Long-term partnership
/ Innovation & Technology, Success Stories
EBNER.blog | Karl Wohlfart & Sascha Eppensteiner, EBNER
Long-term partnership.
HUGO VOGELSANG of Hohenlimburg, Germany continues to place its trust in EBNER hardening and tempering technology.
Our cooperation with HUGO VOGELSANG GmbH & Co. KG goes all the way back to the 1980s. EBNER Industrieofenbau supplied the first hardening and tempering lines at that time, which were equipped with traditional molten-metal quenches.
Over the years, a number of innovative facilities were added that allowed new markets to be developed. To name just a few examples, these included a hardening and tempering line for thin strip, a vertical hardening and tempering line with HICON/H2Q hydrogen quenching technology and a high-throughput hardening and tempering line for wide strip.
A new challenge, however, has been the extensive modernization of two existing lines.
The different process steps used to harden and temper carbon steel strip and achieve martensitic, bainitic or pearlitic microstructures include heating up, quenching and – depending on the technology in use – soaking or tempering, followed by final cooling.
However, since the first EBNER hardening and tem-pering line was commissioned almost 50 ago, many details of the process and many of the requirements have changed. Throughputs have been increased, consumption has been reduced, the strip quality that can be achieved has been improved and, of course, processes have been optimized, increasingly automated and digitalized. For years, as the global technology leader, EBNER has been the driving force behind such innovations at these types of facility.
When HUGO VOGELSANG forwarded an inquiry to EBNER regarding modernization of the two still fully-functional facilities, it was clear that extensive and detailed planning would be required to successfully realize the project.
In cooperation with the customer, the following goals were established and successfully achieved:
- Improvement of the strip quality that could be achieved, by installing new HICON technological components
- Reduction of scrap material by automating operating and processing steps
- Increase of process reliability by replacing the electrical/automation systems installing a new VISUALFURNACES Process Control System (PCS) and installing an automated flatness control system (SmartFlat)
- Increase of the throughput capacity by optimizing existing facility components and eliminating bottlenecks
- Increased quality assurance by installing ShapeFlat flatness measuring systems at quality-critical points in the facility
- Consideration of the extremely small amount of space available, as well as the integration of current safety and environmental standards
INSTALLATION WHILE NEARBY FACILITIES CONTINUE TO OPERATE
Although installation and commissioning took place while parallel facilities continued to operate, both facilities were able to start production on schedule – despite the COVID-19 pandemic. This required a great deal of planning before on-site work could begin, and could only be achieved through close cooperation between EBNER and the customer. We would like to take this opportunity to thank the team from HUGO VOGELSANG and BILSTEIN SERVICE for their valuable support during the project.
STRENGTHENED MARKET POSITION
HUGO VOGELSANG, a member of the BILSTEIN Group, has been one of the world’s leading manufacturers of hardened and unhardened high-quality and stainless steel strip for many years. Its products find use in a wide range of applications, such as those in the band saw, spring steel and tool industries. With the modernization of the two hardening and tempering lines, the customer’s market position was strengthened even further.
EBNER looks forward to continued close cooperation, and the shared implementation of future projects employing advanced technologies.
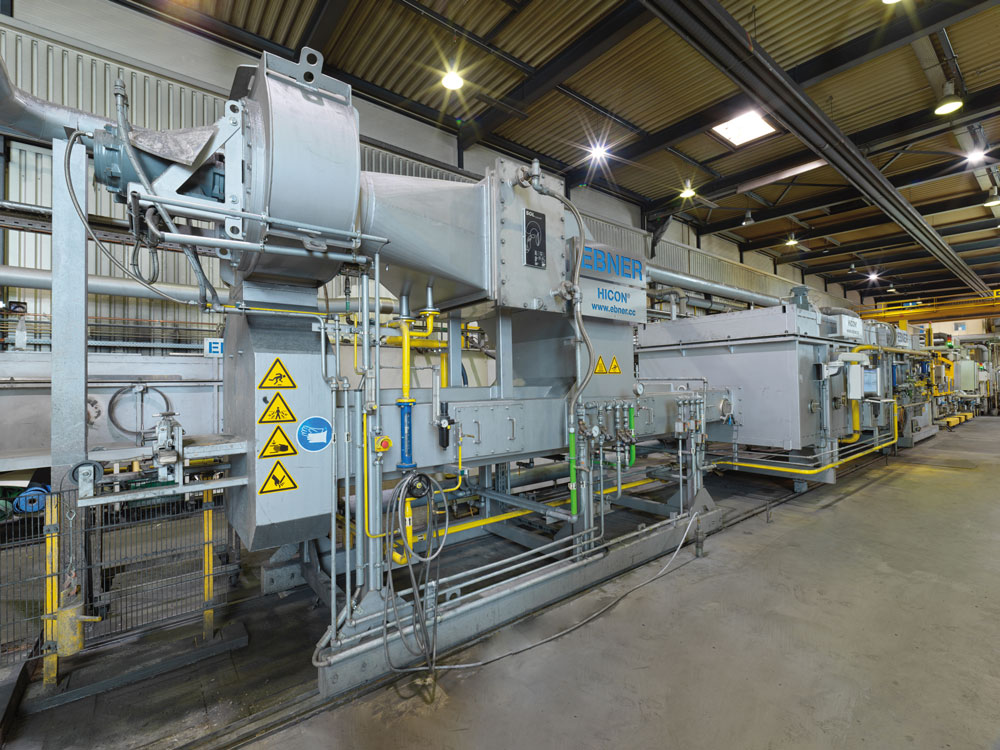
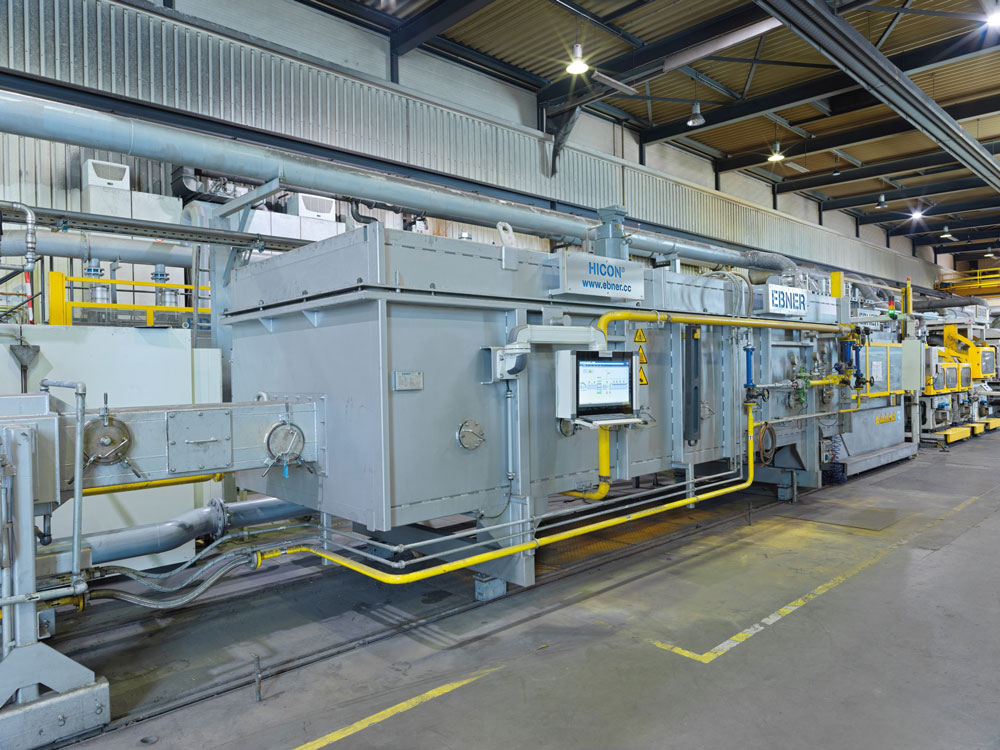