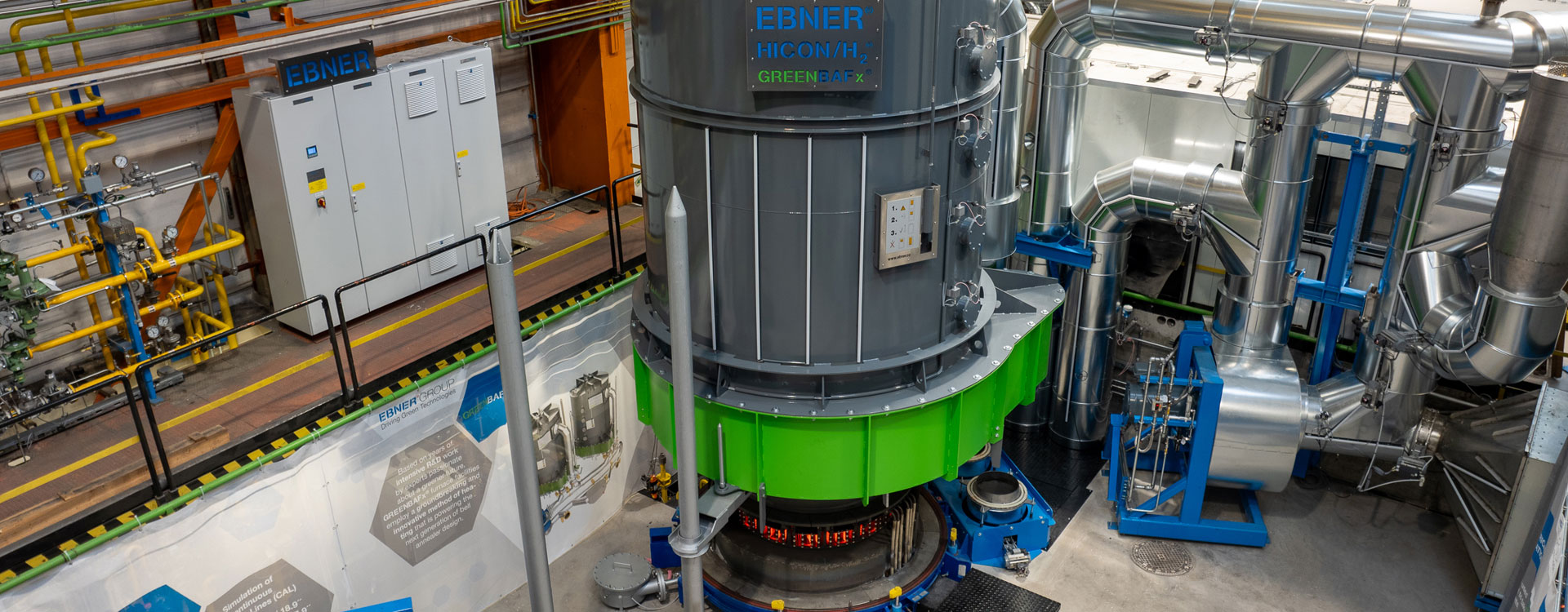
EBNER Industrieofenbau | Sascha Eppensteiner, VP Product Manager | Peter Seemann, VP Research & Development
GREENBAFx®
The next generation of sustainable HICON/H2® bell annealer facilities.
Bell annealer facilities are integral parts of cold rolling mills, where they are used to carry out heat treatment processes. EBNER has been involved in the development of heat treatment processes and the manufacture of heat treatment equipment for decades, constantly introducing innovations that have advanced the industry. For example, EBNER introduced bell annealer technology that combined high convection (HICON®) with straight hydrogen as a process atmosphere (HICON/H2®) all the way back in 1972. The first HICON/H2® bell annealers were designed to process copper base metals, but further development led to designs for the steel industry in 1982. The technology quickly established itself, revolutionizing the heat treatment of semi-finished products.
HICON/H2® bell annealers have been successfully operating for decades. Continuous development has increased their performance even as it has lowered costs, allowing the industry to take decisive steps forward in both quality and economy.
Over 4900 HICON® workbases are in operation today, processing over 80 million metric tons of flat and wire products every year.
Our past and current success is, however, only a starting point. The demands of the future are challenging the entire industry to design processes that are more sustainable, even as they remain competitive. With this challenge shaping our perspective, we invested several years of intensive effort in the development in what we intended to be the next generation of bell annealer furnaces. During development, an emphasis was placed on maximizing energy efficiency, eliminating emissions and simplifying operating sequences.
Our efforts have been rewarded with what is indeed the next generation of sustainable bell annealers, referred to as GREENBAFx® furnaces. These facilities feature innovative systems for inserting thermal energy into the process (direct heating) and for recycling energy released during cooling (heat exchange). During development, two main use cases were taken into account (see figure 1).
A standard design with direct heating (the “basic case”). An expanded design with heat exchange (the “advanced” case).
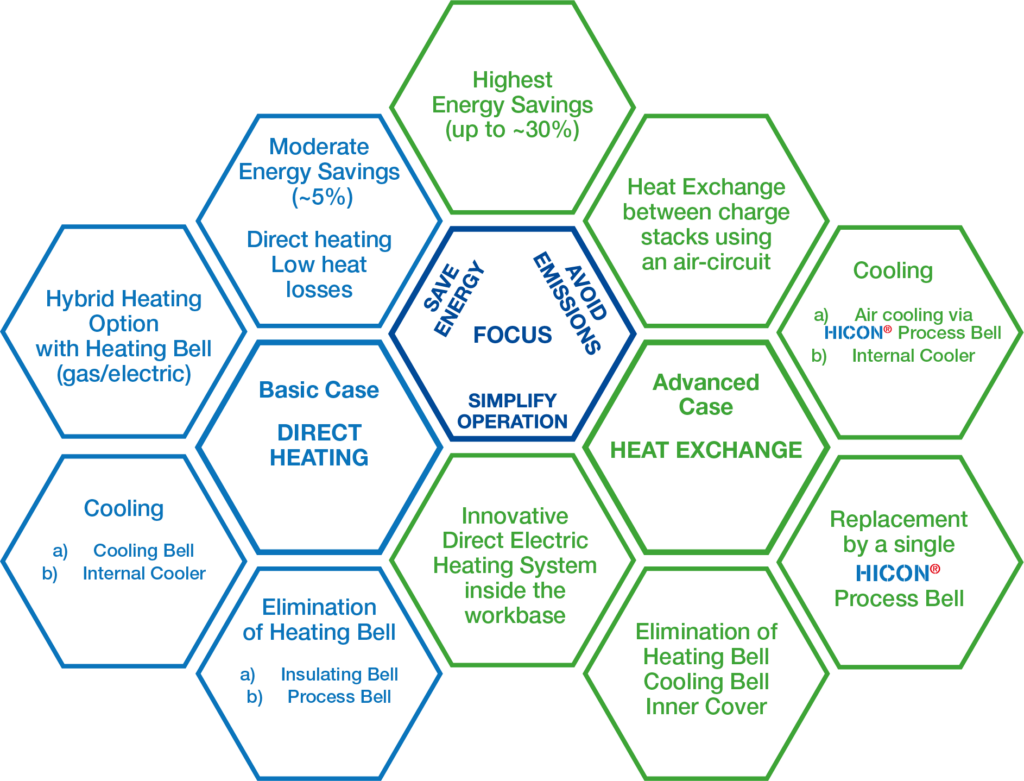
GREENBAFx® FACILITY WITH DIRECT HEATING (the “basic” case)
At traditional bell annealer facilities heating is carried out by a heating bell, which is placed over an inner cover. The interior of the inner cover forms the processing chamber, in which is the charge. Thermal (heating) energy is supplied from the heating bell, which radiates heat onto the inner cover. The inner cover then conveys the thermal energy into the processing chamber and atmosphere convection is used to transfer the energy to the charge.
Cooling employs a similar method. A crane is used to replace the heating bell with a cooling bell, which uses cooling air and/or cooling water to subtract the thermal energy. Usually, energy subtracted during cooling either remains unused (is lost) or only recycled in an inefficient manner (e.g. converted to electricity in an ORC process, used to heat water, etc.).
The new, patented GREENBAFx® system takes a different approach. In this design, the thermal energy from heating is fed directly, without detours, into the process atmosphere. To do so, an electric heating system with a high power density is integrated into the workbase itself (in the diffuser).
The workbase fan impeller is designed to ensure an ideal flow of atmosphere to the heating system, with no flow losses. In fact, it was discovered that the heating system has a positive effect on atmosphere distribution – that is, atmosphere flow is even better than that found at a typical bell annealer.
Furthermore, to prevent residual rolling lubricants from collecting on the electric heating elements, a special temperature/atmosphere program was developed. This program cleans the heating elements before every anneal.
All of these features mean that the need for a heating bell is eliminated: it can be replaced with a simple insulated bell (figure 1, option “a”). In this case cooling is still carried out with a standard cooling bell.
Alternatively, the heating bell, cooling bell and inner cover can be replaced by a single “process bell” (figure 1, option “b”). This bell encapsulates and isolates the processing chamber. It allows the entire heat treatment process, from the time the processing chamber is sealed (clamped) to the time it is released, to run fully automatically. In this case, cooling employs a cooling system installed in the workbase (an “integrated cooler” – see figure 1, option “b”).
With a process bell, there is no need to exchange heating bells for cooling bells. This greatly simplifies operational and logistical burdens, as significantly fewer crane movements and operator interventions are required. In fact, only two (2) crane movements are needed – one when the process bell is placed, and one when it is lifted off the workbase. Compared to a typical bell annealer facility, where six (6) crane movement cycles are necessary, this represents four (4) or 66 % fewer crane movements per anneal. This also reduces processing times by a small margin.
Another advantage of this design is that less space is required than at traditional bell annealer facilities. That is, as the “passive” process bell has a significantly smaller diameter than a heating bell and no external equipment (ducting, etc.) is required, the longitudinal distance between workbases can be reduced. Furthermore, as each workbase now has its own integrated heating system, there are no waiting times for a heating bell to become available and no throughput is lost.
Heat losses are reduced to a minimum, meaning that the facility can operate extremely efficiently. Zero emissions are created, with both CO2 and NOx emissions eliminated. Finally, energy consumption is up to 5 % lower than that at a typical bell annealer facility.
In the “basic” design, an optional possibility is to equip the facility with hybrid heating. If this option is selected, the facility is equipped with a heating bell. Charges can then be processed using either the integrated electric heating system of the workbase or with the gas-fired (natural gas, hydrogen) heating bell (see figure 2).
The advantage of this option is that the user can select the heating method flexibly, for example based on the current availability or price of utilities.
This hybrid heating option can generally be retrofit into existing facilities.
GREENBAFx® FACILITY WITH HEAT EXCHANGE (the “advanced case”)
The goal of heat exchange is to return the energy released during cooling to the process. This is done by using the energy to preheat a cold coil stack on a neighboring workbase.
A HICON® process bell allows air to be forced through the annular gap around the exterior of the encapsulated processing chamber (the integrated inner cover) at high
speed, enabling the air to be used for cooling. This air becomes heated and, as it is now transporting thermal energy, it is fed into an insulated heat exchange circuit. Automatic dampers then lead it to another HICON® process bell, under which another charge is ready for heat treatment, and the air preheats the charge (see figure 3).
A crucial element in this design is that heat exchange takes place across the exterior of the integrated inner cover, ensuring that safety (the composition of the atmosphere beneath the inner cover) is not influenced.
As a HICON® process bell transfers the thermal energy collected during cooling to the heat exchange system, heat stored in the mass of the furnace components (tara mass) is also transported. If a slow cooling process is needed to fulfill technological requirements, the energy released during that process is also used.
This amount of heat exchange means that it is possible to return up to 30 % of the total energy of a heat treatment cycle back to the process, providing an excellent financial advantage.
At the end of a heat treatment process, final cooling of the charge can employ either air cooling provided by a HICON® process bell or a heat exchanger (“integrated cooler”) installed in the workbase. The thermal energy from air cooling can be supplied to a central pipe end and tied in to another unit, such as an air/water or air/ oil heat exchanger. This makes it possible to recycle still more energy by employing it in an external process.
Figure 4 shows the typical time/temperature profile of a 710 °C / 62 t anneal with heat exchange.
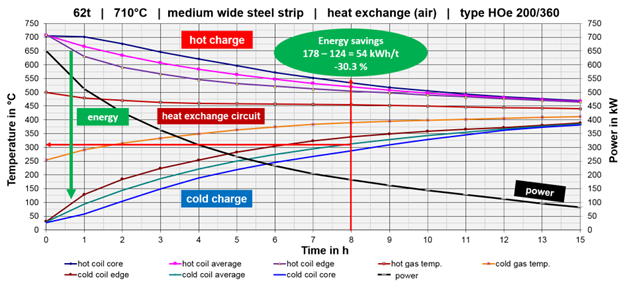
In this anneal, thermal energy is drawn out of the exterior of the coils (from the strip edges) by high-convection hydrogen, transported to the interior wall of the process bell (integrated inner cover) and then transferred to the circulating stream of air (high-temperature gas). On the bottom side of thefigure below, it can clearly be seen how the high-convection hydrogen takes thermal energy from the interior wall of the process bell (the integrated inner cover) and transfers it to the exterior of the coil. The temperature of the hot stream of air falls from around 500 °C at the start of heat exchange (when the gas exits process bell 1) to about 250 °C (when it leaves process bell 2).
The energy that is released is that which is used to heat the cold charge, and the drop in the core temperature of the charge that is being cooled and the rise in the core temperature of the charge that is being preheated can be clearly seen. The average coil temperature thus represents the amount of energy that has been transferred to the cold coils. Of particular interest is the fact that the hot stream of air flowing from one process bell to the other remains fairly constant for several hours, even as the temperature of the air being returned gradually increases and the amount of energy that is being transferred falls.
An economical and optimal balance of factors must be found, as while more energy can indeed be collected by extending the duration of heat exchange this reduces the throughput of the facility at the same time.
In the example shown here, the energy consumption of the heat treatment process with heat exchange is abt. 124 kWh/t. When compared to a typical annealing process, which has an energy consumption of around 178 kWh/t, this means that an energy saving of 54 kWh/t or 30.3 % can be achieved after 8h of heat exchange.
If anneals are carried out at high temperatures (e.g. 850 – 900 °C), even more energy can be recovered.
Note that the heat exchange time is not a pure “loss” that reduces the throughput. Part of the time often runs during a technological slow cooling phase, and the heating time required by the integrated heating system is shorter (as the charge does not start at ambient temperature, having been preheated to around 310 °C).
Furthermore, from a technological point of view a minor extension of the time has a positive effect on coil quality. The slow heating-up rate aids the evaporation of rolling lubricants, while a slow cooling rate helps prevent stickers between wraps.
Thermal recovery, alongside other high-efficiency features of the GREENBAFx® design, is an approach that reduces emissions even as it provides significant financial savings.
That is, in comparison to a classic gas-fired facility, a GREENBAFx® annealer allows an enormous reduction in the amounts of CO2 and NOx that are expelled. For example, at a facility with a throughput of 250,000 t/y, annual emissions would be reduced by around 9055 t of CO2 and around 11.8 t of NOx. The savings in electrical power, when compared to a classic bell annealer with an electric heating system and a throughput of 250,000 t/y, would reach abt. 13,500 MWh/y. Assuming a price for electricity of €0.12/ kWh, this represents a savings of 1.6 million euros per year.
Figure 5 and Figure 6 show the potential reductions in CO2 and NOx emissions, as well as savings in electricity, as a function of the annual throughput.
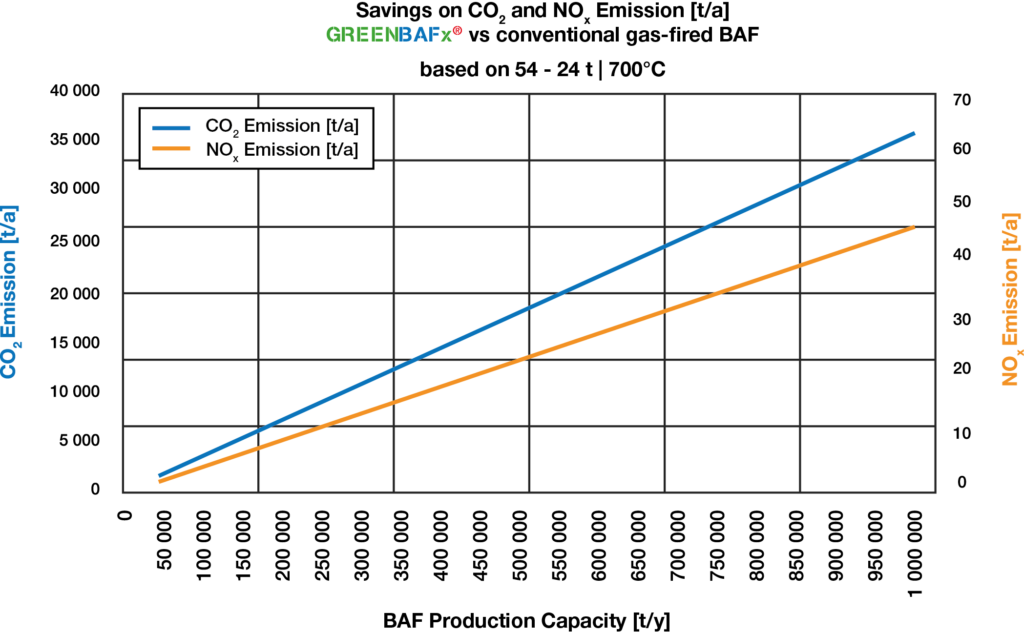
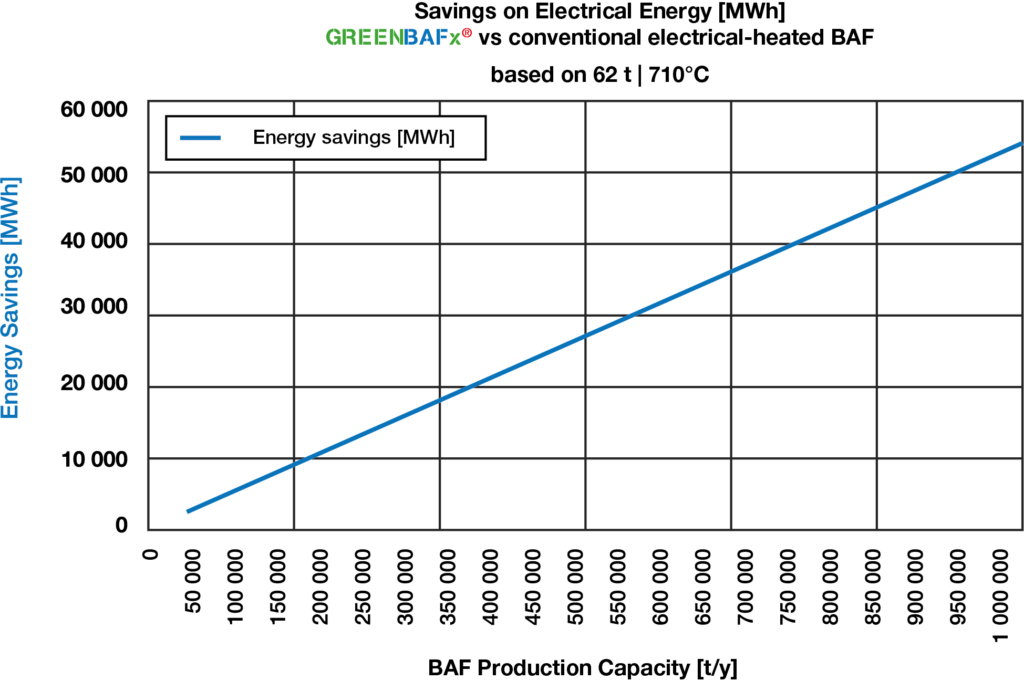
- A GREENBAFx® facility with a throughput of 250,000 t/y reduces emissions by ~ 9055 t of CO2 and ~ 11.8 t of NOx per year
- Energy savings of up to 5 % due to direct heating (“basic” case)
- Energy savings of up to 30 % due to heat exchange (“advanced” case)
- Reduced power draw (abt. – 5 %) compared to standard bell annealer facilities with electric heating
- Atmosphere outburner in heat exchanger circuit
- Air/water or air/oil heat exchanger
- Direct air heating (hot air is then used to heat the workshop, coil storage area, etc.)
- Tie-in to energy storage system
- As the gas transferring heat is not at an excessive temperature
- High-performance air cooling
- Integrated cooler
- Fast cooling system: integrated cooler paired with a high-performance air cooler
- There is no need for a supply of open cooling water, eliminating potential quality issues caused by water droplets on coils
- No utility couplings
- No bell exchange
- Operations are massively simplified
- Heat treatment cycles can be fully automated
- Only two (2) crane movements are required (place bell, lift bell) instead of the usual six (6)
- No waiting times for “busy” heating bells that may reduce throughput
- The heating type (electric, natural gas, hydrogen) can be freely selected in response to the availability and price of utilities (restrictions in bell handling and heat exchange may apply)
- Cannot be damaged during charging
- Due to reduced thermal stresses
- Even during the air cooling phase
- Reduced longitudinal distance between workbases
- Heat shields for valve stands are no longer required
- The heat exchange ducting requires roughly the same amount of space as exhaust gas ducting
- Many types of existing facilities can be upgraded with an integrated electric heating system and a heat exchange system
SUMMARY AND CONCLUSIONS
With the innovative development of a new generation of bell annealer facilities, during which a clear emphasis was placed on maximizing energy efficiency, eliminating emissions and simplifying operational processes, a significant step has been made towards creating a sustainable production method for the metals industry.
As stated above, the challenge has been to provide our customers with sustainable production methods, while still allowing them to remain competitive and maintain their positions in the international market.
The different variants in the GREENBAFx® line of bell annealers are available as financially appealing new facilities with attractive amortization periods, as well as upgrade packages for existing facilities.